Designs and Projects Development designs and develops products a variety of products focusing on haptics and mobile robotics. They have haptics based products targeting surgery simulation, mission control, and assembly operations. The products designed here, are then sold though another concern, Merlyn D3 Systems.
Mr. Biju Ronnie Varkey, Owner, Designs and Projects Development, talks to Abhishek Mutha of EFY, about haptics, and challenges faced while designing advanced bomb-disposal bots.
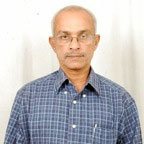
Q. Could you start off by giving us an overview of your organisation?
A. Designs and Projects Development designs and develops our products, and then we sell this product under the name of Merlyn D3 Systems. Merlyn D3 Systems can be called an innovative arm of Designs and Projects Development, and is a company where we market our range of mobile robotic devices, which can be plugged together to form any type of device.
Q. Currently, what is your R&D team working on?
A. Right now our main focus is developing sub-systems for haptic devices for which we have our own mechanical tool room, electronic development center, and software development lab. We are also coming up with other technologies as well. The two focus points for us are haptics and mobile robotics. Mobile robotics is a device for harsh terrain which can move in any direction – it’s used for bomb disposal. Haptics technology is being used for surgery simulation, mission control, assembly operations, and many more areas.
Q. How would you explain haptics to a newbie? Why is it gaining importance?
A. Today we are in a phase where haptics is necessary. For example when an arm in a robotic device is attached with a tool like a drill, and a suitcase with an explosive device is being drilled, then the amount of force required to drill through it is very important for a very safe disposal. Otherwise, the damage caused can be very huge. The force applied by the robot has to be felt by the operator otherwise there can be possibility of tremendous damage. If there is a haptic feedback, the operator knows exactly how the arm and the tool are operating and also the forces that are involved.
Secondly when a trigger is being removed from an explosive device, it’s important to know the pressure being applied by the gripper. Too much force might cause an explosion and too less will make it impossible to extricate the trigger. There should be a very precise control where in the operator should feel that he is at the site performing all the operations. We are also using this technology in surgery simulation also.
Q. How does haptics work?
A. Take the simple example of riding a bicycle. We sense so many factors including the position of our body, the speed, the rumble of the road, the wind on our face, the exhilaration of gliding, the force we apply on the pedal and the effect it has on acceleration. Try doing that on a game console on your PC. You now know what you are missing.
According to medical science there are more than 28 different types of sensors in our human body. These sensations can be used as a feedback mechanism to add to our feel of our action as to its implementation by the machine being controlled by us.
Haptics is the science of feel for our perception senses so that our body can experience the result of our actions to control a robotic system. In a haptic system the end effector is attached to sensors to detect the process being undertaken. The force and orientation data is fed to the controlling device and the action is mimicked so that the operator can feel the effect of the actions being given through controlling device.
Traditionally the feedback was limited to the sense of force that is being applied by the end effector on our robotic system. So the force that is being applied is fed back to another robot actuator system that is integrated to our control device like a joystick. The feedback would be in a ratio as decided. It can be amplified if the force applied is very low so that the applied force perception is detectable. It can be as a lower ratio if the forces being applied by the robot are high.
The above definition of haptics will also allow a camera and display system attached to a robot to be called a haptic device as the operator guides the robot while viewing his actions. This form of haptics would be called a visual haptic system as the visual perception is used to control the robot system.
Q. How is the technology advancing?
A. As technology is advancing more types of human perception are being used to function as a control feedback methodology to actively guide the robotic system. Sometime they are also being used as combination to achieve more complete involvement.