Everything today is smart, smartfactories, smarthomes and smartcars. Our devices, cars and appliances have become more efficient, are able to process faster and can deliver more features. At the core of these smart devices are the chips that make these devices work. Shinichi Yoshioka, vice president and chief, Automotive Analog and Power Systems business division, Renesas Electronics Corp., speaks with Rahul Chopra of EFY
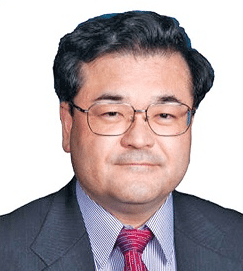
Q. What is driving the future of microcontrollers (MCUs)?
A. Technologies shaping the future of MCUs provide higher performance and larger embedded memory sizes such as flash and static random access memory. Better power saving technology is also enabling performance enhancement, while boosting up the operating frequency of the chip. Moreover, process technology enhancement towards finer nodes such as 40nm and 28nm are also driving chips into the future.
Q. How do advanced process technologies and complex digital hardware circuits on MCUs help embedded system designers?
A. It allows them to reduce external components and achieve lower costs due to smaller PCB sizes. This is because of higher integration offered by the nanometre-level manufacturing process and improved performance that this process enables on the chip.
For example, Renesas offers a digital power controller block in its RX63T MCU. The DPC is a 16-bit fixed-point digital calculator that calculates compensation values for use in the digital control of switched-mode power supplies. The control algorithm adopted for the compensator provides greater stability than a proportional, integral and derivative compensator.
In addition, this manufacturing process provides benefits like lower power consumption, more on-chip flash and RAM, and better yield in manufacturing of MCUs.
Q. What technology trends are driving improvements among power management components?
A. As systems have become more power-efficient and compact, demand has grown for power supply blocks with improved power efficiency delivered in a compact form factor. We have contributed to the reduction of power supply design workload with new on-chip functionalities including auto pulse-frequency modulation and battery backup functions.
By reducing the power supply design workload, the new devices improve the compactness of the overall system for improved power efficiency and lower bills of material cost. Power supply system miniaturisation and lower costs are achieved by integrating a switching regulator, low dropout regulator, battery backup function, on-chip sequencing function and protection function in the same package.
Q. What is the difference between software and hardware intelligence in power devices?
A. Protection mechanisms against over voltage and temperature-sensing circuits are embedded in power devices to make these intelligent. Software control by MCUs can be more sophisticated and complicated but much slower than those enabled by the intelligence embedded in power devices. Both controls are needed to realise competitive systems.
Q. How do you see the arrival of silicon carbide (SiC) components affecting the market of IGBTs and MOSFETs?
A. We are preparing SiC technology, starting from niche applications that need higher voltage and larger current than IGBTs can support. The biggest challenge for SiC to replace IGBTs is its cost-competitiveness issue.
Q. Are there any other application areas that you see driving the demand for MCUs across the globe?
A. Industry applications such as robotics, motor-control and brushless DC motor-control applications should grow fast and drive the demand for MCUs and analogue and power devices as drivers.
Q. Do you feel that a lag still exists in technology flow between developed and emerging economies?
A. Yes, but the lag is narrowing now with costs of such technologies becoming more affordable and Indian purchasing power becoming higher.