Evolutionary robotics designs adaptable AI robots mirroring nature, investigating hardware impact and leveraging 3D printing for diverse bodies.
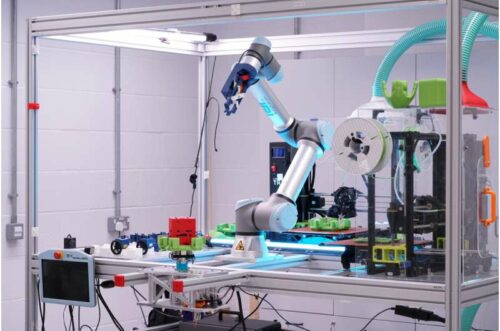
Evolutionary robotics aims to develop AI-driven “organisms” capable of adapting their abilities and configurations in response to their environment as humans and animals evolve, adapting their skills and appearance over time. Roboticists use AI for adaptable robots, but transitioning simulations to the real world poses challenges in maintaining performance.
Researchers at the University of York, Edinburgh Napier University, Vrije Universiteit Amsterdam, University of the West of England, and the University of Sunderland have examined the influence of hardware on the evolutionary development space of robots.
Autonomous Creation and Diverse Morphologies through 3D printing
The team devised a revolutionary evolutionary robotics platform, enabling the autonomous creation of varied robot “phenotypes” primarily through 3D printing, thus bypassing the costly and time-consuming manual assembly of numerous robot generations. This platform facilitates the development of different robot “species” with many morphologies and body structures. The cornerstone of this innovation is a semi-modular architecture that integrates a 3D-printed plastic skeleton with clip-on modular “organs,” providing essential functionalities such as movement, sensing, processing, and power.
Navigating Constraints in Evolutionary Robotics Development
The team created a system where a compositional pattern-producing network (CPPN) dynamically shapes the robots’ body and organ configuration with evolving parameters. Developing this encountered numerous challenges, including 3D printing intricacies and ensuring reliable interconnections in various robot setups. However, they realized the limited and complex exploration space their system provided for evolving robots, with many designs needing to be more feasible due to physical restrictions. It introduces the “viable phenotype space” concept, illustrating the limitations imposed by hardware implementation on a robot platform’s evolvable exploration space.
Beyond Simulations to Real-World Adaptability
The team noted that existing evolutionary robotics research, primarily based on simulations, frequently overlooks hardware limitations, leading to simpler prototypes and an easily navigable ‘viable phenotype space’. As the sector progresses towards solving real-world issues, the importance and complexity of this space are expected to increase. The team urges the careful development of this space to align with specific robotic functions and goals, emphasizing the need to tailor evolutionary algorithms for peak performance in the defined space. They caution against traditional design methods, which could restrict the evolution of practical robots, advocating for adherence to their principles to facilitate the creation of more adaptable and efficient evolved robots.
In the future, the researchers plan to pursue three research directions, all focused on optimizing evolutionary algorithms in the viable phenotype space. First, they plan to develop a strategy to lessen hardware limitations. Next, they will create a genotype blueprint and identify optimal strategies to navigate the viable phenotype space effectively.
Reference: Mike Angus et al, Practical hardware for evolvable robots, Frontiers in Robotics and AI (2023). DOI: 10.3389/frobt.2023.1206055