Discover the future of sustainable transportation with a single-phase power stage for traction inverters, powering electric vehicles for efficient energy conversion, precise motor control, and reduced emissions.
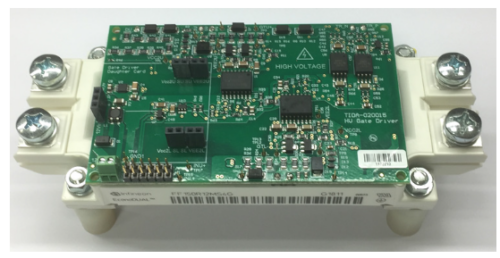
A single-phase power stage plays a vital role within a traction inverter, particularly in applications where electrical energy is transformed into mechanical propulsion, as seen in electric vehicles (EVs) and hybrid electric vehicles (HEVs). It offers cost efficiency by requiring fewer components, reducing manufacturing expenses. Its smaller physical footprint enables a more compact design, ideal for electric vehicles where space is at a premium. Additionally, the inherently lighter construction of single-phase power stages contributes to improved energy efficiency and vehicle range. Single-phase power stages are compatible with standard single-phase AC power sources, facilitating convenient and cost-effective charging options in regions with such infrastructure. They are also well-suited for low-power EV applications and can seamlessly integrate with existing single-phase electrical grids, simplifying the transition to electric mobility. Their precise power control benefits specific traction applications, resulting in smoother acceleration and improved ride quality.
The Texas Instruments reference design, TIDA-020014, presents a single-phase power stage designed for a traction inverter that seamlessly accommodates three 12-V car battery inputs. This innovation boosts EV propulsion by optimizing energy conversion efficiency and simplifying power source integration, benefiting electric vehicles, buses, and trains. It offers versatile bias supply solutions for hybrid and electric vehicles, generating 4.2 watts of power within an input range from 4.5 V to 42 V DC. The output configurations are +15 V, -8 V, or +20 V, -4 V, and an output current of up to 180 mA. The compact design seamlessly integrates with SiC/IGBT half-bridge modules, offering features like isolated gate drivers, remote DC bus sensing, temperature sensing, protection mechanisms, and diagnostics. These components enable comprehensive testing, including CMTI, double pulse performance, and high-voltage short-circuit behavior assessments. Additionally, a dual-channel isolated gate driver ensures precise control and protection for IGBT/SiC modules, with real-time monitoring of DC bus voltage and temperature for optimal performance.
With three distinct SiC/IGBT bias-supply solutions to power the isolated gate drivers, this design offers adaptability across various applications. Inverter and motor control, onboard (OBC) and wireless charger, gasoline and diesel engine platform, and DC/DC converter are key components in modern automotive and electrification systems. These components ensure efficient power management, control, and connectivity within vehicles. Inverter and motor control systems are responsible for the precise operation of electric motors, facilitating the movement of electric vehicles. Onboard and wireless chargers are essential for replenishing battery power, enabling convenient charging solutions for electric vehicles. Gasoline and diesel engine platforms continue to be integral in hybrid and internal combustion engine vehicles, offering a range of power options. DC/DC converters ensure voltage compatibility, enhance reliability, extend lifespan, and save space, making them crucial for automotive progress. The optocoupler’s absence contributes to efficiency in traction inverters.
Texas Instruments has thoroughly tested this reference design, which includes a Design Guide, Bill of Materials (BOM), schematics, Gerber files, Printed Circuit Board (PCB) layout, and more. Please visit the company’s website for further information on this reference design. To explore this design in greater detail, click here.