Bosch is a global supplier of automotive components and also caters to consumer goods and industrial automation areas. The overall turnover of Bosch is 51.58 billion Euros out of which around 59% comes from the automotive area, and the rest from the other two areas. Around 300,000 associates work worldwide in Bosch. At RBEI, there are more than 11,000 associates working in fields of software, hardware, mechanical, IT, and ITS.
Mr. R. K. Shenoy, Senior Vice President, Engineering Unit – Powertrain Electronics, BOSCH, recently spoke to Abhishek Mutha of EFY about the upcoming trends and challenges faced in designing electronic control units for automobiles
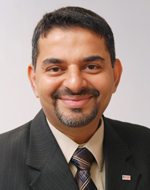
Q. In India, Bosch operates through six companies. Could you just brief us on the significance of these companies?
A. The largest flagship company of Bosch is Bosch Limited, which is responsible for Diesel systems, Gasoline systems, Power tools, and other domains including after-market. The second one is the RBIC, responsible for the safety systems onto the market whether it’s ABS, ESP (electronic stability program), or air bags. Moving onto the next one, RBAI(Bosch Automotive Electronics India Pvt Ltd ) is responsible for manufacturing these electronic control units for any domain of the automotive. Then we have the company which is into the field of drive and control technologies, Bosch Rexroth. We have RBDI in Chennai responsible for Electrical Drives. RBEI is the global supplier of technology and services, offering end-to-end Engineering, IT, and Business solutions.
Q. What is the most significant challenge faced in automotive electronics?
A. In car multimedia, as it is closer to consumer electronics, the challenge is to bring in the change at a much faster rate. This is due to the fact that innovations in consumer electronics are happening at a much faster rate than probably the rate at which we would be able to deploy systems on a vehicle.
The difference is mainly because of safety and security concerns as well as liability issues in a car. We have to be 100 per cent sure that what we deploy onto the car fulfils these norms to be safe and secure for the user. For example, now we have ISO 26262 norms coming up for data safety. When talking of a safe system, car multimedia may be classified differently from a safety system like ABS or ESP. Nevertheless, the challenge in this vertical is to ensure that we have a right balance on the time-to-market.
Q. How do you reduce the development cycle?
A. It is not just a question of the amount of effort being put in but a smarter way of engineering and validating the product by utilising accelerated ways of doing the testing. In power train and safety vertical, we see to it that the product made is safer while the development time is reduced to, say, one or two years to deploy the new system. That is where we have ensured at RBEI that we not only have a team that engineers the software but also a team developing hardware—even the mechanics of the electronic control unit (ECU).
We wanted to ensure that we had a complete EMC Lab where we could test the electronics. This was a big investment made. Each one of these labs cost more than two million Euros. At our lab in Coimbatore, we are able to test whether the electronic components can withstand all the electromagnetic (EM) interferences, while ensuring that these components don’t emit so much EM waves that other ECUs become unoperational in the vehicle. Thus we had to do it both ways. We cannot have vehicles performing differently when they go close to a TV tower, a satellite reception area or even a mobile phone tower.
Reliability is another challenge. When the product is incorporated into a vehicle, it should withstand different temperatures, vibrations and humidity. So the product is tested in a reliability lab where we put it through such tests as thermal shock. Once testing is done, we are able to reduce the development life-cycle by directly doing engineering, having the samples, doing the testing and finally ensuring that we are able to release them for production.
Having a production line is beneficial as we are able to test whether the product developed is easily manufacturable. If there are any issues during manufacturing, we are able to solve them quickly.
Q. The number of ECUs per car is increasing. What are the major advancements in this area?
A. In high-end cars, there are over 60 ECUs, including the body electronics and smaller ECUs. Reduction of CO2 emission primarily starts with engine management. We try to optimise the engine performance by having a more advanced software that runs on these control units and reduces fuel consumption.
Then there is connectivity. For example, when there is connectivity between ECUs, more information flows from navigation system into the power train, running the engine more optimally. Safety can also be improved with connectivity between navigation and driver assistance systems, as the information on an accident or other situation on the road can be used effectively in the car.
The connected vehicle is becoming a hot research topic, eventually leading to a lot of development. Connectivity not only helps to use information between the ECUs more effectively but also to communicate between vehicle-to-vehicle and vehicle-to-infrastructure. By having this information we can actually make a vehicle perform much better, both in terms of fuel consumption and safety.