Designed for automotive applications, the design is tailored for high-voltage systems within HVAC compressors, featuring isolated communication setups necessary for safe and reliable operation.
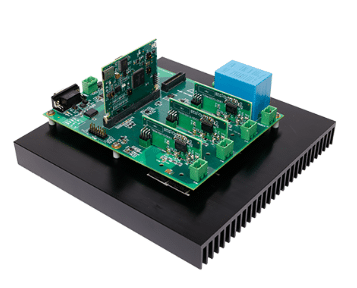
The TIDM-02012 by Texas instruments is an advanced 5-kW reference design optimized for high-voltage HEV/EV compressor applications, prominently known as eCompressors. It is powered by the mid-performance C2000 TMS320F28003x real-time microcontroller unit (MCU) from Texas Instruments. This reference design is compatible with 400-V and 800-V DC-bus systems, accommodating the current shift towards higher battery voltages in the automotive industry. Central to this design is its controlCARD-based framework, which not only facilitates the evaluation of various MCU and gate driver combinations but also ensures scalability. This feature allows for the integration of other devices from the C2000â„¢ portfolio, including future devices aimed at addressing the increasing demands for cybersecurity, functional safety, and compliance with evolving automotive market standards.
A significant aspect of the design is its adoption of the MathWorks Model-based design approach. This methodology expedites development processes, reduces the demand on engineering resources, and eliminates the need for in-depth software expertise. It achieves this by separating control algorithm development from firmware programming, allowing for easy portability across different families of C2000 MCUs. Additionally, the model-based design supports offline development, tuning, and validation of control algorithms, enhancing development efficiency. The motor control software development kit (SDK) features example models from MathWorks MATLAB & Simulink, incorporating the C2000 microcontroller blockset, motor control blockset, and embedded coder. These tools provide a comprehensive framework for developing advanced motor control applications, facilitating the integration and customization of the software to meet specific system requirements.
The reference design offers various advanced features to enhance functionality and accelerate market readiness. It includes Sensorless Field Oriented Control (FOC) powered by InstaSPIN software and the FAST observer for precise motor management. The hardware and software solutions provided are pre-tested and ready for immediate deployment, streamlining the path to market entry. Additionally, the design supports incremental software builds that allow for thorough verification of various software modules. It also includes features that support sophisticated motor control techniques such as field-weakening control, Maximum Torque Per Ampere (MTPA), overmodulation, and vibration compensation. The design is capable of operating across a wide speed range, beginning from an electrical speed of just 5 Hz, and offers support for CAN FD and LIN interfaces.
Robust motor overcurrent protection is ensured through on-chip comparators. Furthermore, a sliding mode observer integrated into the MathWorks model-based framework enables effective implementation of sensorless FOC. The system also features closed-loop speed control, phase over-current protection with an on-chip comparator, self-calibration of ADC offsets, and advanced simulation capabilities to facilitate the development and validation of control algorithms. The reference design encapsulates a holistic solution that not only meets current technical demands but also anticipates future needs in the rapidly evolving automotive sector.
TI has tested this reference design, which comes with a bill of materials (BOM), schematics, and other data. The company’s website has additional data about the reference design. To read more about this reference design, click here.