From research work to modern engineering processes, high rates of encoded information in multiple signals from simultaneous processes have forced data acquisition (DAQ) systems to evolve. This article gives you insight on the latest in DAQ systems
PANKAJ V.
Data acquisition is a process of acquiring information and documenting it in a meaningful way, to analyse a process or phenomenon. Data acquisition (DAQ) systems are usually used in applications that require data logging, control, test automation, monitoring and prototyping. Advances in electronics and information processing technologies have made these types of processes simpler, accurate, versatile and reliable.
What is happening to data acquisition
The most visible trends can be seen as the effects of transition to PC-based DAQ that started some time ago. Most earlier box instruments had processing built into them. Now, all that processing is being done inside computers, so the instruments are interfaced to a computer with analysis being done through computer software. Thus we see a more software-defined approach to DAQ, as well as the emergence of high-speed USB-enabled DAQs.
The other key trends are wireless DAQs connecting with user’s consumer electronics, which users can associate with using sensors, signal conditioning hardware along with flexible software and extensive DAQ channel counts. Integrated and multifunctional applications for modular PCI-based and USB DAQ systems are also gaining popularity due to their comparatively economical nature.
Let us take a look at some recent major developments in the field of DAQ.
Better interfacing options to keep up with DAQ system requirements
The industry is moving towards a trend of having a combination of modular hardware and flexible software. These newer modular systems have appropriate signal conditioning and analogue-to-digital conversion (ADC), with various interfacing sensors supporting multiple DAQ requirements.
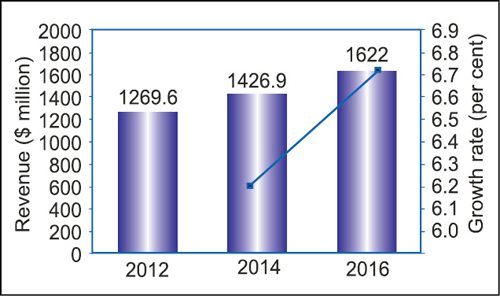
The plug-and-play signal conditioning systems improve accuracy and performance by simplifying sensor connectivity, removing noise and ensuring safety. The traditional approach used to be instruments performing specific DAQ tasks, which is not feasible considering today’s requirements.
Chinmay Misra, technical marketing engineer, National Instruments says, “A traditional DAQ system is equipped with a fixed user interface and in-built programmed software, and hence it is not capable of catering to multiple applications. This means that as soon as DAQ requirements change, the traditional set-up has to be completely revamped. With today’s advanced technology, as upgrade cycles grow relentlessly shorter and relentlessly more cross-platform, the traditional approach is neither feasible nor cost-effective.”
Software-defined, modular instrumentation is gaining popularity as it offers flexibility, scalability and higher speeds. A modular instrument is essentially a generic hardware that acquires and generates raw data while the software is stored on the user’s PC, which allows user-defined measurements, analysis and logging. A successful, software-defined DAQ system comprises modular, reconfigurable hardware platforms based on open industry standards, and a systems design software that can be used to easily define the functionality of the system.
Navjodh Dhillon, application engineer, Electronic Measurement Group, Agilent Technologies says, “Modular systems give you a facility of changing the module as and when required while making minimum changes to the overall DAQ system. They also allow you to put different kinds of modules in a small space, to make one integrated, unified system for DAQ purpose.
Today, DAQ is not just about only taking one type of measurement, it’s taking ‘n’ types of different measurements. For this you need an instrument which can have multiple kinds of modules that can be added to the instrument and still be able to take ‘n’ types of different measurements in a unified, integrated solution. This is how modular solutions help you out.”
Improved sensor accuracy using digital multimeter technology
Many DAQ systems now include digital isolators to protect the device, computer and operator from potentially hazardous electrical signals while improving measurement accuracy. This is done by breaking ground loops and rejecting error-causing common-mode voltages and other signal conditioning features such as amplifiers, filters and sensor-specific circuitry on new devices to further improve accuracy and simplify connectivity to common sensors.
Today, the major requirement for any DAQ system is to be as accurate as possible while continuing to be available at a minimal cost. For this, digital multimeter (DMM) based systems have come up. Many systems use DMM as the measurement instrument, which ensures minimum cost, and the measurements are as accurate as a standalone DMM would have.
Integrated signal conditioning
While the fundamental architecture of hardware has remained the same, the technologies used in various integrated components have evolved consistently. High-performance DAQ hardware with integrated signal conditioning have surfaced as next-generation solutions.
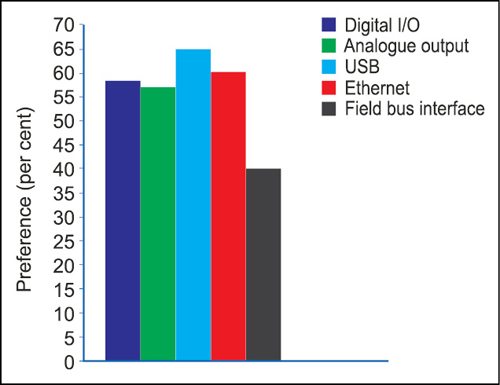
These solutions integrate DAQ and signal conditioning on a single module to provide high-performance, high-channel count and reliable sensor measurements. Most of such solutions are built around the industry-standard PXI platform, taking the advantage of the superior synchronisation and the high-throughput PCI express bus.