As public-private partnership in aerospace and defence catalyses indigenous design and manufacturing, test and measurement holds great potential from design to delivery in the Indian strategic electronics market. Test and measurement manufacturers provide sophisticated, state-of-the-art solutions to ensure quality and reliability of these equipment
SHWETA DHADIWAL BAID
AUGUST 2010: Aerospace and defence systems are very typical in nature and custom-built to serve the very purpose of the industry. To satisfy their stringent testing requirements, the test and measurement equipment need to be highly accurate and reliable.
The increase in indigenous design and manufacturing of aerospace and defence systems has resulted in a rise in the demand for high-performance, state-of-the-art test and measurement equipment. With public-private partnership initiative, there is a demand for commercial off-the-shelf (COTS) equipment satisfying military (MIL) standards in the strategic electronics segment.
“T&M equipment and solutions for aerospace and defence are based on advanced technology for their use in radar, electronic warfare, military communications, satellites, guidance, avionics, intelligence, surveillance and beyond,” shares Gautam Awasthi, general manager-marketing, Agilent Technologies.
“Cutting-edge technologies and advanced applications are very important for aerospace and defence, as the risks are high in these sectors. State-of-the-art solutions in T&M are available to analyse threats, signal integrity and frequency hopping in radio signals,” says Naresh Narasimhan, pacific technical marketing manager, Tektronix.
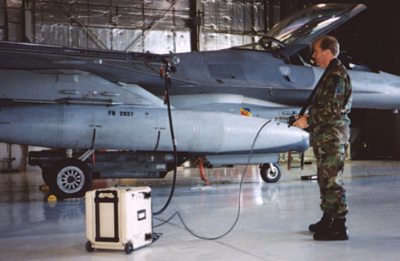
“Generally speaking, the requirements for military/defence and commercial aerospace projects are quite similar. Whenever health and safety are involved, the requirements are set at the highest level independent of the market being addressed,” informs Jon Semancik, director of marketing, VTI Instruments.
Adds N.V. Valsalan, director-business development, T&M and broadcast, Rohde & Schwarz, “Equipment manufacturers work collaboratively with the aerospace and defence industry to bring focused solutions that meet the exact requirements.”
Modular instrumentation and open standard instrumentation interfaces ensure availability of a wide range of commercial-off-the-shelf solutions for test and measurement in this segment. Today, a number of solutions are based on LAN extensions for instrumentation (LXI) and synthetic instruments (SI) that shrink test systems and enhance their longevity. Modular systems based on peripheral component interconnect (PCI) extensions for instrumentation (PXI) can benefit from widely available software and hardware components and easily connect with a PC to give high-performance results.
Industry’s stringent requirements
If we categorise the applications further into aerospace and defence, these are more or less the same as in other domains like telecommunication, electrical safety testing, security and surveillance, and microwave and RF testing, but the sensitivity and tolerances required are very high. The systems and components are designed and developed as per military standards and the test instruments are expected to measure as per the stringent tolerance levels and accuracies, and require calibration with standards.
Justifying this, S.R. Sabapathi, chief executive officer, QMAX Technologies, shares, “Typically, bonding testers used to test the aircraft body and instrument chassis resistance need to have accuracy of ±0.001 ohm and calibration to the standards of NPL.”
Semancik explains, “High accuracy and repeatability are key characteristics of these test equipment, making certain configuration elements essential, such as integrated signal conditioning, self-calibration, open transducer detection, noise immunity and stability. Some of the test environments can be quite demanding, exposing the instrumentation to high levels of acoustic noise, electromagnetic interferences, vibration and moisture. As a result, certain instruments must be sealed, conduction-cooled, splash-resistant and capable of withstanding extreme acoustic vibration.”
“T&M instruments are used mostly in fully automated set-ups and not as standalone equipment. For example, testing of avionics equipment needs a test bench with all measuring instruments in the same bus to do full testing of voltage, frequency, power, spectrum, etc,” shares Sabapathi.
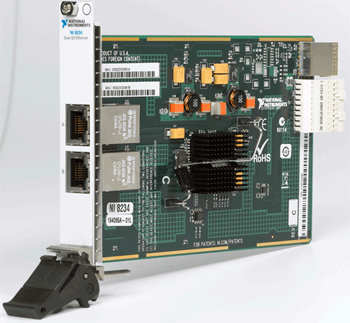
Avionics instruments used in aircrafts have to withstand extreme climatic conditions ranging from +40°C to -14°C (at 10,668 metres) and vibrations. So these need to be tested in simulated conditions at ground.
“For pneumatic and hydraulic systems used in aircraft controls, such as rudder, ailerons, wheels and brakes, we need special T&M instruments like data acquisition systems and other portable measuring instruments,” says Sabapathi.
“It is necessary to have each test thoroughly documented and the data archived for future reference. This involves capturing instrumentation identification details and calibration records,” adds Semancik.