Long before Fukushima, energy saving was a watchword. Efficient use of energy reduces the number of power stations. The conventional filamentlamps are problematic because of their low efficiency On the other hand, energy-saving CFL lamps too are not without problems due to their mercury content. For this reason, advances in light-intensive white LEDs are welcome. These offer an additional advantage—long life. With proper cooling, LED lamps have a life expectancy 50 times greater than filamentlamps. However, these might not be within design trends when they finally reach the end of their life-cycle!
With life expectancy approaching 50,000 hours for LED lighting, their service cost tends toward zero. One only has to consider the cost involved in replacing the lamp. The introduction of electronics into lighting technology has transformed it into a system, which offers energy savings along with substantial reductions in service cost. This is conditional on a balanced adjustment of the LED, the driver and the cooling. This system, however, is only as good as its weakest link.
Electronics posing challenges for designers
Designing highly efficientLED-based lighting systems confronts the designers with electronics issues. LEDs are semiconductors that operate with low DC voltages. To turn these into lights with a high life expectancy, designers have to pay attention to selecting the optimal LEDs and combining these with the right power supply and optimised cooling. The individual components determine not only the quality of the emitted light (what we see and feel) but also the efficiency and life expectancy o the complete system.
Cooling—the central aspect
It is widely believed that LEDs do not heat up. In fact, these radiate very little heat, quite in contrast to filamen lamps. Converting electrical current into light generates heat in the confined barrier (depletion) layer. So cooling or heat management is an important aspect as high temperatures in the depletion barrier have a negative impact on the life of the lamp. Heat sinks must be suffciently big, so that the temperature on the surface of the LEDs doesn’t exceed +75°C.
Good heat management and maintaining the temperature of the depletion layer continuously at 80°C makes it possible to increase the life expectancy towards the magic 100,000 hours limit (Fig. 1). An additional advantage is that a maximum temperature of +55°C on the heat sink of a lamp poses no injury threat to the user. Meanwhile there are a multitude of heat sinks in various forms and sizes available, which leave the designers with many options.
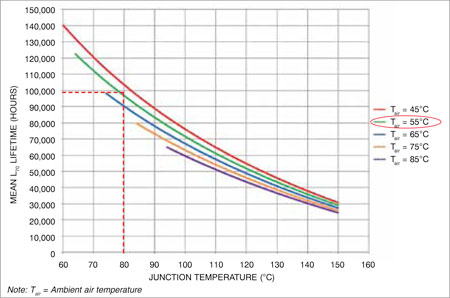
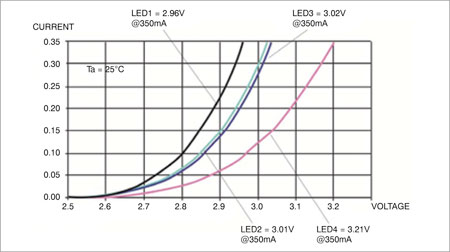
Fig. 2 shows the current-voltage curve of high-power LEDs. If you choose a supply voltage of, say, 3V LED1 is over-driven, LED2 draws 300 mA, LED3 draws 250 mA and LED4 draws only 125 mA. Furthermore, theses curves are dynamic. As the LEDs warm up to their operating temperatures, all curves drift to the left (the forward voltage (VF) reduces with increasing temperature).
The driver is critical
Although LEDs have been around for decades, their use for lighting has been discovered only recently. Quite contrary to display applications with individual LEDs, it becomes paramount that the rating graphs match while connecting a string of LEDs for lighting purposes. Connecting several LEDs in parallel to the same voltage source leads to different degrees of brightness. The human eye is very responsive to this, particularly, at low light intensity, so a solution was required.
Manufacturers could, of course, select LEDs for identical threshold voltages. But since they already select LEDs for different colour temperatures (binning), this would be an exceptionally expensive process. Some manufacturers focus on constant-current power supplies, which use the principle of brightness of individual LEDs being proportional to the current flow,irrespective of the threshold voltage of individual diodes.
Which outlives the other—driver or LED?
Many products in daily use are ‘service-free.’ For example, when the batteries of an iPod reach the end of their life (about five years), it is usually tim to switch to the next generation product. The same can be expected in the lighting area. Selecting the right LED driver is important for the reliability and life time of the lighting system. 50,000 hours of lighting is an extremely long operating life—equating to seventeen years at eight hours daily. By then the lamp is amortised. However, what happens when the driver packs up after only a few years’ operation?
The logistics alone can be very costly for the manufacturer, besides the loss of image. It is therefore not economic to just consider the price. Specifications o different manufacturers are similar at firstglance. What differentiates these is the life expectancy. Many data sheets focus on the mean time between failure (MTBF), which provides only limited information about the quality of the product. For one, it is a calculated value that is based on individual components and refers to the time between two failures, and does not take into consideration deficiencies in manufacture.