When it comes to selecting a new cleaning process, I feel sorry for the poor production engineers. Engineers are always expected to clean more boards while using less machinery, water, electricity and money. It is a tough bind, for two reasons.
First, electronic circuits are getting smaller and denser, which makes cleaning the circuit boards difficult. The boards feature many different types of contamination, including fluxes, glues, inks, epoxies, fingerprint oils and conformal coating residues. Usually, the cleanliness standard is very high, which makes the analysis even more difficult.
At the same time, manufacturers around the globe are being asked to change their processes to protect the environment.
Air, water and soil issues
Some of the world’s most polluted cities are in India, according to the World Health Organization, and Kolkata ranks No. 2 in the World Pollution Index. But India is not the only country with environmental problems:
1. In the Philippines, there are nearly 5000 premature deaths each year due to respiratory and cardiovascular diseases from exposure to poor air quality.
2. In Jakarta, more than 300 million cubic metres of water are pulled from aquifers each year—about three times the rate of replenishment. Indonesia is bound to face a serious scarcity problem within three to five years unless an immediate action is taken to conserve water.
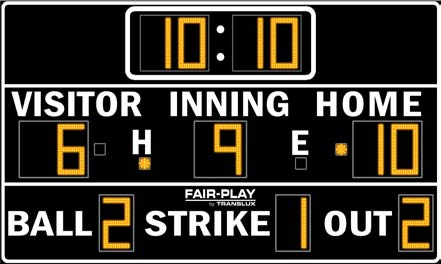
3. In Vietnam, only 4.26 per cent of all the industrial sewage and waste water is treated before being released.
4. Simple energy efficiency should be a goal everywhere. But Switzerland produces $9293 of domestic output for every tonne of CO2 released into the atmosphere whilst Thailand produces only $760/tonne and India produces $579/tonne.
This is not sustainable. Sooner or later, businesses will be required to pollute less and become more energy-efficient. In terms of cleaning circuit boards, the new requirement is for a cleaning process that is effective, consistent, versatile, safe, fast, sustainable and affordable.
A number of companies around the globe offer innovative, affordable and effective circuit board cleaning systems that minimise pollution and costs. But capabilities and costs of cleaning systems can differ dramatically. Look at just two contenders: water cleaning versus solvent cleaning. Aqueous cleaners are relatively slow but inexpensive, while vapour degreasers are fast but require expensive solvents. How can an engineer compare these disparate technologies in a fair and meaningful manner?
The answer is to use a procedure that balances the benefit of each option against its costs. We call it the ‘cleaning scoreboard.’
The cleaning scoreboard
When people talk about football, basketball or other ball games, the final score pretty much says it all. The same is true with electronics cleaning. Engineers can develop a cleaning ‘score’ that compares all the different cleaning technologies—aqueous cleaners, semi-aqueous cleaners, hydrocarbon cleaners and vapour cleaners–and makes meaningful comparisons between dissimilar systems. The best cleaning score is the lowest total-cost-per-part-cleaned (CPPC).
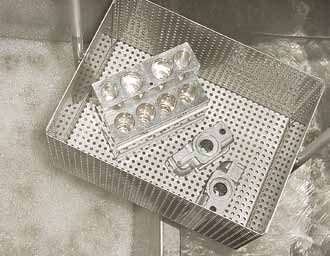
CPPC is a number, ranging from hundredths of a rupee to hundreds of them. This score summarises all of the direct cleaning costs, environmental inputs, labour costs and waste disposal costs into one simple question: how much does it cost to clean a single part? This cost becomes the tool that allows the savvy engineer to compare totally different cleaning technologies fairly.
So here’s the crucial teaching of this report: stop caring about prices. It is not the ‘rupee-per-litre’ that really matters; it is the ‘total-rupee-per-part-cleaned.’ That is where profits will be made or lost.
For the purpose of this discussion, the cost-per-part-cleaned rating is the most practical. However, customers may prefer cleaning-cost-per-day or cost-per-shift as an equally effective metric of efficiency. In general, boards-per-hour is optimal for most companies because most of the other operational expenses are either recorded as hourly numbers or can be easily converted into hourly costs.