Through automated manufacturing, the railway and airway sectors will realise efficiency, capacity and cost benefits of Industry 4.0.

There is no established path for success of any emerging technology, but creating a roadmap can help the rail and aviation industries to bring a more digital and connected future. The need for these industries to be smart is there because Industry 4.0, or the fourth generation of industrial activity, ensures reliability and safety to these sectors. With automation of the manufacturing industry, these sectors will realise efficiency, capacity and cost benefits of Industry 4.0. Enhanced industry-wide condition monitoring will also help reduce unplanned maintenance. Both sectors are in constant search for improvements to deliver better and secure customer experience.
Transportation systems are complex with respect to technology and operations due to the involvement of a wide range of human actors, organisations and technical solutions. There is a need to apply intelligent computerised systems for the operation and control of such complex environments, such as computerised traffic control systems for coordinating airline transportation.
Industry 4.0 is enabled by smart systems and Internet-based solutions. Maintenance is one of the application areas of self-learning, and smart systems can predict failure and trigger maintenance by making use of the Internet of things (IoT).
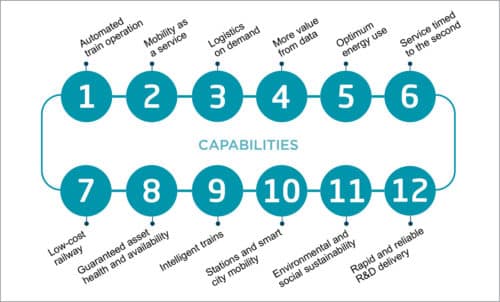
Digital railway solution
The digital railway programme is focussed mainly on digital signalling technology, which aims to enhance safety and speed up train movement in a congested network. If all data from signalling, rolling stock and passenger traffic control systems is brought together on a common platform, the entire network will be able to communicate seamlessly and instantaneously. The key to digitisation is interoperability of systems while retaining a critical approach to data security.
Rail service information could even be integrated with other transport modes, such as bus and taxi services, to guide passengers through smooth door-to-door journeys. Holistic data management could lead to the transformational change in real-time intelligent traffic management and in-cab signalling. This could improve customer satisfaction, with station information systems and personalised messaging providing passengers with all the relevant information they need.
Digitisation of railways includes:
- B-scan ultrasonic rail flaw detection (both non-stop and stop-and-verify systems) and track inspection with automated high-speed test trains.
- Train control system levels 2 and 3 for high-density routes to increase network capacity and maintain the required safety standards.
- Increased surveillance of personnel with both interior and exterior locomotive-mounted video surveillance to improve monitoring.
- Track-laying machines for mechanisation of construction.
- Electrification through machines such as self-propelled overhead electrification laying trains.
- Complete train scanners for improved diagnostics and maintenance.
- Use of distributed power to improve the efficiency of train operations with coordinated acceleration and deceleration.
- Establishment of smart railway stations by implementing access control at entry points.
- e-ticketing with services such as infotainment and app-based systems.
- Use of training simulators and virtual reality (VR) training systems to improve personnel capabilities.
Digital twin—the digital platform for railways and airways
A digital twin refers to a virtual replica of a physical asset, like an aircraft engine or a rail engine. It is a vital element of the digital rail solution that is continually updated as per the rail network. It enables engineers to test detailed what-if scenarios that could help in decision-making around the planning of enhancement and maintenance programmes. It could identify the most-valued solution that would have the greatest efficiencies and minimise disruptions.
Every year unplanned maintenance, flight delays and cancellations cost millions of dollars to every airline. Optimisation of operational availability can reduce operating costs due to maintenance. Monitoring engines in use with a digital twin can help airlines achieve this. A digital twin can display how the engine is running to engineers on the ground, while the aircraft is still in the air. Later, it can be linked to IT systems to help streamline and optimise maintenance processes and operational availability.
For each asset, engineers compile thousands of data points specifically during the design and manufacturing phases of the engine. These are then used to build a digital model that tracks and monitors an asset in real time, providing essential information throughout an asset’s lifecycle, such as engine temperature, pressure and airflow rate.
These virtual models of the assets can provide early warnings, predictions and even a plan of action by simulating what-if conditions based on weather, performance, operations and other variables. This way these models help keep the aircraft in service for longer.
Role of sensors in predictive maintenance
Sensors are constantly getting cheaper. This will increase their implementation as a leading real-time data provider. Sensors use a reaction-based approach to manage and maintain an asset and maximise its use potential. A wide range of sensors is available to collect huge amounts of data from all possible systems of a single train and then analyse it in real time to detect problems before these actually occur.
Constant monitoring of equipment through the measuring of all relevant variables such as temperature, vibrations, oil levels and the like help anticipate the optimal timing for maintenance. It enables identification of faults proactively and elimination of necessary maintenance interventions. Predictive maintenance is a powerful tool that helps track asset health, reduce unplanned downtime of equipment and minimise the high cost of unscheduled maintenance.
Optical and tactile sensors such as light curtains, camera systems and dynamic pressure-sensitive mats are suited to monitoring areas near rail vehicles. Good internal communication, fast reactions based on equipment geolocation data, high-quality maintenance planning and regular interventions are required to keep massive rail networks working.
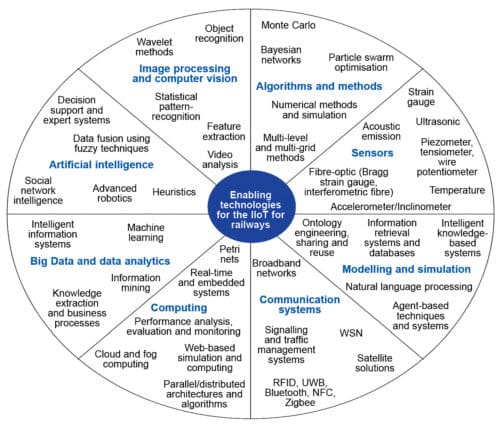
Predictive maintenance and CMMS for improved railway asset performance
Modern, next-generation asset and maintenance management starts with the adoption of a smart computerised maintenance management system (CMMS). Reliable railway maintenance is required to improve critical issues like safety, delays and overall system capacity. It is expected to rely on smart transportation systems and interconnected solutions such as predictive maintenance.
An interconnected CMMS can help maintain, manage and connect tracks, terminals, rolling stocks and communications infrastructure. It can identify maintenance issues before these impact safety, operations or revenue. It collects, stores and analyses data to prevent breakdowns and issue predictive maintenance algorithms to extend equipment life.
A reliable CMMS should be user-friendly, fast, reactive and flexible. It should also have a mobile application for anytime access, connectable to ERPs and IoT systems, geolocation tool, an analytical tool that supports unrestricted media upload and so on. Different departments such as accounting, operations, purchase and maintenance should also be connected to the entire communication platform. It can work as a network for manufacturers, technicians and suppliers to exchange expertise and speed up operations. Advanced CMMS analytic tools enable organisations to analyse data with great speed and accuracy, to optimise availability and increase the life of assets.
The IoT-connected trains
The IoT can interconnect all objects and devices that were previously not part of a network for predictive analytics. Its application increases safety, efficiency and ease of use with train management systems. Control and surveillance systems reduce the risk of collisions and regulate speed. Advanced consumer technologies help maximise connectivity and allow passengers to continue their activities on smart devices while travelling. Train-to-train communication through the cloud enables operators to transmit data about equipment, tracks and stations among themselves.
The IoT enables monitoring of areas on railway crossings remotely, such as barrier operations and end positions, switch end positions, space between barriers, system operations, connections and signals. This allows users to accelerate their projects, from engineering and runtime to maintenance with fast detection and localisation of errors and faults.
Big Data analytics for smart railways
The complete Big Data architecture includes the IoT and cloud computing devices. These work together to create smart railways that have self-learning capabilities to predict failure, make diagnoses and trigger maintenance actions. The architecture utilises multiple data sources to extract relevant information. It helps users to know what happened when, so they can go back and do the root cause analysis from the data, and take appropriate corrective action.
Big Data analytics in railways lead to predictive analytics and make decisions based on huge amounts of data. These involve data collection, analysis, visualisation and decision-making for assets.
Estimation of the remaining useful life of an asset to ascertain the probability of its mission accomplishment is key to the success for any organisation. The railway domain can achieve data interconnection via the train bus where most railway sub-systems and their respective sensors are accessible for global optimisation.
With the increase in demand for more passenger rail services and greater volumes of cargo trains, use of data and its analysis will become a primary asset for the railway sector. Millions of data points captured from sensors on critical train components will help detect impending part defects, ensuring maintenance before a defect occurs. This will improve reliability of the system infrastructure for many years by remote monitoring of location and condition of all vehicles.
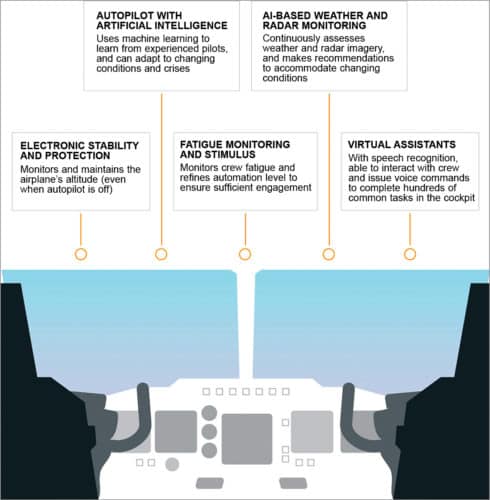
More technologies to meet needs of the railways
Researchers at Siemens Corporate Technology have developed a technique known as frequency-selective coating of window panes to solve the problem of low mobile Internet signals. These panes are provided with a transparent electrically-conductive layer consisting of metals or metal oxides. Metallic coating of the windows is vaporised along lines in a special structure by a laser to pass certain frequency ranges unobstructed.
The VR lab at GE Transportation’s John F. Welch Technology Centre, Bengaluru, facilitated a 3D VR environment for inspection. It tracks the motion of inspectors through specially-designed wearable goggles and infrared (IR) cameras placed in the room. The VR controller allows users to interact with individual components. The environment helps teams at different locations collaborate and review products that are under development. The lab can also be used as a training ground for service engineers who work on products in the field.
Locotrol distributed power system is a control and communication system that enables coordinated braking and traction power distribution between lead and remote engines for faster stopping times and shorter stopping distances. Locovision system through superior image quality cameras and real-time data processing monitors wayside assets, measures track gauges and detects intruders. It stores all information in a hardware infrastructure to help avoid major asset repairs and fines. The rail integrity monitor employs innovative technology with mounted sensors under the locomotive, continuously testing rail integrity in real time.
Automatic train control systems continuously monitor all train movements to provide fail-safe signalling. Operation of railways is centrally-monitored and controlled through operations control systems. Supervision systems, such as CCTVs or emergency telephones, also contribute to safety and enhanced comfort.
Signalling systems and railway automation solutions are crucial to detect and signal whether line sections are clear or occupied. There are three grades of automation and train control systems, namely, partially automated (supervised by a driver), highly automated (reduced driver supervision) and fully automated (the system is responsible).
Airways technologies and automation
The year 2019 looks to be the era of digital transformation with technology becoming a part of everyday life within all industries, including air transport industry. The airline industry is constantly evolving and adapting to new consumer habits, expectations and requirements for better safety and security. Technologies and trends that we expect to play the most important role in reshaping the air transport industry in 2019 are:
Biometrics
Biometrics-enabled self-service boarding gates, where your face becomes your passport, have been implemented at the entrances of many airline lounges. Integration of this technology into signages and flight information display systems is used to serve passengers with personalised information and offers.
Biometric technology can also be used onboard to facilitate seatback immigration and simplify in-flight payments. Airlines, airports and their partners are continuously working towards the goal of creating a biometrics-enabled single passenger token to offer effortless journeys.
Biometric technology such as fingerprint scanning or facial recognition on smartphones has also been adopted by airlines and airports to transform the customer journey. Fingerprint scanning for identification purposes to check in baggage could eliminate the need for boarding passes and cut down on the need for crew to be present to manually scan them at the gate.
Blockchain
Blockchain technology can eliminate the need to rely on physical ID proofs by saving passengers’ data maintained in a virtual de-centralised database. It can be extremely useful in building a robust security system for managing customer data by using a cloud-based document management solution. This will save time, money and resources in the long run, helping airlines become more efficient, safer and compliant. This data can also be used in increasing the operational efficiencies through predictive analytics.
Artificial intelligence
Chatbots can be used to answer simple questions, freeing up resources (human agents) for more complex customer service issues. Artificial intelligence (AI) also holds potential in a number of other areas, such as real-time predictive pricing, predictive aircraft maintenance and operational efficiency on the airfield.
Travel experiences can be daunting when you are in an unfamiliar environment and do not speak the local language. This could be solved by AI and machine learning (ML) technologies with translation apps and devices.
Robotics
Robots can assist in various tasks from transporting luggage to proactively identifying potential security risks. Customer-facing robots can provide on-the-spot assistance to passengers like customer management, car parking and so on. Baggage management can also be improved with re-usable electronic bag tags and door-to-door pick-and-drop facility.
Beacon technology for indoor positioning systems. Beacons can make navigation easy for travellers between different terminals at the airport. It can also help to know where passengers are and send them personalised and relevant information accordingly. This information can be about boarding gate number, baggage or flight status, or about the shops around.
AR and VR
Augmented reality (AR) allows passengers to use the camera on their device to view AR directions to wherever they need to go within the terminal. It helps them navigate the complex layout of airports.
VR-based apps can be used for training new crew members and engineers about engine mechanics.
Cybersecurity and cloud
Everything that airlines do to improve their digital touchpoints depend on the security of their IT systems. While technology leaders and industry stakeholders are working on a number of solutions, airlines should keep cybersecurity at the top of their priority list.
The IoT
Sensors can detect and report faults to maintenance teams on the ground, removing the need for the crew to manually do so. Addition of sensors to aircraft seats will enable the crew to monitor individual passenger health and well-being. Sensors such as hydraulic pressure and brake temperature provide real-time data to help predict early malfunctions or diagnose the remaining life cycle of the landing gear. Researchers are developing resilient ML-based autopilot systems that can adapt to changing conditions.
Airlines are using mobile platforms to connect with their customers throughout the journey, starting from booking of a flight to deplaning it. Deployment of connected objects can transform the manufacturing process with new tools and services that generate a drop in production costs and increase productivity. Overall, it can reduce both time and cost of maintenance.
Conclusion
With the rise of Industry 4.0, railway companies can now ensure that they are prepared to avoid the surprise of equipment downtime. The railway industry is on its way to integrate predictive maintenance and Big Data. Recent advancements in sensors and condition monitoring technologies have led to continuous data collection and evaluation, significantly minimising the number and cost of unscheduled maintenance.
Most significant improvements have been evidenced by more informative and user-friendly websites, mobile applications for real-time information about vehicles in motion, and e-ticket purchases and timetable information implemented at stations and stops. Airline technology is likely to evolve over time to the point where one crew member can handle a sizable chunk of a flight given an anticipated pilot shortage in the future. With automation a remote pilot on the ground will be able to take the second seat on a flight or flight segment.