Designs and Projects Development designs and develops products for a variety of verticals focusing on haptics and mobile robotics. They have haptics based products targeting surgery simulation, mission control, and assembly operations. The products designed here, are then sold though another concern, Merlyn D3 Systems.
Biju Ronnie Varkey, owner, Designs and Projects Development, talks to Abhishek Mutha of EFY, about haptics, and challenges faced while designing advanced bomb-disposal bots.
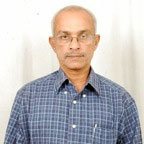
Q. Could you start off by giving us an overview of the company?
A. Designs and Projects Development designs and develops our products, and then we sell this product under the name of Merlyn D3 Systems. Merlyn D3 Systems can be called as an innovative arm of Designs and Projects Development, and is a company where we market our range of mobile robotic devices, which can be plugged together to form any type of device.
Q. Currently, what is your R&D team working on?
A. Right now our main focus is developing sub-systems for haptic devices, for which we have our own mechanical tool room, electronic development center, and software development lab. We are also coming up with other technologies as well. The two focus points for us are haptics and mobile robotics. Mobile robotics is a device for harsh terrain, which can move in any direction – it’s used for bomb disposal. Haptics technology is being used for surgery simulation, mission control, assembly operations, and many more areas.
Q. How does the robot recognise a bomb structure?
A. Once the bomb/suspected bomb is approached, two processes are performed. First, recognise if it’s a bomb and second, its structure. The first process is done by using a vapour sensor, which can smell the bomb. In about 50 per cent of the cases, the bomb can be smelt. Otherwise, we use a handy mobile X-ray unit, which is attached to the robot so it performs an x-ray of the suspected device. On this basis, it could be found if there is an explosive. Alongside these processes, the trigger mechanisms, location of the trigger or the detonator remote controller and things like that can be found. Once the location in the 3-dimensional space is established, then a call has to be taken on whether to dispose or diffuse the bomb. Diffusing is only possible if there is an idea about the trigger mechanism and if safety is not endangered. If in doubt about the trigger, then the suspected bomb is taken away from the current location to a safer location where even if it explodes it does not cause much damage. Usually these decisions are taken by the operator or at the HQ.
Q. What are the features required for a bomb-disposal robot?
A. In a bomb-disposal scenario, 70 per cent of the time is spent on positioning the vehicle near the bomb or the suspected bomb. Right now, the technology available gives us a tracked or wheeled vehicle, which has to be manoeuvred into the target site manually with a remote and a video link. We have developed a flexible chassis system where it flexes according to the terrain that is moving around. It takes a less amount of energy to move over big obstacles. We are also able to move in any direction without turning reducing the 70 per cent time to 20 per cent and move the payload without any type of vibration getting on to the payload on any type of terrain. Secondly, we are able to have a very precise manipulation which is possible once you retrieve the bomb.
Q. How is your system different from the other bomb-disposal robots?
A. In a normal system, the bomb is picked and carried out but the terrain may shake the bomb from the gripper. In our system, the arm picks up the suspected bomb but the terrain undulation is not passed on to the arm. So the bomb can be taken away from that place very safely, which is one of the major advantages of our system. Secondly, it’s a total plug-and-play system so the operator can plug in what ever is necessary, which can be decided on-site and he can pass on the command structure to the HQ (Headquarters). In normal systems, it’s up to the operator on how to dispose the bomb. But in our system, once the system is set-up, the command can be shifted over to the central HQ where the experts could be watching the video and have an idea on its triggering mechanism or how it can be deactivated. With plug-and-play, a bomb-disposal device can be effectively created.
Q. Could you brief us about diffusing?
A. Along with Disposal, there are other 2 Ds, which are Detection where equipments are carried along to detect bombs or bomb-like structure, and Diffusing where the robotic arm is enabled for 6 degrees of motion very finely tuned to the device with the fell the operator can try to manipulate the arm very precisely and try to diffuse it. If it cannot be diffused then IED must be disposed in a very safe way either at the same location or some other.
Q. How is the field of haptics evolving?
A. Today is a phase where haptics is necessary. For example, when an arm in a robotic device is attached with a tool like a drill, and a suitcase with an explosive device is being drilled, then the amount of force required to drill through it is very important for a very safe disposal. Otherwise, the damage caused can be very huge. The force applied by the robot has to be felt by the operator otherwise there can be possibility of tremendous damage. If there is a haptic feedback, the operator knows exactly how the arm and the tool are operating and also the forces that are involved.
Secondly when a trigger is being removed from an explosive device, it’s important to know the pressure being applied by the gripper. Too much force might cause an explosion and too less will make it impossible to extricate the trigger. There should be a very precise control where in the operator should feel that he is at the site performing all the operations. We are also using this technology in surgery simulation also.
Q. Could you talk about some new applications in the field of haptics?
A. Haptics can be used anywhere depending on your imagination. When there is an operator involved in commanding a robotic system where application of forces is critical, a haptic device becomes a must. In a normal system, joysticks are used and the only thing known is the extent of the motion not the amount of force. We are using haptics for mobile robotic system for bomb disposal and surgical simulation, where the doctor can ‘practice’ his operation that he is supposed to do on a live patient or try to simulate different ways in which he can perform the same operation from different locations. We have custom developed most of our Haptic device actuators and they are active devices and passive devices. They can be custom tuned for the application including force applied, stroke length, reaction time, weight boundaries etc.
Q. What hardware and software tools do you utilise?
A. We have got two kinds of hardware. One is mechanical, a full fledged machine tool system and we get the other operations done when we cannot afford the tools. The other is electronic and digital hardware. Depending on the type of work that we are doing, we try to get devices like controllers or motor drivers in-house. We also use a lot of sensors. Integration of all these forms the electronic hardware.
As far as software is concerned, we have tools for mechanical design like AutoCAD 12 Ultimate, where we can simulate the hardware motion. Software for control depends on the controller board that we are using (like Arduino) which again depends on the speed at which we require control and the number of I/O ports that we will be using for that device. Also what is the type of communication required from the field to the operator.
Q. Could you talk about an interesting technical challenge that your design team faced recently?
A. When we were designing the haptic device for surgical simulation, one of the major challenges was balancing the weight of all the mechanical components and nullifying the imbalances of the weight. When an actuator is used, it adds weight to the device. So we had to design the structure in such a way that they all cancel out. The second part of it was that we wanted to give it a natural motion path to the operation of the device. If endoscopic operation is considered, we have to actually follow a path that a doctor in actual situation will take. So the whole device has to be made as if the doctor feels that he is actually operating. We had to juggle the mechanical designs and the software feedback in such a way that we had to actively overcome the weight with the software. It was challenging but one fine day the idea clicked that the whole thing can be done. We came up with a device which had 5 degrees of motion out of which only 1 degree of motion had to be actively stabilised whereas the remaining 4 degree were naturally stabilised as far as the weight and friction were concerned.
Q. Do you have any evolutionary offerings in the pipeline?
A. The core technology as such can be used in many different ways. We are trying to collaborate with other people or companies who have got other core specialities wherein we can use our capability along with their capabilities and to come up with other technologies which are really useful. In haptics, one thing in which we are very excited about is simulation for an exoskeleton type of work for soldiers where they can pick up and move very heavy loads. Compared to other systems where power module is needed, we are going to use the muscle power of the soldier itself over a longer period of time to power up his exoskeleton. Mechatronics, haptic devices, software, optimization of the design, and sensor have been used which makes it very interesting. We are also working with eight other manufacturers helping them in their product design using our core technologies. The technology that we learned in bomb disposal is being used in the simulator for a soldier moving on a very rough terrain simulation to give a product that is entirely different.
Q. According to you, what kind of challenges does an R&D Environment pose?
A. The major challenge we face is integration. Integrating the mechanical, electrical, electronic, and software design to give a perfectly working product in a very optimised way and to do the work that is actually needed. As we are working on all these fields simultaneously, slowly over the time, we have developed our expertise and workshops so that we can actually do something which only electronics or software cannot do. Everybody in my team has to work seamlessly, know what the other person is doing, and how a mechanical design can be improved by software design. We are working on multi-disciplinary engineering branches.
Q. Any project that you had to come across which was extremely challenging?
A. One of the trickiest problem was a customer of mine wanted to use a device to check whether mangoes were ripe, contaminated with any diseases, amount of medication required (if contaminated), and if ripe how to pluck it and safely store it. We used a machine-vision with around 60 million colours to sense the colour of a mango peel in-turn to find out the ripeness and contaminated mango along with worm detection. We were able to detect it by taking the photographs and analysing it. Once that was analysed, we were supposed to press it so slightly to judge the level of ripeness inside. If it is ripe, then how to rotate it so slowly so that it breaks right at the tip from where it is hanging on the tree and place it in the basket. So much money was being put into this project because the customer was into tissue culture and he was plucking the mango at a particular time decided by his scientist wherein each mango could be made into 200 mango trees. If not done at the right time and with the right procedure, then the whole mango becomes a waste. So each mango for this customer was worth around 10,000 rupees. It was nearly 3 months of work. 2 months to decide and develop the whole system and prototyping took about a month. I can claim that I have made haptic devices to pluck mango which was one of the most peculiar prototyping assignment that I undertook.
Q. What kind of challenges did you face here?
A. One of the challenges which we faced was that the arm, which was to be lifted from the ground, had to be nearly 5 meters and hence precision of the motion at the tip had to be about 0.1 mm. Mechanically also it was a very challenging assignment as we even had to use carbon graphite masts to reduce the weight. It was really interesting because the whole system weight had to be passed over a rough farm. We used mobile technologies, haptics, machine-vision, etc to remotely control the device 200 meters away over a wireless network.
Q. In which application vertical do you see great demand?
A. In the coming years, according to me, there is going to be a very big scope of haptic devices. We can compare it to how a mouse changed the operation of a computer. In the coming years, Haptics is going to change fundamentally the way we use our computer systems. Presently in India, I see that most of the work that we try to get out of the computer is output through the printer or the display. But once this technology comes down, it will become much more easier for us to control machines where you can do things which are not possible right now. Haptics is going to be a major vertical in future considering the demand.
Q. Could you throw some light on your marketing strategies?
A. We work at two levels. The first one is that we directly work with the customer itself where we develop the system according to the customer’s specifications. We have felt that sometimes the customer doesn’t know which is a better solution. So we take up the challenge and develop a prototype and showcase it to the customer. Secondly, we showcase our products and try to find manufacturers who are held back because of lack of this technology. Interacting and working along with them allows us to share their problems in a much better way. We are working with eight other manufacturers and giving them the necessary design input and training.
Q. Basically what kind of audience do you target?
A. As far as haptics is concerned, everybody is a potential user. It has not been elaborated to people as to what this technology can do. We try to educate as many people as possible in every field. It can be used medicine, construction and many other fields. In this field it’s very difficult to judge where your next potential customer is going to come from. Some from woodworking could also be the next potential customer.
Q. What about your hiring policies?
A. We are more concerned on how an engineer can use his brains and hands effectively rather than his percentile. We have our own process to recruit in which we find out if the concerned person has a mechanical aptitude or a software aptitude and how they can work together. One major aspect is whether the person can adapt to the technology which is not his forte. We have been interacting with college students regarding their M. Tech projects by which we get an idea of the quality of the student and we select the best.