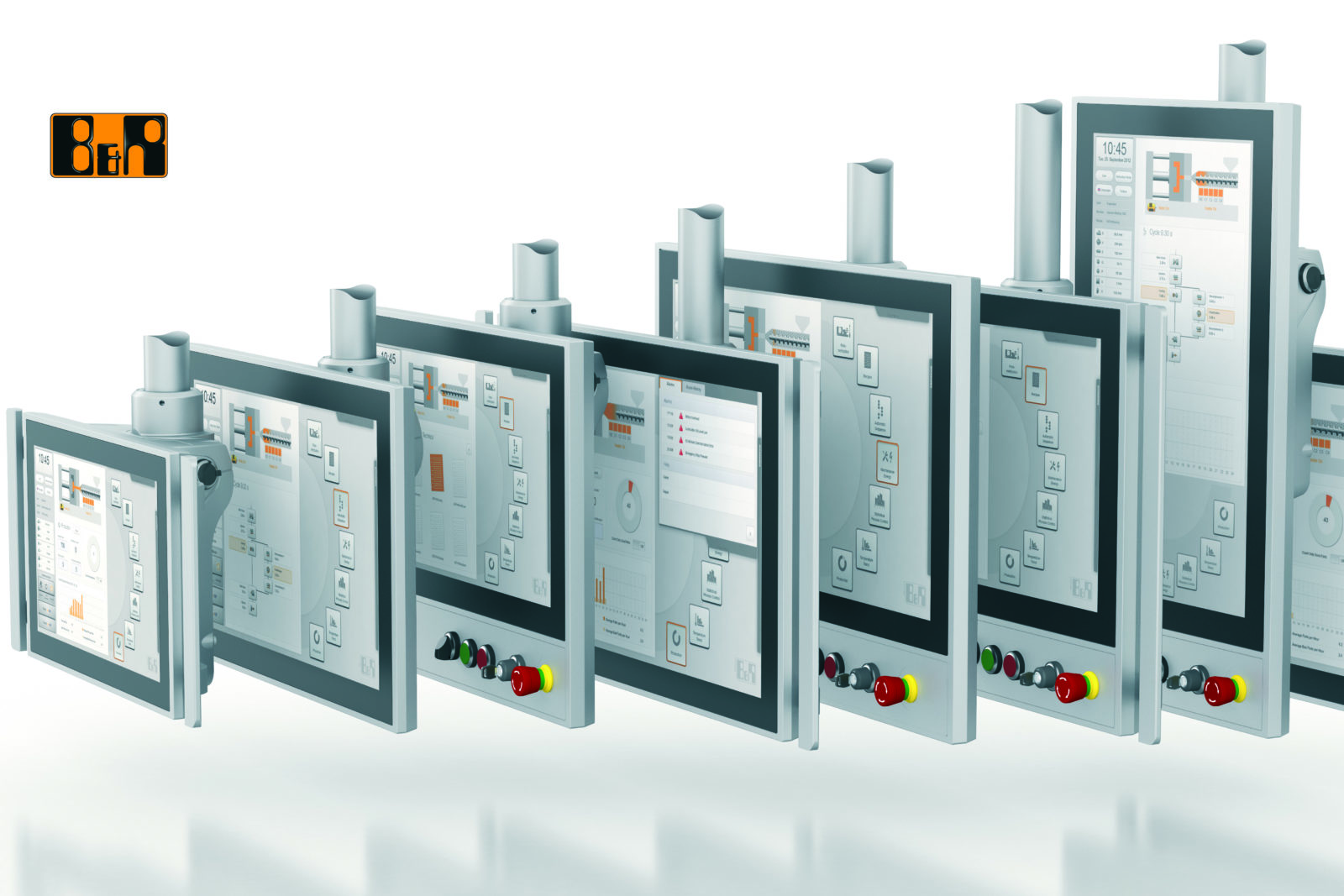
Automation is no longer restricted to the conventional ways of building machines using customized controllers or Programmable logic controllers (PLC). With the rise of Industrial Internet of Things and Industry 4.0, machine builders look at providing additional features to their customers with respect to connectivity and performance. Apart from performance and features they also look at reducing overall system costs. It is a challenge for machine builders to provide connectivity to the MES and ERP layers and at the same time provide a real time, deterministic connectivity to the field devices.
Conventional vs Innovative
In a conventional approach machine builders used a customized controller or a PLC for achieving performances on the field and solving the application needs of the machine and process. A PC based solution is used to acquire data from these controllers so as to send it to the process layers or the MES and ERP layers. These PCs most of the times also host other automation related acquisition software’s. Customers are thus continuously raising their demands for achieving higher productivity, accuracy, precision, productivity, throughput coupled with a cost effective solution. Thus the biggest dilemma for any machine builder is to achieve features and flexibility requested by the customer keeping the machine costs very low.
To overcome this many machine builders choose to use PC based automation with different proprietary software to achieve the performance needed on the field layer. As the software’s for data acquisition are based on Windows the machine builders have to run a dual operating system and install these software’s. Thus the machine builders address this issue by using PC based systems and reducing the number of components in their system but they do not achieve the flexibility and cost requirements.
Flexibility and cost the core
We all use mobile phones and we as users pick and choose the make of the handset, the operating system it works on, and eventually the software’s i.e. apps which we would like to install on it. Just imagine in the automation world if the machine builders had such flexibility, wouldn’t it provide him an extra degree of flexibility? It could help him to choose the real time operating system, the network, the software to use? This eventually will help him reduce his system costs and give him the technological edge over his competitors. This is not a concept but a practical approach being used by machine builders with a PC based automation and having in-house R&D for developing software’s for their machines. Android in the mobile market has gained momentum with its open source approach. Similarly in industrial automation open source systems are catching the eye of the OEMs as well as machine builders. The usage of open source systems in automation is creating a whole new dimension of flexibilities, features, and possibilities.
Myths and misconceptions of open source
There are many myths and misconceptions about open source. Vendors provide software’s and charge machine builders for licenses or provide object codes for their software or ask the machine builder to purchase custom made hardware like ASICs and justify they are still open source. What open source truly means is there are no charges; no copyrights and users have access to the complete source code. This is when the platform is truly recognized as open source.
Open source software and applications are definitely free of cost but are also governed by different licenses. Some licenses allow the modification of the code but ask the user to provide the modified or derived work back to the community for usage by others, while some licenses allow the user to modify or have derived works and the users do not need to provide their work back, in fact they can even copyright their modified work under their name and distribute it. The most common licenses are the GPL, BSD and MIT licenses. GPL is the most widely used free type of license and has a strong copyleft requirement. In any scenario of distributing the derived works, the source code of the work has to be made available under the same license. Linux is a major example of the GPL license. The MIT license is again a free permissive license which allows the users to do anything with the code with proper attribution. OPC UA is an example of a MIT license. BSD alike the MIT license also is a free permissive license which allows users to do anything with the code with proper attribution. Ethernet POWERLINK and openSAFETY are examples of a BSD license. Thus users can make use of these established global open source automation technologies in their systems in-order to meet their customer demands.
Benefits of using open source Linux
The main advantage of using open source is reduction in costs and making use of tried and tested systems. The machine builder can install Linux as an operating system and to have the real time capabilities can use the RT PREEMPT patch for Linux. This will ensure the deterministic operation needed on the field level. Thus the machine builder can scale down the PC and still achieve a higher machine performance. Like other operating systems Linux offers the users to have different application running and thanks to the RT PREEMPT patch it provides a real time deterministic behavior for the field level communication. B&R Automation system is an example using Linux as an operating system in machines as well as processes. APROL which is the DCS solution from B&R operates completely on open source Linux.
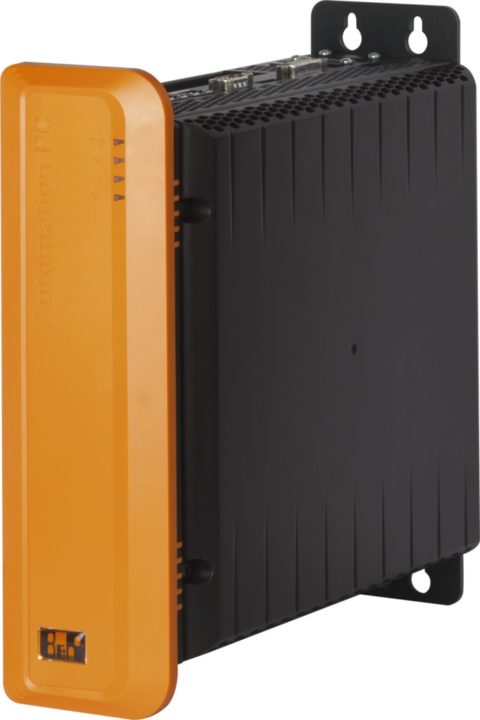
Ethernet POWERLINK: Network the key differentiator
Once Linux is in place on the PCs the machine builder needs to gather data from the field devices like encoders, IOs, pneumatic valves, drives etc. This is done using a network. Ask any machine builder the network demands are very stringent in automation and needs a perfectly deterministic performance. In motion application this determinism and real time communication needs go down to as low as 200µs and in process it could be even a few milliseconds. Topology also plays an important role in the machine and process. In many instances high availability is of keen importance.
Looking at all the above aspects Ethernet POWERLINK has the perfect blend of all the features coupled with the having the source code open source. It is the only protocol which provides the master and slave source codes free of cost. The protocol also provides high availability and redundancy features in the open source stack. On both the master and slave devices it functions on standard Ethernet and complies with the IEEE802.3 standards. The protocol is completely hardware and operating system independent. The stack is maintained on the website by the Ethernet POWERLINK standardization Group which is a consortium of over 3200 members and users.
The machine builder can thus implement the master solution on the Linux PC and achieve the deterministic performance on the field. The machine builder has the option of using the field devices compliant with POWERLINK communication with off-the-shelf components from various companies. A huge list of device manufacturers is available at http://www.etherent-powerlink.org. With this configuration the machine builder can easily achieve cycle times as low as 200µs. A redundant master solution can also be implemented by having two masters in the network to avail high availability. The complete details of the protocol for any platform and operating system implementation are readily available here.
A video of the a position control demo using FPGA and ARM controllers controlled by an open source Linux based PC is available here
openSAFETY: Safety no longer a limitation
Safety is of utmost importance in machine as well as process industries. To make the machine safety compliant needs effort and certifications. We try to make the life of machine builders easy by providing a TUV certified stack complying with the IEC 61508 standards. The machine builder thus gets a networked safety solution. Networked safety has not only improved the cooperation between humans and robots but also reduced development time, reduced wiring, eliminated setup errors, improved maintenance, and added intelligent features. This has facilitated robots to no longer be restricted by cages. Similar to communication networks, most safe networks are proprietary and limited to certain fieldbuses and they are not compatible with each other. Thus connecting all machines on a shop floor would have been a distant dream. But thanks to openSAFETY which is fully open and totally fieldbus independent safety protocol makes lives of millions of plant operators and machine builders very easy. It is SIL 3 certified standard and available for all industries.
OPC UA: Field to MES/ERP connectivity
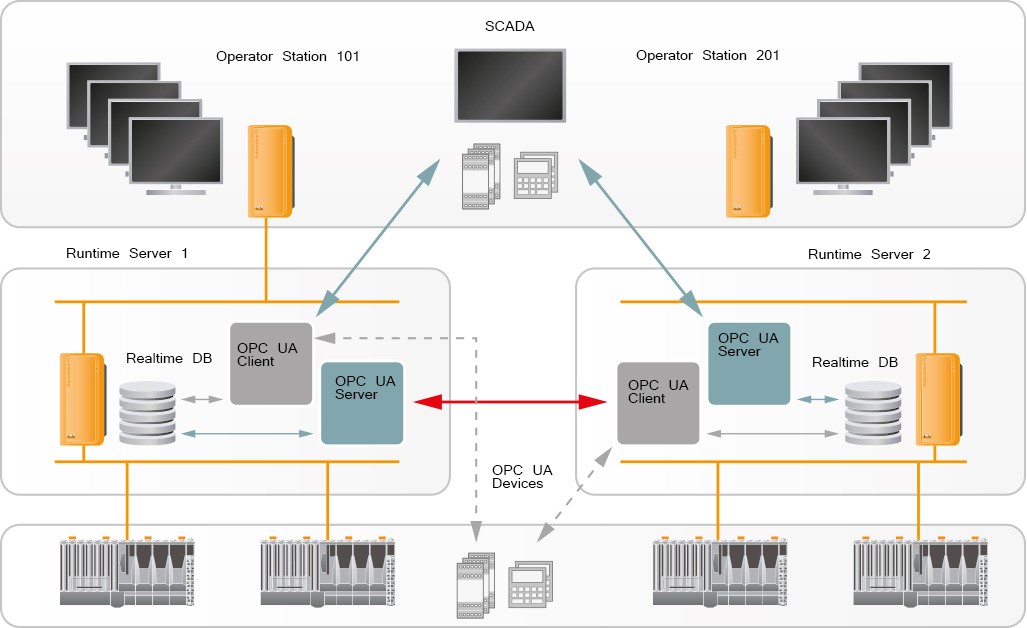
POWERLINK and openSAFETY enable to machine builder to gather data from the field in a deterministic and same method. On a shop floor there could be requirements for the controllers from different machines to exchange data or a central PC working as SCADA would require the data for sending it to the ERP and MES. The machine builders could use OPC UA which is another open source protocol based on standard Ethernet for transferring the data. Being based on standard Ethernet, POWERLINK effectively mergers well with OPC UA and facilitates seamless data transfer from the shop floor to the MES/SAP. OPC UA is already playing a central role in the IT related areas of modern production systems. An OPC UA server and OPC UA client are now available directly on Linux-based runtime servers to allow open, vendor-independent communication. Motor management and control units, compact OPC controllers and other devices can directly exchange all important operating, service and diagnostic data with the OPC UA client. OPC UA is standardized in accordance with IEC 62541 and offers easy-to-use functions for vendor-independent data exchange. This makes it easy for software developers to engineer complex systems with high data communication demands. Implementing flexible and modular automation solutions more easily is the result.
No vendor lock-ins
With the usage of open platforms the machine builder can be free from licensing and copyrights. He gains an edge over his competition as he offers the customer a flexible, high performance and on top of all a cost effective solution. Usage of the open platforms helps him to avoid vendor lock-ins. The machine builder is able to provide a complete solution from field to the board over a standard networks.