Soldering irons are most often used for installation, repairs and limited production work in electronics assembly. These can be commonly seen in any electronics environment. But with the confluence of automation and the emergence of surface-mount technology (SMT), more sophisticated methods of assembly and repair have came to the fore, and demand refinement in both soldering and de-soldering techniques. Thus, first-age soldering workstation have taken the place of ordinary soldering irons in repair shops.
A soldering workstation is a simple temperature-controlled instrument that consists of electrical power supply, control circuitry, soldering iron or soldering head with a tip-temperature sensor and/or provision for adjustment of temperature, and display. The station usually has a stand for the hot iron when not in use, and a wet sponge for cleaning. It is invariably used for soldering components.
Other functions may be combined; for example, a de-soldering pump, mainly for the removal of through-hole components. In addition, there may be a hot-air gun, vacuum pickup tool and soldering head. But when you repair a modern-age motherboard, for example, to replace a damaged electrolytic capacitor, after struggling with your 30W soldering workstation that came with a spring-loaded vacuum tool, you simply feel hapless and realise what a difference the right power and tool make!
Usually purchasing such a soldering workstation for your workshop ends up in a folly as the array of features and manufacturers’ specifications are usually quite confusing, and most units are priced out of your budget. A soldering or de-soldering station is an investment, and the decision to purchase one (or a few) should be made thoughtfully. With the variety of soldering stations out there, make sure you are getting the right one for your money.
You must carefully select the soldering and de-soldering station as per your requirement as different types of components require different parameters for soldering/de-soldering. If you do not look out for these, you might end up damaging the equipment. This buyer’s guide is all about this.
Hot-air rework
Hot-air rework stations are ideal for small jobs that you need to finish in a single go. A hot-air gun, which melts the solder and enables you to remove the components, is great for removing parts from an old circuit board. But the process is not fully surgical, though it will save you a great deal of time as well as existing parts that otherwise would have been damaged along with the circuit board.
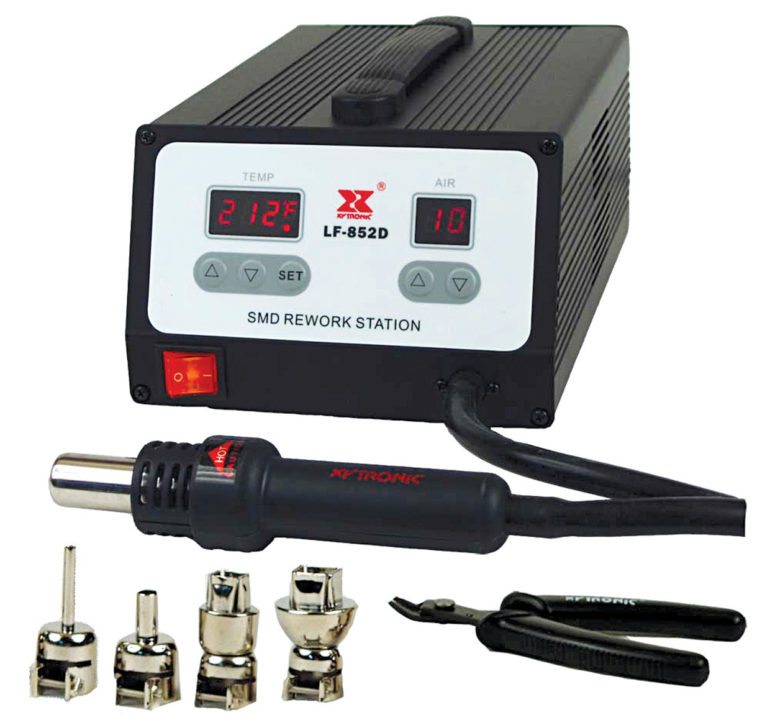
Another benefit of using a rework station is that it doubles up as a soldering workstation, which isto say that you de-solder, say, a transistor and then solder on a new transistor immediately, saving you time in the process.
You can de-solder and re-solder several components simultaneously—quickly de-solder a problematic electrical part from the circuit board and re-solder the area again in a few minutes. In addition, hot-air stations are typically non-contact, enabling you to prevent damage to other parts of the circuit as you work.
However, one drawback of using hot-air rework stations is that these are much more expensive than de-soldering stations. Rework stations are also considerably bulky and difficult to carry around, so you will need to bring your work to the station itself, which can be difficult at times.
De-soldering stations
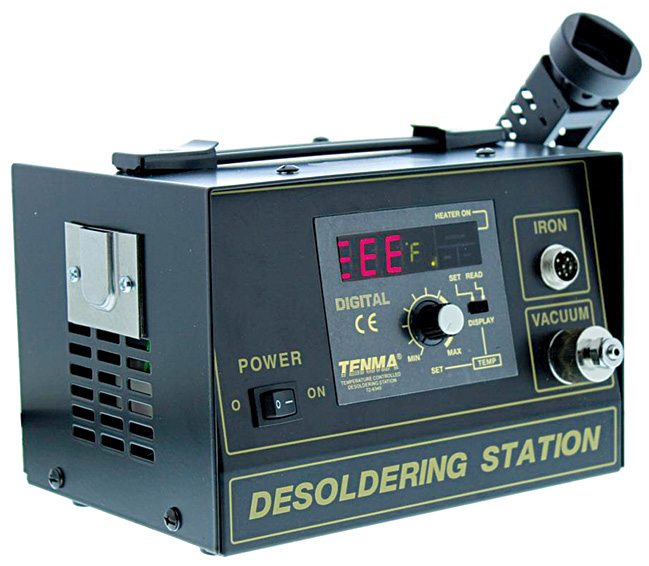
De-soldering stations are available with a variety of features; some include vacuum pumps that enable you to precisely de-solder whatever you want. Because SMT parts are usually small, de-soldering stations are also much easier to clean and maintain than hot-air rework stations.
De-soldering stations come packed with a lot of power, yet have fewer controls and nozzles than hot-air rework stations. But the usual drawback is that there is a greater risk of damage from voltage leakage when using de-soldering stations.
The most significant benefit in choosing a de-soldering station is probably its lower price tag; you can save upwards of a few hundred rupees by opting for a de-soldering station over a hot-air rework station.
Further, de-soldering stations are easier to move than rework stations. Although, you can get your job done with just a soldering iron and de-soldering station, a hot-air rework station may certainly be better for you if you are going to use most of its special features.
Bench-top de-soldering or rework stations
Generally, bench-top soldering workstation have the most accurate temperature control, best thermal recovery and other features like programmable timing and hot air combined with suction. If you plan to work with surface-mount ICs on a regular basis, rework units are ideal. These have a set of separate nozzles for just about every IC package. The higher-end units can be programmed to pre-heat for a specific period before applying heat and then heated for a number of seconds, and some even have a vacuum nozzle to pick up freed components from the PCB using suction. But since these are costly, hobbyists are usually able to do without these.
Moreover, a component with one or two connections to the PCB can usually be removed easily by heating its joints with a soldering iron. Solder-filled hole can be cleaned out with a de-soldering pump or with a pointed object made of a material that the solder does not make wet, such as stainless steel, graphite or wood. If a multi-pin component does not have to be salvaged, it is usually possible to cut its pins and remove the residual ends by pulling these one by one.
Components with more pins cannot be extracted intact in the way described above, unless the wire leads are long and flexible enough to be pulled out. For a component such as a dual-in line package (DIP), the pins are too short to pull, and solder melted on one joint will solidify before it can be melted on another pin.
Basics tips to observe while buying soldering workstation
Different products are being produced by all reputed manufacturers to meet user requirements at different levels of work situations. The products range from economic, entry-level stations with basic features, such as analogue thermostat based temperature control, to high-end expensive and most sophisticated units having precision digital temperature control and most sought-after component removal attachments. Since the station you are going to purchase would become an integral part of your toolkit, it is important to consider some points before making a purchase. The following tips can be useful:
Reliable brands. It is important to choose a well-reputed high-quality manufacturer’s product. It is probably one of the most important decisions to make when you decide to make a purchase. A few of the premier imported brands in the solder industry include JBC Tools, Weller and Kester, Hakoo and Sumitron. Picking quality brands where it matters gives you the general incentives of superior customer support, trusted materials, manufacturing, longevity of solder tools and versatility to interchange solder irons and other supplies within your station seamlessly.
Control units. If you are working on a job with a high temperature requirement for soldering, you will need a comprehensive temperature control unit to help keep the temperature well under control. With a choice of proper control unit, you can accurately monitor the heat of the soldering iron to ensure that you keep the temperature at the required level, so that you can get the best results.
Always choose a model that has a comprehensive real-time temperature control. There are models out there from the rudimentary economical ones that rely on thermostat based analogue temperature control to the most sophisticated industrial models that have precision temperature controls and flaunt great looks.
Hand piece. Depending on what you already own and what your soldering needs are, you may require a hand piece. Certain soldering systems come with enough flexibility to allow you to interchange and use a variety of hand pieces to help achieve close soldering blends. A pencil hand piece is usually excellent for SMT and PTH work.
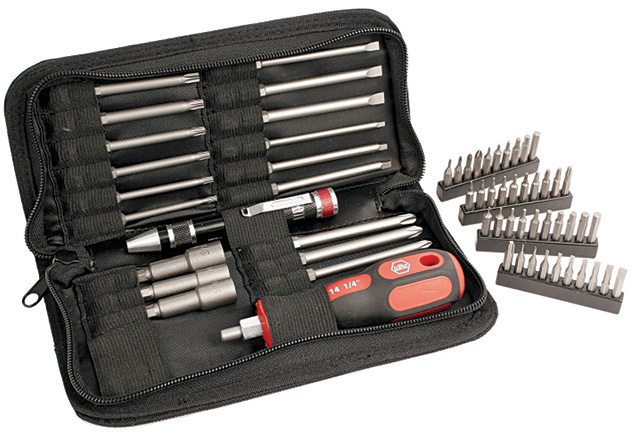
De-soldering iron. For de-soldering, you would need a de-soldering iron, but not all systems come equipped with a de-soldering iron. If you need one, look for a solder workstation that includes a well-designed de-soldering iron and a versatile hand-piece stand.
Soldering and de-soldering bits. To match really small or heavy-duty applications, and to meet your soldering and de-soldering requirements and needs, a variety of soldering and de-soldering bits are needed. So always go for a rework station that includes a versatile set of bits to match your work needs, and make sure the quality and re-availability of these bits are taken care of.
Special attachments. For the sake of convenience during work, and versatility, choose a model that comes with special attachments, say, attachments for the removal of QFP packages, a vacuum picker and so on.
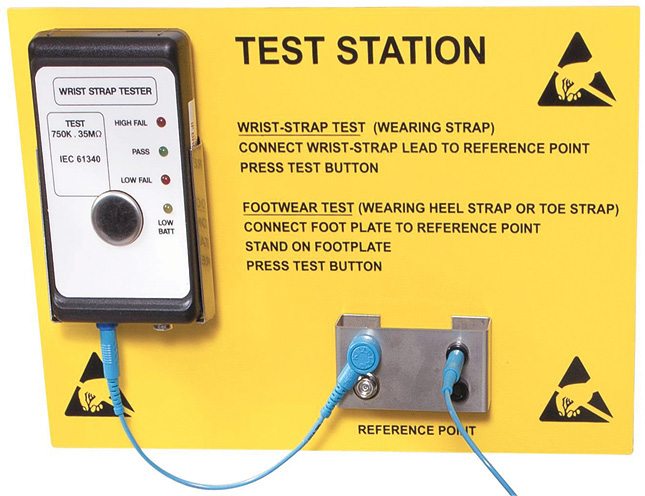
Vacuum pump. Always go for a vacuum pump having good suction level. Read manufacturer’s specifications carefully at the time of purchase. A dual-reflow-type vacuum pump with a release valve is a good choice. A comprehensive vacuum-level indicator can further make your life easy during SMT and PTH work.
Thermal tweezers. Recent advanced rework stations are available with special tools like thermal tweezers and thermal peelers. Consequently, review your needs before buying your rework unit.
Safety features. As with any soldering equipment purchase, ensure that the equipment includes a variety of safety features. It should be ESD-safe, have an accurate temperature control and a temperature lock function besides a tip-cleaning patch to ensure proper solder cleanup.
Versatility. When choosing a trusted brand for your soldering workstation, you have the added benefit of versatility. Many of the soldering equipment come with interchangeable instrument attachments, allowing for the biggest range of soldering applications.
Wattage. It holds prime importance in making your buying decision for a rework station. Unless you are going for repair of instruments involving high-profile, rugged components, a 140W or equivalent is quite reasonable and goes well for almost all regular work.
Soldering torch. An acetylene or butane based torch attachment is particularly an incentive if you are interested in high-profile assembly work that involves metal soldering of assorted types, chassis work or work involving galvanised wires.
ESD tools and devices. Modern-day work involves electrostatic-sensitive components on a large scale. To work with such devices, normal equipment is quite unsafe. Need for special ESD-safe tools and devices is mandatory. We recommend use of the following devices if you are involved in handling and use of such devices:
- ESD-safe mats
- ESD-safe tool kits
- Anti-static dispensers
- ESD-safe wrist and ankle straps
- Periodic verification tester
- Precision surface resistance monitor
- ESD field-strength meter
- Automatic ground-fault watch dog
- Temporal ground extenders
Important note
EFY team would like to suggest some mandatory safety devices as well.
A proper electrical ground is the foremost requirement in any assembly or repair workshop, but unfortunately, it is often neglected. Soldering fumes are very toxic in nature, so you must install a fume exhauster in your workshop.
In workshops doing high-profile work involving torch soldering, special fire retardant gowns and goggles should be put to use to avoid any untoward incident.
Proper layout of power cables can be very helpful to avoid accidents to a large extant. Fire or arc light monitors and alarms should be employed in all assembly lines involving torch soldering.
A first aid burn kit comes in handy for minor injuries during soldering jobs. So keep one in your tool kit.
Regular service of Soldering workstation is required and try to avaoid local shops for any repairs.
Do you like this article? You may also like these similar articles.
Nidhi Kathuria is a senior application engineer at EFY Labs, New Delhi