The market for solar systems is growing exponentially due to the rising demand for solar energy worldwide. Unlike other forms of energy sources, solar equipment does not require expensive and consistent maintenance. But for optimised outcomes, it is necessary to ensure that the equipment is working properly at all times. This article discusses the related parameters and several ways of testing the solar equipment.
With the rising demand for solar energy, the market for solar systems is growing exponentially. More and more manufacturers and businesses are considering it as a profitable sector in the long run. New solar systems with better efficiency, performance, and longevity are being launched in the market nowadays. Unlike other forms of energy sources, solar equipment does not require expensive and consistent maintenance. According to a report from Market Research Future, the solar panels market is expected to grow at a CAGR of 20.18 per cent until 2023.
But for optimised outcomes, it is necessary for industries, homeowners, and commercial businesses to ensure that their equipment is working properly at all times. This makes photovoltaic (PV) testing services mandatory to ensure safety and performance, especially for new products.
It is also important to make sure that common standards for solar panel certification or photovoltaic testing like those established by the International Organization for Standardization (ISO), International Electrotechnical Commission (IEC), American Society of Heating, Refrigerating and Air-Conditioning Engineers (ASHRAE), and the like are met. This article discusses the related parameters and different ways of testing solar equipment.
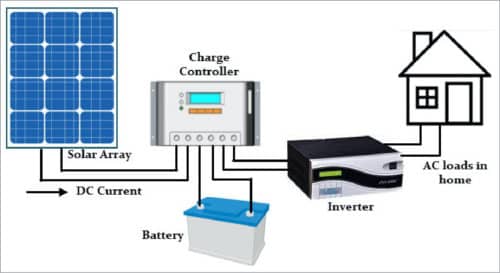
About photovoltaic system
Any photovoltaic system that converts solar energy to power has a few basic components—photovoltaic modules, battery or batteries, charge regulator or controller, and an inverter. A charge controller is necessary for a standalone system for regulating the voltage and current coming from the solar panels and going to the battery so as to prevent the battery from overcharging. An inverter converts direct current (DC) generated in the process to alternating current (AC).
A solar cell or photovoltaic cell is the basic unit of any solar energy generation system. It is a silicon-based layered semiconductor that can produce electricity from sunlight. Just like all other types of battery cells, every solar cell has one positive back contact and one negative front contact.
When sunlight falls on a solar cell, some photons of the light that get absorbed have enough energy to exceed the energy gap between the valence band and conduction band as well as excite the electrons to break semiconductor bonds. Due to electrostatic force of the field across the junction, electrons migrate to the n-type side while holes move to the p-type side. This results in a potential difference across the terminals of the cell. A photovoltaic module or solar panel consists of multiple such cells connected in series to provide the required voltage output for a load.
Metrics affecting output of a solar panel
For any solar project to be successful, certain factors like the rating of a solar panel need to be chosen wisely. In case more voltage is required, more panels can be connected in the power generation system. The total system voltage of an array of panels is a product of the total number of panels and their individual voltage rating.
The parameters are a way to measure the efficiency of conversion of sunlight to electricity in a panel. For instance, if a tolerance value (in per cent) is mentioned in the power rating, it is used to specify the upper and lower bounds of power generation for the rated capacity. A few important parameters are discussed next.
Maximum power (PMax)
It is the maximum power (in watts) that can be obtained from a solar panel under standard conditions. The higher the value of maximum power, the greater is the load that it can handle. It can be calculated by multiplying current (IMax) with voltage value (VMax) at the maximum power point on the current-voltage (I-V) graph.
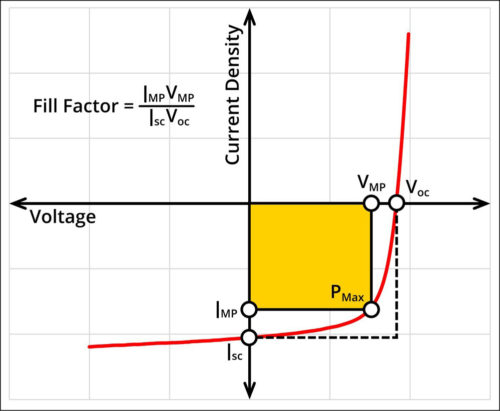
Voltage at maximum power (VMP)
The voltage of a solar panel (in volts) at peak efficiency when it is connected to the solar equipment (charge controller or inverter) under ambient conditions is known as the voltage at maximum power.
Current at maximum power (IMP)
The current generated by a solar panel (in amps) at peak efficiency when connected to the rest of the solar setup under ambient conditions is termed as the current at maximum power.
Open-circuit voltage (VOC)
As the name suggests, VOC is the voltage obtained across the terminals when no load is connected to the circuit or system. The current through the open circuit is always zero. VOC can be simply measured using a voltmeter and is crucial in deciding the number of panels that can be connected in series.
Short-circuit current (ISC)
ISC is the amount of current through solar panels when there is a short circuit between the positive and negative leads, that is, the voltage across the cells is zero. This is useful for determining the amount of current an inverter or connector can withstand, thereby ensuring safety.
Efficiency (η)
The percentage of absorbed solar energy that a solar panel can actually convert into electricity when in a complete setup under standard test conditions gives the efficiency of the panel. This is an essential measure in quantifying the performance of a panel; the higher the efficiency, the more is the amount of power generated. Factors like tilting the solar panels for better orientation to have full sunlight exposure and use of bipolar modules to produce power from both sides improve efficiency.
Fill factor (FF)
Another metric to characterise the performance of a panel is the fill factor. The ratio of Pmax and the value obtained on multiplying VOC with ISC gives the value of the fill factor.
Temperature coefficient
VOC and ISC decrease with increase in temperature (inversely proportional). The temperature coefficient represents the per cent change in these terms with a change in temperature (%/°C). This also shows how these values might deviate from their rated values in different climatic conditions.
Testing and measurement
Investing in proper photovoltaic testing is a good way of measuring how effectively the solar equipment is performing in the installed location before beginning with the operations.
Although testing individual components installed in solar energy plants most commonly deals with the measurement of current-voltage characteristics of solar panels and collectors, there are several other procedures too. These include measurement of the emission coefficient of materials, testing of PV modules in a humid environment, visual inspection and thermography of solar PV panels, testing of control units and control systems, performance testing, field testing, and many more.
The tools for measurements can range from simple digital multimeters that are easily available in labs to high-precision technique-based instruments. For test equipment that can characterise PV modules or source circuits, commissioning and safety testers and portable I-V curve tracers are the most common. PVA-1500 PV Analyser Kit is a popular 1500-volt I-V curve tracer with built-in PV performance modelling and wireless irradiance, temperature, and tilt sensing.
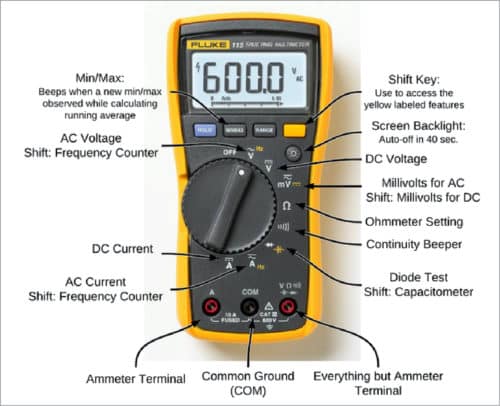
Most of the professionals also carry an irradiance meter for checking real-time system performance and an infrared (IR) camera or thermometer with them these days. IR thermometers can take basic temperature measurements to do the same task as cameras, that is, identifying high-resistance electrical connections and thermally stressed overcurrent protection devices.
Among the handheld instruments, multimeters are a popular choice. Multimeter allows a user to test the voltage and current of any device, and therefore it can be used for testing solar panels. A switched multimeter is manually switched between the ranges to get an accurate reading of the selected function like the current, voltage, or other variables. Whereas an auto-range multimeter switches between ranges automatically. But both perform the same function.
To read the approved voltage of panels, check inside the converter box located at the back. Next, set the multimeter to have a higher reading than the approved voltage. The reading of the multimeter must be as close as possible to the rating for high performance.
While performing the testing procedures, precautions must be taken so as not to cause any damage to the solar equipment. For example, the alligator clips attached between the panels and multimeter can only be disconnected after switching the multimeter off.
When connecting the controller and battery with the panel, first disconnect the panel from the controller, and then disconnect the battery from the controller. Similarly, during reconnection, first connect the controller to the battery and then the controller to the panel. Also, positive and negative connections must be duly taken care of.
Indian scenario
Solar energy companies in India are leaving no stone unturned to ensure the quality of their products in this highly competitive market. For instance, recently, Underwriters Laboratories (UL), a global safety certification organisation, announced that it has completed the PV module testing and certification for bifacial modules manufactured by Waaree Energies, a solar PV module manufacturer in India, as per the latest IEC standards.
According to a press release, Mukul Harne, AGM of Quality, Waaree Energies, said, “We partnered with UL due their long-standing understanding and experience in certification to IEC CB 2016 standards coupled with the harmonised UL 61730 standards that provide the US and international market access in one standard and the widespread acceptance of UL Mark in the US.”
Testing labs have come up in the country in the past few years. ACME Solar Test Laboratory, a subsidiary company of ACME Cleantech Solutions, and a National Accreditation Board for Testing and Calibration Laboratories (NABL) accredited lab, was established in Manesar, Haryana in 2017, which is engaged in the testing of crystalline silicon PV modules.
As the awareness about the importance of factors impacting cost systems and possibilities increases, the testing equipment and monitoring system market will grow further.