Imbibing progressive practices ranging from multicore (parallel) processors and software-defined instrumentation to wireless standards, the field of test and measurement continues to enable new technologies
JANANI GOPALAKRISHNAN VIKRAM

October 2011: The use and development of technology requires test and measurement instruments. From research and development of new technologies to ensuring quality in the manufacturing of various products, these instruments are essential. For example, when a space shuttle is launched, many different instruments are used to conduct thousands of electrical, temperature, chemical and other measurements to monitor the status of the craft and its crew. These instruments are essential to our high-tech economies,” says Dr Anita Agrawal, assistant professor in department of electrical and electronics engineering, BITS, Pilani-K.K. Birla Goa Campus, opening our discussion on developments and trends in the test and measurement (T&M) space.
The goal of T&M has often been misunderstood as mere fault-finding. Of course, the detection of faults during manufacture has been a key task handled by T&M instruments; and has been instrumental in achieving high quality-control levels in all technological arenas. However, T&M plays a larger role in monitoring and maintaining various critical technical scenarios, and in the research, validation and improvement of new technologies.
Further, the relationship between T&M and other technological areas has always been intertwined and symbiotic. While T&M helps develop new technologies, it also imbibes the best of technologies to advance its own capabilities further. Progress in networking and telecommunications, for example, has been possible only because of capable T&M equipment that can accurately measure and monitor various critical technical and quality-of-service (QoS) parameters on a real-time basis. At the same time, fast wireless and Ethernet technologies have helped make T&M instruments more communicative and capable of connecting to larger enterprise systems via fast networks. It is this symbiotic relationship that drives a lot of improvements and innovations in the field of test and measurement.
Inspiration to improve—from technology and technologists
The innovations in T&M cater to both the needs of new technologies as well as the demands of technologists and manufacturers.
At one time, strict quality regulations and the need to find even the smallest of faults were the key innovation drivers in the T&M industry. But now high standards have been set and achieved in this aspect, and so the focus is shifting to low cost, short time and ease of testing.
“The drive to reduce the cost of test is forcing changes in the way instruments communicate and the way they are programmed. As examples, look at the rise in the number of LAN eXtended for instrumentation (LXI) instruments (over 1500), graphical programming and the acceptance of modular tests such as PCI eXtensions for Instrumentation (PXI),” says Bob Stasonis, Pickering Interfaces, USA.
[stextbox id=”info”]Software development coupled with improvements in areas like LED lighting allows vision inspection systems to improve test speeds and reduce marginal errors[/stextbox]
A lot of effort is also focused on making the test engineer’s job of routing stimulus or measurement instruments to and from the unit-under-test easier. “To that end, we have focused on switching the density and bandwidth. As products become more complex, more inputs/outputs (I/Os) need to be managed. Also, between new high-speed serial buses and wireless products, the need for even higher number of switching points and getting a few more GHz where possible is the priority,” remarks Stasonis.
On the technology front, the growth of wireless technologies has been driving a lot of innovations in the T&M world. Higher signal bandwidths and increasingly complex modulation schemes, strict QoS requirements, need for real-time monitoring across networks, etc are driving the need for faster and more capable instruments.
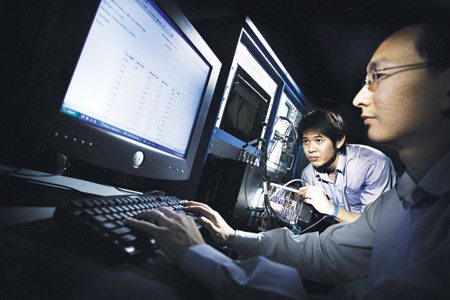
The recent multicore mania, surge in digital broadcasting, more stringent quality norms across industries, convergence of design and development activities across the product lifecycle, need to shorten the time-to-market like never before, and a lot of other new technological and market trends are also triggering various developments in the T&M world. In the rest of this article, let us delve into some of these recent developments and trends in test and measurement.
Great improvements in vision test systems
When we think of test systems, machine vision is probably the first thing that comes to our mind. Machine vision involves the capture and analysis of images to monitor and control an activity. Generally, it is used for automatic inspection and process control in assembly lines, guidance of robots, etc. The light source used is a very important factor in vision test systems because it affects how accurately the image is captured—and hence how accurately defects can be spotted.
Of late, there have been significant improvements in machine vision systems with the use of light-emitting diodes (LEDs) for the light source. LEDs offer many benefits like high efficiencies, reproduction of varied colours and longer lifetimes. Moreover, the last few years have seen significant improvements in LED technology in terms of brightness, efficiency, thermal stability and optics—all of which are now being harnessed by machine vision companies to improve their test systems.
We also see test systems with increased strobe speeds emerging to meet new machine vision applications. Cameras capable of 1000 frames per second (fps) are becoming the standard. These take hundreds or thousands of inspections on a part looking for a pass condition, as against the earlier norm of one or a few images. Software is also becoming smart enough to process and analyse these images swiftly and accurately.
Stasonis confirms, “Improved lighting and, most importantly, software algorithms have improved vision test systems. Software development coupled with improvements in areas like LED lighting allows vision inspection systems to improve test speeds and reduce marginal errors.”
Emergence of multicore systems
Multicore processors are fast becoming popular as these help achieve performance gains without increased clock rates. Of course, the world of T&M has to keep pace with developments across the technological spectrum. Hence test engineers are now beginning to use multicore processors to develop automated test applications capable of achieving the highest-possible throughput through parallel processing.