In the modern world, it is a big challenge for many industries in information technology or manufacturing to maintain quality without compromising on the costs of quality and non-quality.
These two together make the total cost towards maintaining quality of a product, and are involved throughout the project’s life cycle. The primary challenge here is to determine how to trim the overall costs of quality and non-quality.
There are many definitions of quality set by various gurus around the world, some of which are given below:
“Quality should be aimed at the needs of customers, present and future.”
—Dr Edward Deming
“Quality is the degree of excellence at an acceptable price and control of variability at an acceptable cost.”
—Robert A. Broh
“Quality is the loss (from function variation and harmful effects) a product causes to society after being shipped, other than any losses caused by its intrinsic functions.”
—Dr Genichi Taguchi
Consumer electronic products have huge competition in today’s market. Due to this, there is a thin cost margin with good character that draws consumers to buy the merchandise, along with quick and quality after-sales service.
There are many factors that may affect the costs of quality and non-quality. A few of these are mentioned below.
Cost of quality is the cost of conformance incurred from costs of prevention and appraisal. These include:
• Cost of contract
• Cost of employee training and education
• Cost of auditing
• Cost of maintenance
• Cost of resolving an impediment
• Cost of maintaining company assets like test equipment
• Cost due to field trials
• Cost of employee wages
• Cost of prototype and reviews
• Cost of continuous improvement
• Cost to make infrastructure for logistics and packing (focus on packing technologies)
Cost of non-quality is the cost of non-conformance incurred due to internal and external failures. These include:
• Cost of rework
• Cost of frequent design change
• Cost of requirement change
• Cost of material waste
• Cost of delay in release due to internal failure or regressions
• Cost due to non-conformance in the manufacturing process
• Cost due to non-conformance in raw materials like electronic and electrical components
• Cost due to non-conformance in assembly of components
• Cost due to warranty claims
• Cost incurred from customer complaints
• Cost due to return of product
• Cost due to service
• Cost due to lack of service (losing customers)
• Cost due to legal and government rules, when certain regulations are not followed in product designing and implementation
The development, quality assurance and quality control team is mostly responsible for reducing the costs of quality and non-quality. Research says that most recurrences from the field that get consumers unhappy are technical issues, including ones due to behaviour of a product with other connected devices, reliability, stability, performance and so on. This requires skilled employees (both proof and evolution) who can identify issues related to design, protocol or codification.
Owing to the immense pressure to establish the product early in the market, organisations focus more on getting the work done, bypassing many quality-related processes (which increase the software deliverable process time), which may also impact the fast pace of field returns. By this point, it is too late to contain the cost of non-quality.
The challenge is to manage this state of affairs, so that industries can optimise the overall monetary value without compromising the quality of products. Below are a few factors that may allow organisations to achieve such goals.
Of the many reasons for the cost of non-quality, a few important ones are explained below.
Cost of rework. Repeated tasks to achieve a certain goal is called rework. This may happen if engineers have not performed error-free work at the first try. Rework is the most common problem that many organisations face in their day-to-day project lifecycle.
Consequently, situations of schedule constraints create extreme pressure for the development team, which may result in the lack of involvement in the testing phase.
Below are some probable points due to which rework may occur:
• Faults not solved correctly, non-conforming with regards to coding standards or logic
• Very frequent change in requirements, design, etc, during development and testing stages
• Incomplete coverage in code implementation or hardware implementation during design implementation phase
• Test executions or design implementations not measured or evaluated; hence, incomplete coverage
• Incorrect test plan and test strategy creation
• Frequent regressions
• Negligence by developers or test engineers
Cost of frequent design/requirement change. Design changes in software are very common during the software development lifecycle. Generally, design changes come in when projects are in the middle of software development lifecycle, which contribute to a lot of rework. Below are a few points that indicate the impact of design changes:• Design changes in one component often impact other components, which often encourages software changes in other components as well and, finally, rework in one or more software elements
• Increasing overall development cost
• High chance of delay in the market
• High rate of regressions
• May need to develop additional components and, hence, boost efforts with respect to planned efforts
To avoid these issues, it may be useful for organisations to ask a few questions during conception phase and create a secure database that may provide optimal information to recover the shock of design changes.
Some such questions that should be answered and documented during design phases are:
• What is the anticipated number of plan modifications that may happen during the development stage?
• How many elements should be involved during plan modification?
• How much rework effort is required for plan modification?
• Which component requires optimal rework effort?
• Which ingredients should be prepared early to minimise shock due to design modifications?
Database structure that may be useful to analyse and foresee design change efforts is given below:
• Unique design change number
• Description of design change
• Name of module or component where design change needs to be made
• Type of change
• Time spent to carry out the change
• Name(s) of person(s) who made the change
• Date on which design change is made
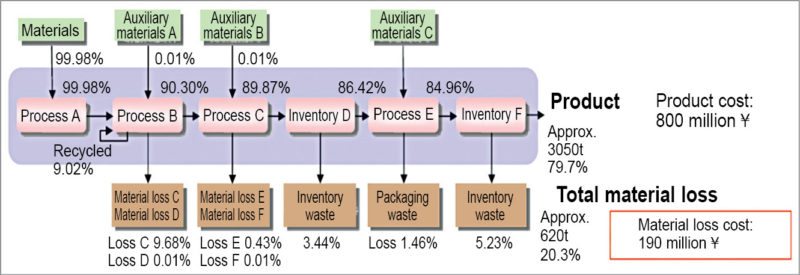
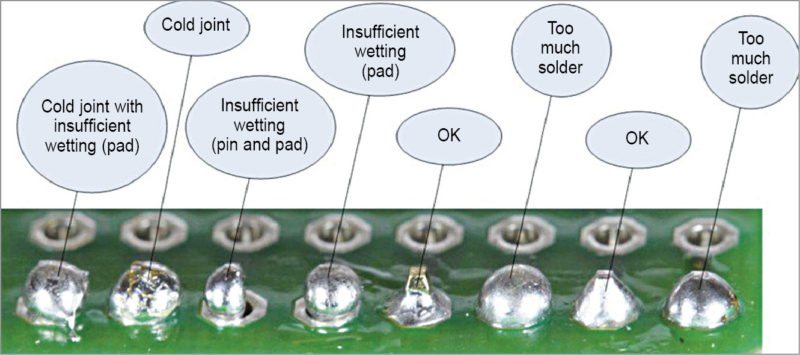
Cost of material waste. Any material/tool that is unavailable due to defect, mishandling or being scrapped is material waste. In every organisation, during execution of its process there is always some loss incurred. Material loss margin varies from company to company, depending on how they are checking it. A few material losses can be manipulated effectively, whereas others cannot.
Especially in the research and development sector, loss due to bad workmanship such as test equipment error, development/test setup issue, choosing right vendors for quality service and materials, and the like can be curbed by training, whereas material losses during the making of prototypes are inevitable.
By preventing material waste, costs can be spared in any kind of establishment. A few examples where industries took in huge costs towards material waste are given in Tables I and II, and Fig. 1.
Waste material can be imaged in consumer electronics based industries in the following ways:
• When defective tools, equipment or raw materials (like spare parts and consumables) are purchased
• Test equipment errors due to lack in regular calibrations
• Mishandling of equipment/poor workmanship
• Bad-quality materials
• Wrong settings or calibrations
• Poor inspection
• Lack of environmental controls
• Poor supervision of workmen
Cost due to non-conformance in manufacturing process. Non-conformance in the manufacturing process is an event that deviates from certain manufacturing protocols and criteria. Usually, manufacturing process management experts are keen to curb these losses. Non-conformance management solutions enable identification and documentation of these quality events, apply standard risk criteria to triage, route events appropriately and enforce structured failure analysis, root cause identification, quarantine and final disposition.
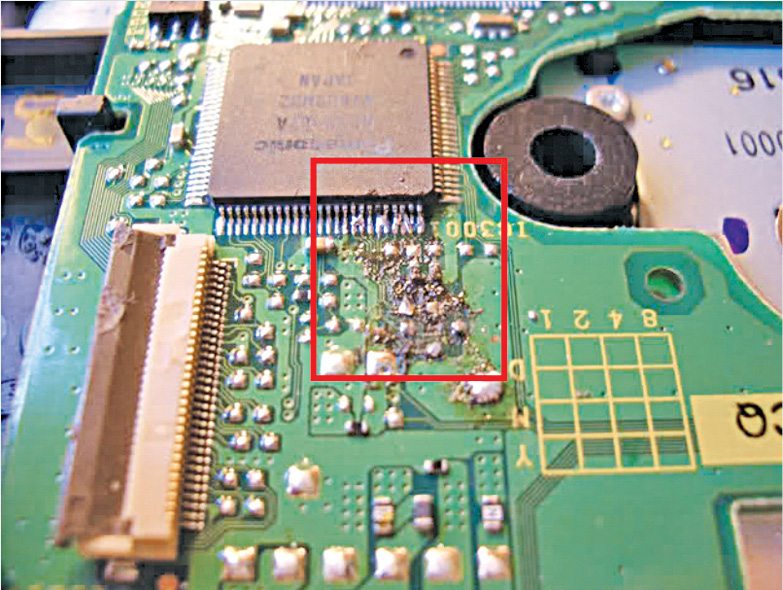
There are various factors in the manufacturing process that may incur as contribution to manufacturing defects. Some factors that are observed as part of the manufacturing process are mentioned below:
• Lack in availability or usage of electrostatic discharge (ESD) devices like ESD wristbands, ESD tables, ESD clothes and the like
• Human hair that may fall on PCBs/components in assembly lines and cause damage to the board due to ESD generated from hair
• Thermal balance
• PCB cracked or broken during assembly of QA/QC activities due to which component failure may occur
• Soldering problems
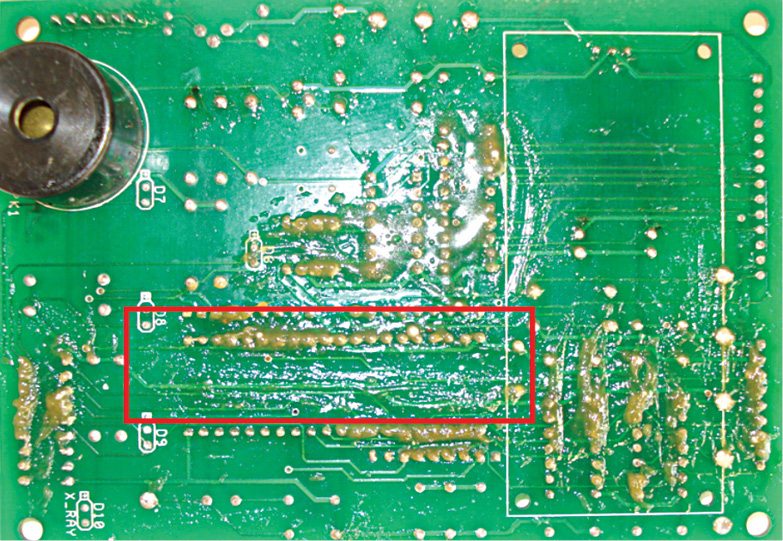
To cover the fabrication/assembly process and to measure the quality of manufacturing, there are some testing measures that need to be followed, a few of which are mentioned below:
• PCB analysis test
• Zero-value analysis
• Soldering evaluation and corrective action
A few examples of the type of quality non-conformance and damages that may occur in the manufacturing process and in the field are shown in Figs 2 through 6.
There are many dependencies in the manufacturing of consumer electronics products. Examples of dependencies are given below:
• Dependencies with system-on-chip manufacturer and vendor
• Dependencies with raw materials like small electronic and electrical components
• Dependencies with packaging vendors
• Dependencies with product body manufacturing vendors
• Dependencies with PCB vendors
• Dependencies with PCB layout vendors
• Dependencies with logistics vendors
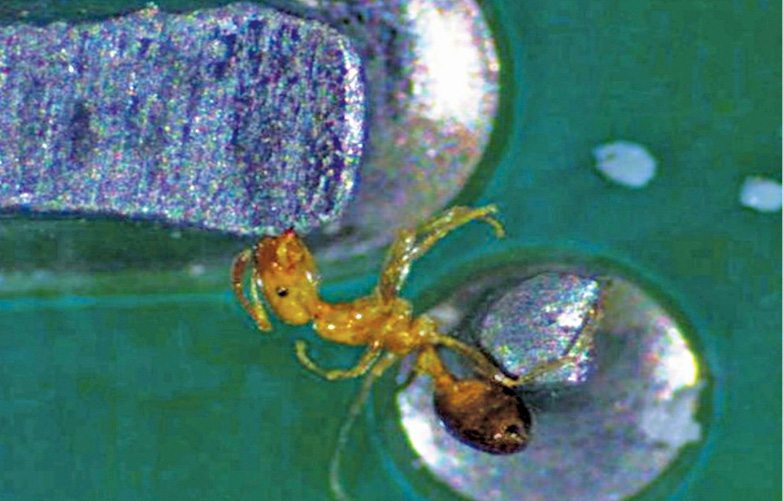
Despite these dependencies, it is a great challenge for manufacturing industries to sync with various vendors and maintain manufacturing process quality. Following are some possible impacts if challenges are not met appropriately:
• Increase in field call returns
• Increase in rework
• Increase in warranty cost
• Increase in scrap
• Increase in low performance in overall productivity
To address the above points, non-conformance management systems should ask the following questions during the manufacturing process:
• How long does it take to find, analyse and resolve manufacturing issues?
• Are you sure you have really solved the issue?
• Is the issue recurring?
• How do you implement and enforce preventive measures?
• Do you really have the data required to identify non-conformances?
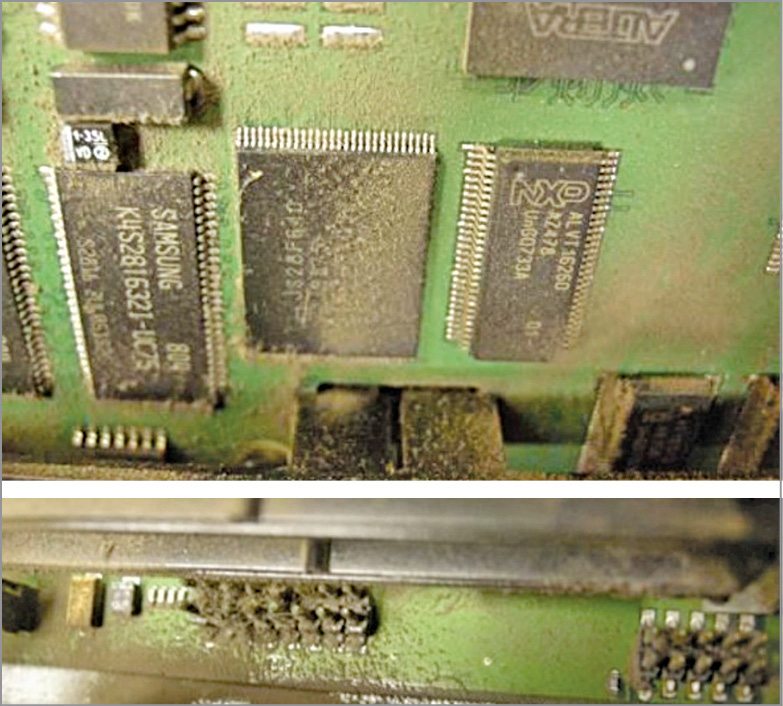
Non-conformance management systems teams usually work on the following mindsets:
• To identify any deviations in processes
• To identify quality assurance test results on product, packaging and product body
• To initiate appropriate actions to overcome the above two points
• To initiate field call returns analysis and take appropriate actions depending on analysis reports
Cost due to non-conformance in raw materials. To make consumer electronics products, we need many raw materials in the form of electronic, electrical, mechanical and packaging materials. These call for the involvement of multiple vendors to supply those raw materials. Hence, manufacturers need to evaluate the caliber of new materials that various vendors are offering. Examples given below show the problems that may occur due to non-compliance of raw materials:
• Failure of electronic/electrical components
• Damage of products during transportation due to inferior packaging quality
• Burning out of product
• Product malfunction due to environmental temperatures and other reasons
Hence, every industry should deliberate the following:
• Validate datasheet for raw materials that different vendors are offering; whether the datasheet meets product design principles
• Rate of failure of samples calculated per 100 samples
• Reliability of those samples
• Tolerance range
• Mechanical characteristics
• Packaging characteristics
Valuation of the above points may help decide which vendor to choose. It can also help boil down the field call return in the form of component damage, damage due to transportation, mechanical reliability and more. Meanwhile, it is also necessary to track and control, so that things are in place.
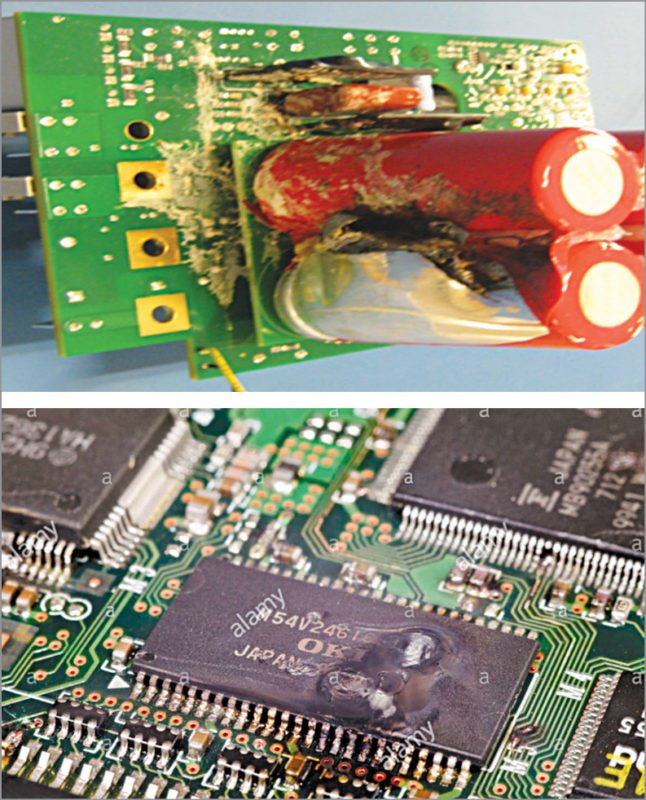
The above-explained cost of non-quality increases customer complaints and more returns, hence, higher warranty cost. This leads to the company using earnings for maintenance and customer satisfaction. Sometimes, cost of non-quality is so high that it brings down profit margins substantially.
Cost due to lack of service. Like manufacturing, supply chain management, design and development, customer serviceability is also important. Outstanding customer serviceability makes consumers become brand focused, and it also helps with word-of-mouth marketing due to customer-oriented service.
Subhabrata Chatterjee is senior technical specialist at TP Vision India Pvt Ltd, Bengaluru