SEPTEMBER 2012: Mentor Graphics Corporation is a world leader in electronic hardware and software design solutions, providing products, consulting services and award-winning support for the world’s most successful electronic, semiconductor and systems companies. Established in 1981, the company reported revenues in the last fiscal year of about $1,015 million.
In an interview with Pradeep Chakraborty, Dr Walden (Wally) C. Rhines, chairman and CEO, Mentor Graphics, and vice chairman of the EDA Consortium, USA, talks about the future prospects of the global semiconductor industry, the status of the global EDA industry, the advent of newer physical design capabilities, and what EDA now needs to do at handling 22nm and sub-22nm levels, and so on. Excerpts:
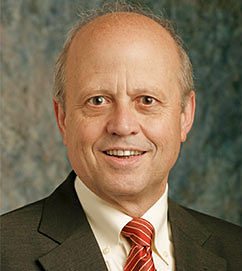
Q. How is the global semiconductor industry behaving at the moment? Do you see it going past the $310 billion mark this year?
A. The absolute size of the semiconductor industry (in terms or total revenue) differs depending on which analyst you ask, because of differences in methodology and the breadth of analysts’ surveys. Current 2012 forecasts include $316 billion from Gartner, $320 billion from IDC, $324.5 billion from IHS iSuppli, $327.2 billion from Semico Research and $339 billion from IC Insights.
These numbers reflect growth rates from 4 per cent to 9.2 per cent, based on the different analyst-specific 2011 totals. Capital spending forecasts for the three largest semiconductor companies have increased by almost 50 per cent just since the beginning of this year. However, the initial spurt of demand was influenced by the replenishment of computer and disc drive inventories caused by the Thailand flooding. Now that this is largely complete, there is some uncertainty about the second half.
So, overall it looks like the industry will pass $310 billion this year, but it may not be by very much. The strong capital spending and demand for leading edge capacity should impact the second half but the bigger impact will probably be in 2013.
Q. What is the current status of the global EDA industry?
A. Year 2011 was a record year in terms of total EDA revenue ($6,128 million: Silicon IP included), and the second highest on record (behind 2007) in terms of License & Maintenance revenue ($4,193 million).
Historically, the overall spending on EDA typically increases in line with semiconductor R&D spending, delayed by one year. Semiconductor R&D spending increased 11 per cent in calendar 2010, 6 per cent in 2011 and is likely to increase 12 per cent in 2012. If historical patterns continue, the strong EDA industry growth in 2011 should be followed by a good, but lower, rate of growth in 2012 and then acceleration in 2013. Current guidance by the major EDA companies supports this prediction.
Our forecast model (based on semiconductor R&D spending offset one year) predicts that EDA License & Maintenance Revenue will grow 3.5 per cent to $4,341 million in 2012. However, it probably understates the significance of the 28nm transition that is likely to increase semiconductor R&D-funded design activity this year beyond the current forecast. Moreover, with 20nm processes coming online in the latter part of the year, I expect the growth in EDA to continue at least through 2013.
New design methodologies traditionally drive almost all the growth in EDA. Most of the growth of EDA during the last decade came from DFM (including resolution enhancement), power analysis, ESL and formal verification. Currently, the new methodologies that are driving EDA growth are largely related to the 28/20nm transition or the increase in system design requirements for EDA. Examples include accelerated adoption of emulation, embedded software development/verification and ESL verification.
Q. Has the share of total IC production gone up, rather than being flat? Why?
A. EDA revenue, as a percentage of worldwide semiconductor revenue, continues at its long term level of 2 per cent with only a very slight decrease in the last 15 years. EDA cost per transistor continues to decrease on the same learning curve as semiconductor product cost per transistor, at about a 30 per cent decrease every year.
Q. How has been the foundry spending in 2012 so far?
A. Capital investment by silicon foundries, which had been flat for the previous decade at about $7 billion ($6.9 billion) per year, doubled in 2010 to $14 billion ($14.1 billion), increased again in 2011 to $19 billion and is now projected to maintain a level above $17 billion in 2012. Forecasts for overall industry capital expenditures have increased significantly since the beginning of the year.
Much of this change can be attributed to TSMC and Samsung, which are expected to spend $8.5 billion and $7 billion in 2012, respectively. TSMC spent approximately $1.64 billion of its capex budget in Q112. Capital expenditure plans for other major foundries include $2 billion for UMC, $430 million for SMIC and upwards of $3 billion for GlobalFoundries.
Despite all of this spending, 32/28/20 nm capacity is still fully loaded with demand for more. Improvements in yield and throughput on these advanced nodes will free up much more of this capacity as we move through the year.