Previously, electronic circuit simulation mostly focused on the analysis of electrical signals like voltage or current waveforms for analogue engineers and binary bit patterns for digital engineers. However, IC density has grown to billions of transistors, and now verification of system performance and reliability requires analysis of both thermal and electrical conduction, involving modelling of materials that were previously ignored.
In this interview, four industry leaders discuss whether multiphysics simulation really helps design engineers. Sudhir Sharma of ANSYS, Valerio Marra of COMSOL, Dr Detlef Schneider of Altair Engineering, and Kapil Gaitonde of SolidWorks spoke to EFY in this special interview.
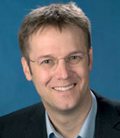
Q. What major electronics design challenges does simulation help tackle, and how has the emergence of a shorter time-to-market affected work practices?
Dr. Detlef Schneider (DS): Simulation technologies can have a much larger impact on the time-to-market and innovation, when used earlier in the design cycle. Instead of only validating designs, simulation and optimisation technologies have the potential to drive important decisions and help to make fundamental choices at an early stage. Industries such as automotive or aerospace already have proven that upfront simulation and optimisation provide great benefits.
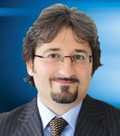
Valerio Marra (VM): The major challenge electronics designers are facing today is to build models that accurately represent their application. A shorter time-to-market calls for a reduction in the number of prototypes that need to be tested before committing a new design to manufacturing. An accurate model and simulation software that supports this objective is the solution.
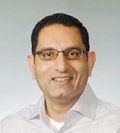
Sudhir Sharma (SS): To squeeze a higher performance out of electronics devices, engineers need to start looking at multiple physics. For example, an engineer needs to simulate the functionality of the silicon die with the die package and the board to ensure that the final product will work as specified. This requires high fidelity simulation models for each of the parts that can be simulated within a reasonable period of time. The short time to market has made high-fidelity simulation software a critical part of the workflow in organisations worldwide.
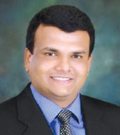
Kapil Gaitonde (KG): The primary challenge of realistic simulation will be to simulate real-world problems as they are. Obviously, this brings in a huge amount of complexity to theW task of problem definition, which leads to the requirement for specialised manpower and powerful tools. On the other hand, the design cycle for products is going down, companies are expecting innovative products to be released faster, and they have to also be of the best quality. Lack of time and tools leads to designers having to do re-engineering and innovation takes a back seat.
Q. How important and necessary is it to enable the re-use of model components here?
DS: It is important, not so much on the level of the simulation model, but more on the level of the physical description of the model. Different simulation disciplines require different numerical models. Preprocessing tools are getting so efficient, and process automation offers so much potential, that the re-use of models (other than making sure that the same geometry etc, is used) does not offer too much of an advantage.
VM: The first assessment of a product’s performance might include its mechanical strength. Once its structural integrity and weight goals are met, a designer might want to include other physical effects such as heat transfer and fluid flow. A simulation environment capable of handling multiple types of physics, one at a time or in any combination, to accurately simulate an application is mission-critical.
SS: Design reuse is a key enabling best practice with several benefits. First, reuse can reduce the number of bugs because, presumably, the piece of Intellectual Property (IP) being reused has been tested in previous products. Second, if a new product is largely based on existing IP, the amount of component level verification should be significantly less compared to products built with fresh IP. This can significantly reduce the verification burden and speed up the time to market.
KG: Irrespective of the new designs one makes, there are many components that are repetitively used or are a must in the product. Yes, there can be some minor changes made to them. Hence, it is important that the tools used by the designers enable easy reuse of existing data, to save the time that is spent in recreating the component.
Q. If you had to list three features that are most necessary in a multi-physics simulation product today, what would they be?
DS: Scalability. To solve increasingly complex models efficiently, it is important to leverage the growing number of available hardware/computer resources. Scalability also includes efficient handling of a growing volume of data.
High quality. Only a simulation model that captures physics correctly and where users can rely on the results, ought to be used to make decisions.
Robustness. Multiphysics simulation can be accomplished by methods ranging from direct integration in one solver, through one-directional coupling, to full co-simulation.
VM: Accuracy is of paramount importance when it comes to verifying and optimising a design. Two additional features that are also vital are the ability to couple any physics, and interoperability.
Designers need to be able to trust simulation results, mimic what happens in the real world, and use external data resources in the form of CAD files or material properties, for example.