There is a wide range of fault-insertion switching modules in PXI, specifically designed to assist the simulation of fault conditions in automotive and avionics applications that involve the reliability testing of safety-critical controllers. The block diagram (Fig. 2) shows how fault-insertion modules work in this test strategy. These switching modules are designed to route various fault conditions between a test fixture and the UUT, which include open circuit, short circuit between UUT connections and short circuits to other signals such as power, ignition and ground. Faulty serial buses can be injected into the circuit as well.
There are many fault-simulation systems that are available commercially. However, these tend to be proprietary to one vendor and might not work well with other vendors’ products, and can be very expensive as well.
Another key point in the selection of the PXI standard was the fact that every vendor offered software-driver support for real-time operating systems (RTOS)—a key requirement in HILS. The reason for RTOS is the deterministic nature of the test. Responses by the UUT, especially in the areas of active safety, need to be presented at exact times in order to protect the vehicle’s passengers.
The solution was accommodated in four 3U PXI chassis. Modular products included 24 modules to route fault-insertion signals (one module with 30-amp switching, 22 modules at 20 amperes and one module at 2 amperes) plus programmable resistor cards for sensor simulation. Other cards for FPGA functionality and CAN/LIN communication protocol support were also included. In addition to the cost and flexibility advantages already mentioned, the application of PXI solutions also improved the test system’s performance and cabling elegance in comparison to the original proprietary system.
2. Satellite payload testing
Customer. A satellite company delivering operational space missions for a range of applications including earth observation, science and communications. The company designs, manufactures and operates high-performance satellites and ground systems for a fraction of the price normally associated with space missions. These cost savings are achieved by implementing commercial off-the-shelf (COTS) satellite technology. This process takes standard consumer technologies such as those used in personal computers, and adapts these to the unique environment of space.
Application. Satellite payload testing is critical for several reasons. First, as the hardware is extremely expensive, a lot of testing is expected. Second, if a failure occurs after launch, it is extremely difficult, but not impossible, to return the entire product for service.
Satellites and payloads are complex systems made up from multiple mixed-technology sub-systems. The traditional approach to satellite development is a very linear fashion—specify everything upfront, design to specifications, test the prototype, then assemble and verify the flight unit. This approach is time-consuming and unsuitable for rapid, low-cost developments, which require more agile methodologies.
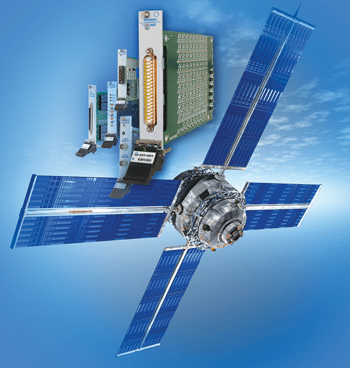
The use of simulation can provide major improvements on cost and time-scale. Using COTS components and standard tool-sets, a sub-system simulator can be developed and tested far in advance of flight-grade equipment, often at a much lower cost. This yields two major advantages to the project:
1. The designs are developed and progressed far in advance of the main development. This allows early detection and resolution of inherent design issues avoiding any costly rework of flight equipment.
2. Interface simulators can be used for system integration-testing, far in advance to identify and resolve sub-system integration issues. This is especially important for large-scale programmes where a single satellite may be made by many different sub-contracted manufacturers. Unlike hardware, the simulator is open, providing a much higher degree of debugging ability.
Solution. When specifying hardware for this latest simulation requirement, the customer chose not to base it on heritage tools and strategies, instead took a fresh look at what was available and possible. The goal was to find an optimally-engineered solution within a defined budget.
It was decided to base the hardware primarily upon the PXI standard. The reasoning behind this came down to one statement from the customer: “The solution fitted our requirement, as opposed to our requirement having to fit the solution.”
In the case of thermal control system, which monitors key temperatures within the satellite, PXI high-density precision resistor module is a key test product. Six modules were used to simulate 36 space-grade thermistors across their full range of -80ºC to +55ºC. These PXI precision resistor modules could cover the entire range of the thermistors requiring simulation.
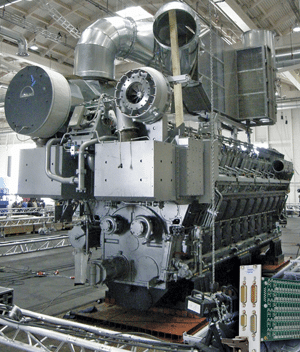
In addition to the precision resistor modules, switch cards for both signal and high-power switching, isolated power supply cards and MIL-STD-1553 bus analyser modules were used. The main functions of the switching modules were to physically isolate interface paths, simulate RF switch feedback contacts and distribute load channels across multiple paths.
3. Diesel engine temperature simulation
Customer. A manufacturer of large diesel engines, whose products are used in ships and power stations. Some of these diesel engines are being manufactured for a new class of container ships, which are among the world’s largest cargo carriers.
Application. The controllers for the massive diesel engines in ocean-going vessels require many temperature sensors in order to determine whether the engine is operating correctly. This is primarily because of the sheer size of the engine block. Many sensors are required to ensure that the engine operates in the correct temperature range and hot spots are identified quickly. It would be difficult to have an engine block available for system test, not to mention the time it would take for the engine to reach operating temperature. Sensor simulation provides a cost-effective means of testing the controller without having an engine on hand.
This requirement involved the support of ECU development for 40,000kW ship diesel engines. In terms of horsepower (HP), 40,000 kW equates to approximately 55,000 HP. Besides other ECU tasks, it was required to simultaneously simulate 144 channels of PT100 temperature sensors. These sensors are resistive temperature devices (RTDs) as opposed to thermocouples. The temperature range needed here was -20ºC to +250ºC, with an equivalent resistance range of 92.160342 ohms to 194.074250 ohms. Extreme precision was also required, demanding accuracies within 0.11ºC at -20ºC (equivalent resistance deviation within 43 milli-ohms) and 0.65ºC at 250ºC (equivalent resistance deviation within 220 milli-ohms).
The customer’s original method of sensor simulation was achieved manually. This comprised 288 precision potentiometers (covering both coarse and fine adjustment) along with 144 switches for short circuits, and 144 switches for open circuits in the simulation of faulty wiring connections to a sensor. All these components were adjusted and controlled by hand. The need for automation was obvious in order to save time and improve performance and repeatability.
Solution. With various measurement and stimulus modules already available in PXI and a requirement to support RTOS software, PXI was seen as the natural choice of platform for new product design.
The solution developed was a 3U PXI module that supports either six channels of RTD simulation (in one slot) or 18 channels (in two slots). Based upon existing design principles, the module provides a setting resolution of 2 milli-ohms and a resistance accuracy of better than 0.1 per cent on all channels. Each simulation channel is able to provide a short or open-circuit setting in order to simulate faulty wiring connections to a sensor. Furthermore, the calibration or verification of each resistor channel is possible by connecting the module calibration port to a high-performance digital multimeter.
The use of simple resistance value calls makes programming simple. This was achieved by using an application programming interface (API) to convert temperature request into resistance request through a model of the sensor used in the real engine.
The end product enabled a cost-effective method of simulating either PT100 or PT1000 RTDs with very high accuracy. Eight modules achieved the 144 channels of PT100 required in this application (18-channel two-slot modules), accommodated in sixteen slots of 3U PXI chassis space.
A ‘simulated’ conclusion
From these three applications it is clear that PXI products can simulate the signals necessary for a variety of applications including consumer, transportation and aerospace. PXI can achieve the densities required to make the system manageable on the test floor—accurate enough to meet customer demands and support specialised environments like RTOS.
Shaun Fuller is switching product manager and Bob Stasonis is Americas/Asia sales & marketing director for Pickering Interfaces