3D printing, also known as additive manufacturing, is considered to be a disruptive technology that could power the next industrial revolution. It could transform the way designers visualise concepts, the way companies do businesses and, particularly, the way manufacturers make products.
When the design process moves forward technical decisions are iteratively tested to achieve improved performance, lower manufacturing costs, deliver higher quality and more successful product introductions. In pre-production, 3D printing is enabling faster first object production to support marketing and sales functions, and early adopter customers. And in final production processes, 3D printing is enabling higher productivity, increased flexibility, reduced warehouse and other logistics costs, economical customisation, improved quality, reduced product weight and greater efficiency in a growing number of industries.
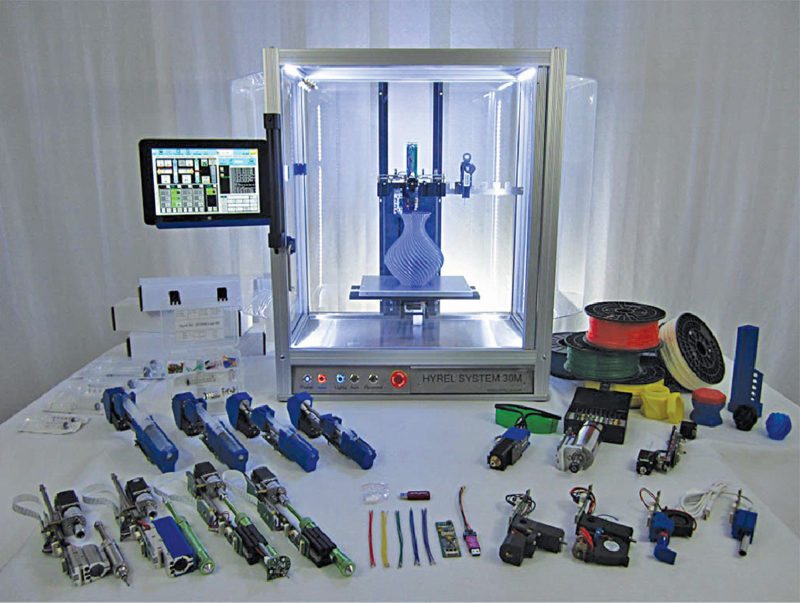
Current technologies
A large number of additive processes are now available. The main differences between processes are in the way layers are deposited to create parts and in the materials that are used.
Some methods melt or soften the material to produce the layers. Some examples are: selective laser melting (SLM) or direct metal laser sintering (DMLS), selective laser sintering (SLS), fused deposition modeling (FDM) or fused filament fabrication (FFF).
Some other methods cure liquid materials using different sophisticated technologies such as stereolithography (SLA).
“Different types of 3D printers function on a different technology that uses different materials in different ways. One of the most basic limitations of 3D printing in terms of materials and applications is that, there is no one solution that fits all,” says Karan Sangani, business development manager, MaherSoft.
Attributes to consider
Selection of the right 3D printer depends on the application requirements and matching the key performance criteria that will provide the best all-around value. Here are some 3D printer performance attributes to consider when comparing various 3D printers:
Print capacity. Right from prototyping stage, it is critical to print full-size parts to test the product in real conditions, so the build volume (size) is the key. The largest build volume is available with SLA technology.
Speed vs quality. There is a trade-off between print speed and print quality. The quality of your print (product) depends on the size of the layers you use, but it also depends on the precision of the extruder (nozzle head). Heated build plate and precise nozzle alignment of the machine ensure high print quality. Printers with low layer thickness settings may take longer to produce a final print, but these generally produce a smoother finish. The best printers offer a wide range of quality settings, from fast (but low quality) to slow (but high quality).
Size of filament. All 3D printers have a unique set of temperature, speed and functional ranges in their respective designs, which you should review and consider when selecting filament. Most commonly used printing filaments are ABS, PLA, HIPS and PVA available in, generally, 1.75mm and 3mm diameter.
Availability of support. While buying a 3D printer, look for long periods of warranty. Most large 3D printers, especially those that come from big-name manufacturers, offer some type of specialised support. You can typically contact these companies for ‘live’ help and support over the phone, through email or live chat on their websites.
Sangani mentions, “Most of the buyers make their decision of buying a 3D printer based on cost. We highly recommend buyers to make their decision based on print quality and service support from the manufacturer.”
Frahan Shaikh, founder, Mattermatic, says, “The print time and quality can vary due to factors like layers and print speed. Fine print quality requires more layers in an object but it also increases the printing time.”
Application areas
Your selection of the printer has to be based primarily on the use you want to put it to. A printer useful for one type of application may not be useful for another type. See if the printer you are considering is for one of the following applications.
Industrial.
Automotive. To build tooling, jigs and fixtures from high-performance engineering thermoplastics using FDM technology
Construction. Super-size printers use special concrete and composite mixture that is thicker than regular concrete
Space and Defence. To print spare parts for planes or satellites using FDM technology
Healthcare. For implants and prosthetics, surgical guides, hearing aids and tissue engineering, etc
Computers. To make cases for laptops and other computers
Apparel. For clothing, consumer-grade eyewear, etc.
Manufacturing.
Mass customisation. To customise 3D printed unique objects using simplified web based customisation software
Rapid manufacture. SLS and DMLS processes are enabling better rapid prototyping methods
Rapid prototyping. Rapid prototyping for research purposes using powdered metals, casting media, plastics, paper or cartridges
Entertainment.
Film & Animation. For visual mock-ups, photo/film shoots and master patterns for moulding; ready for chrome or copper plating, PU finish, investment casting, etc
Trophies. Complex trophies can be made quickly with a surface finish that requires little or no hand finishing
Social.
Gifts. You can 3D print your child a toy, yourself a smartphone case, or your loved ones jewellery or chocolate/candies
Medicines. To produce your own medicine or household chemicals
Not all 3D printers come assembled; some of these come in DIY kits form, like the Makeblock Constructor 3D printer. This often results in price savings as the manufacturer does not need to assemble, calibrate and test the machine.
Open source robots are being built using 3D printers. Double Robotics grants access to their technology (an open SDK). On the other hand, 3&DBot is an Arduino 3D printer-robot with wheels and ODOI is a 3D printed humanoid robot.
Cost
The main considerations in choosing a 3D printer are generally speed and cost. For the printed prototype, choice and cost of the materials, and colour capabilities are important.
Right now, the least expensive 3D printers are those using FDM technology. Entry-level printers cost ₹ 20,000 to ₹ 80,000. These use standard filament, can print onecolour/material at a time, and have small build size. Most FDM printers use only PLA and/or ABS material.
Better printers cost ₹ 60,000 onwards. Some of these can print two colours/materials at a time; they usually print at finer resolution to get smoother surfaces. Moreover, the build size is larger, so you can print larger objects.
If you are good with your hands and tools you may buy a printer kit and assemble the printer by yourself. Prices of kits start at ₹ 6000 and go up to a few thousands. Bobs CNC RP9v2 Deluxe, Reprap Guru Prusa I3, HICTOP Auto Leveling Desktop, OneUp v2, HICTOP Desktop 3D Printer are all under ₹ 30,000 3D printer kits.
More expensive printers use SLA (stereolithography) or SLS (selective laser sintering) technologies. SLA printers use a laser or digital projector and photosensitive resins.
Prices, of course, depend on materials’ cost, in-fill, size of the item to be printed and many other factors. Both proprietary and generic brand filaments are available in many different sizes and colours. If you wish to save money in the long run, a printer that accepts generic or cheap filament can help cut down long-term costs.
Frahan says, “3D printers today can be used to make everything from paper clips to jet engines. The same goes for market value because desktop FDM 3D printers are available under ₹ 100,000 while industrial ones can cost well over ₹ 100,000.”
“The major advancement happening with respect to FDM is scaling down of the cost of 3D printers using this technology,” informs Prudhvi Reddy, co-founder, Think3D.
Nitin Gandhi, co-founder, LBD Makers, says, “For printers within this price range, recent notable additions have been Wi-Fi connectivity, auto bed levelling, Bluetooth connectivity and dual nozzles.”
Sangani adds, “MaherSoft’s core competency is to build high-quality FDM 3D printers at an affordable cost, making it more accessible to the masses. MaherSoft will be launching a crowd funding campaign on Indiegogo, where the Indie-Desktop 3D printer will be available for a pre-order price of approximately ₹ 30,000.”
Will 3D printing live up to the hype
Despite its value in rapidly creating prototypes, 3D printing has very limited application as a production process. That is because 3D printing is intrinsically serial in nature; each unit of material has to be laid down sequentially. As a result, 3D printing is very slow relative to an intrinsically parallel process like moulding, in which the material transformation happens simultaneously for the whole object.
For instance, an injection moulding machine in a factory can spit out 100 perfect plastic spoons every 15 seconds. The best 3D printers can produce one not-quite-as-good spoon in ten minutes, which is 4000 times less productive. So the plastic spoon you get at the ice cream shop will never be 3D printed.
There will, however, be two areas in which 3D printing will likely serve as a production process. First, for parts that experience low, highly sporadic demand, 3D printing on demand will be more efficient than holding inventory of little-used items. Someday, if you need to replace a bracket on a vintage motorcycle, your supplier will probably 3D print the part.
Second, applications that benefit from true customisation may employ 3D printing. You don’t need a custom ice-cream spoon, but you would benefit from a custom implant when your hip needs to be replaced.
3D printing is a fascinating technology. It is already being used by almost every product designer as a prototyping technology. But it won’t alter the fundamental economics of production. 3D printing will make inroads in applications where demand is highly intermittent, and where true customisation to the unique characteristics of the customer is valuable.
NASA has already tested a 3D printer on the International Space Station, and recently announced its requirement for a high-resolution 3D printer to produce spacecraft parts during deep space missions. The US Army has also experimented with a truck-mounted 3D printer capable of outputting spare tank and other vehicle components in the battlefield.
3D printers may also be used to make future buildings. To this end, a team at Loughborough University is working on a 3D concrete printing project that could allow large building components to be 3D printed on-site to any design, and with improved thermal properties.
Chinese company Winsun claims to have built ten 3D constructed houses in one day at a cost of just US$ 4800 per house! In addition to making housing more affordable, many architects also hope that 3D printing will increase their ability to customise homes and buildings.
Another possible future application is in the use of 3D printers to create replacement organs for the human body. This is known as bio-printing, and is an area that is rapidly developing.
Cost-effective, customisable 3D printed prosthetic limbs have revolutionised the medical sector and will further fuel 3D printing medical applications.
As per Frahan, “The future belongs to low-cost 3D printing. As awareness about the technology grows and more users come on board, even the types of 3D printers will increase. In short, there is already something for everyone, no matter how specialised their need, and that is only set to grow.”
SmarTech says they have developed a customer adoption model for 3D printing, which is specifically tailored to the automotive industry. The primary application of 3D printers in automotive is for prototyping and tooling.
The US Department of Energy Advanced Manufacturing Office showed that the weight of certain aircraft can be decreased by as much as 7% by using 3D printing to replace certain conventional methods. And GE’s 3D printed LEAP engine fuel nozzle has been estimated to cut fuel costs (and CO2 emissions) by 15%.
So 3D printing has a bright future, both here on Earth and in space.
Biswajit Das is manager-R&D, EFY Labs