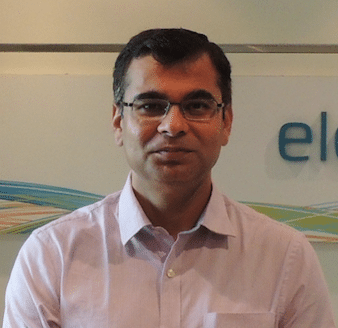
When choosing a switch means more than just the ‘ON’ and ‘OFF’ function
A switch might seem insignificant because of its ubiquitous presence, but the ideology behind the utilisation of a switch comes in the wake of the functional demand and surrounding conditions.
The preliminary jobs of a switch are the ON/OFF functions or rather the START/STOP functions. In a basic switch, this is achieved by the position of metal surface contacts and a mechanical plunger. The contact surfaces provide a plane for the flow of electricity when the switch is ‘ON’ and the contact is broken apart when the switch is ‘OFF’, to stop the current flow. But for more complex and accurate processes, different working methodologies and technologies come into play.
To arrive decisively at a solution for choosing an appropriate switch, you must zero in on the working conditions, and the different criteria the switch must possess to function effectively. These could include the mechanical strength, contact surface quality or even resistance to flux/current leakage. And the working conditions range from industrial to household utilisation.
Contamination of Surface Contacts
When surface contamination occurs while constructing a mechanical switch, the usual approach would be a protective silicone lining to protect it. But this only protects the surface from dust. In mechanical switches, the presence of a metallic contact plate increases the possibility of surface corrosion and oxidation. This will result in the gradual wear and tear of the surface contact which could lead to a dampening of the flow of current and ultimately, a breakdown in working ability. Also, contact surface can produce high flux which can result in a deposit of silicone residue at intricate points. This is avoided by using certain corrosive-resistant materials and poor electrical conductors such as gold or nickel-based alloys. This occurs with regular wall mounted switches and can be avoided using high quality reinforced surface contact switches. Companies like Honeywell and Apem are leading manufacturers in this division.
In an electrical switch, the contact plate is swapped with a semi-conductor diode. The p-n-p junction diode works in accordance to the flow of current through the semi-conductor. The ‘ON’ position is achieved through a voltage and the ‘OFF’ condition is achieved by inducing a reverse breakdown voltage. Hence in this condition, contact surface corrosion is a miniscule problem in comparison to the flow of current. To govern this flow of current, dampers and improved soldering techniques are employed to absorb stray currents.
Contact Surface Material
The material of the contact surface is determined purely by its functional environment and industry need. The switches used in households employ different contact surfaces as opposed to manufacturing industries and corporate offices which employ 100+ individuals.
Different materials used at the contact surface possess target specific properties. For example, a switch which uses Pure Silver (99-9% Ag) as a contact possesses high electrical and thermal conductivity, low contact resistance and operates at a low contact force. This is used in thermal heaters and appliances because of its enviable resistance to heat and electrical flux.
An alloy known as Coin Silver (90% Silver and 10% Copper) can withstand high pressures because of its hardened surface. It is also cost effective to produce and hence, is used in automotive relays. These relays are used in digital equipment and encoders as well as medical devices. C&K is the global leader in this division due to its high quality and increased demand from engineers around the globe.
Shape of Contacts
The types of mechanical designs which go into the construction of a contact surface depend upon the metal and resistive advantages. In hindsight, their physical properties, which when designed in a fashion, provides a specific switching operation for a target industry.
Take the example of solid riveted contacts. They are usually made of high density metals such as Silver alloys and Palladium (Pd) alloys. These surfaces are for simpler applications and are used for more economical reasons.
Cladded and riveted contacts are Silver alloys with copper (<10%) and are supported rivets with a thick shank. The high strength it possesses is the sole reason for the employment of these contacts in the Automotive, Power Engineering and Communication industry.
In accordance with the shape and design, there are different surface contacts employed, namely:
• Contact rivets with brazed surface layer – Power Engineering applications.
• Contact screws – Adjustable contacts for Controls and Horns.
• Vertically welded wire segments – Economical Manufacturing at higher quantities.
• Horizontally welded wire and profile segments – Measurement Devices and Controls.
• Tungsten weld buttons – Ignition Points and Arcing Contacts.
• Seam-welded contact strips or profiles – Switches, Pushbuttons, Relays, Auxiliary Contactors and Sliding Contacts.
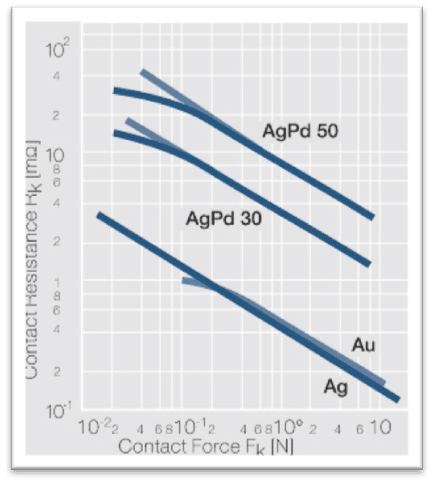
These are some of the many shapes and their proven uses.
Switch Damage Due to High In-Rush Currents
In the case of contact switches that employ a semi-conductor which works on the electric principle that governs the functioning of a diode, a factor that should never be ignored is the in-rush current. This current, represented at times as ‘I2’, is a phenomenon where when a capacitor is entirely discharged, a charging current, like an electrical short may occur during the first micro-seconds of the inrush process. This surge in current can cross the half-life of the metal’s electrical conductor capacitance and decrease its overall function-ability with time.
This is controlled by using a high capacitive limiter which is either made of Tungsten (Tg) or Nickel (Ni) alloys and basically serves as a current limiter, to provide the dampening of the inrush current.
Arching and its prevention
In switches working on the electrical principle of a diode, a luminous discharge of highly energized electrons and ions or a ‘spark’ is noticed when the contacts separate. This is known as ‘Electrical Arcing’ and it cannot be prevented but only reduced with precautionary measures, known as ‘Arc Suppression’.
Arcing is dangerous as it can result in circuit failures and in worst cases, a fire in the circuit box that could ultimately spread and damage property as well as cause harm to human life.
The best, most effective and cost dynamic method to prevent mishaps in the case of arcing is with the employment of an Arc Fault Circuit Interrupter (AFCI).
An AFCI serves the function of a circuit-breaker when it detects an electric arc in the circuit. The AFCI is designed in a unique way to selectively distinguish between a harmless arc (common to the normal operation of switches and plugs) and a potentially dangerous arc.
Different companies manufacture AFCI’s in accordance to the need and size. Schneider Electric is a giant in this industry and controls a fair share of the market space with its cost effective and qualitative AFCI’s.
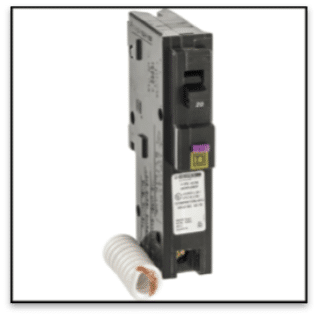
Magnetic Reduction of Arcing in DC Switches
DC switches are rarely employed due to the invention of the AC switchgear. But the utilisation of DC switching technology still prevails in certain niche categories of manufacturing and automation, especially in heavy industrial tools.
In this scenario, an electromagnetic circuit breaker is provided with a pair of magnets on opposing sides of the contacts in the open position. The combination of these magnetic fields deflects the arc current, shifting the arc current away from the contact points and lengthening the path of the arc, thereby increasing the voltage rating of the breaker, by decreasing the intensity of an associated arc current. With a reduction of its intensity, the danger involving the arc is reduced to a minimal non-threatening spark.
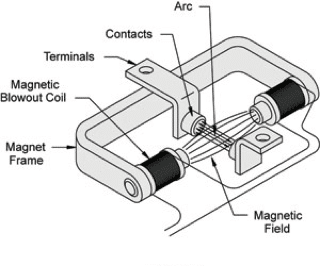
Moving Beyond Physical Switching
From Pressure Switches to Biometric switches, different approaches have swept the industry away.
A Pressure Switch functions on the principle of acting fluid pressure on a surface. When switched on, an electrical contact is closed and the charge is conducted, thereby performing the switching action. The design of the switch can vary, that is switching action can take place either with the rise or fall in fluid pressure. Pressure switches find its application in heavy industries to automatically supervise and control systems that use pressurized fluids.
A Biometric Switch works on the digital fingerprint recognition technology. The data is hosted either internally or externally, and a positive match will bridge the contact to provide current flow and thus, a timely switching action.
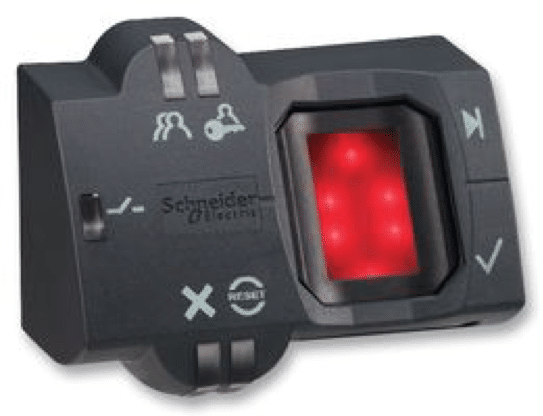
In hindsight, switches are much more than just something to turn things on and off. By choosing the right switch, you can not only ensure that your system doesn’t encounter problems/failures, but also optimise the operation and user interface. Choose the best by relying on the best.
element14, the Development Distributor, provides a range of over 7,000 switches to address these issues, including MicroSwitches, Rocker Switches, Push Button Switches, Toggle Switches, Rotary Switches and more, in stock and ready to ship today.