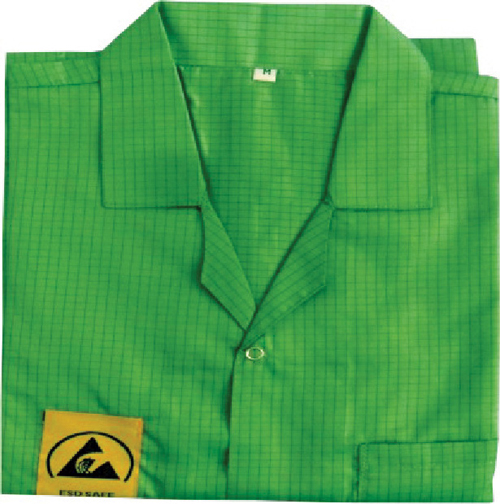
ESD garments. The standard document ANSI/ESD STM2.1 defines test methods for determining the electrical resistance from sleeve to sleeve and point to point of static control garment.
As described in the document, the sleeve-to-sleeve method is intended to test the integrity of the electrical resistance across the seams of the garment, whereas point-to-point test method is intended to test the electrical resistance between two points on the garment, which may include the electrical resistance across the seams of the garment. The resistance range suggested by the document is 1×105 ohms to 1×1011 ohms. Most of the manufacturers do not mention such values in the datasheet, but they do mention that the garments are tested as per ANSI/ESD STM2.1 standard. So look out for that.
2. Grounding of work surface. It is extremely important to ground the work surfaces. The work surfaces that we discuss here are workstation surface and floor.
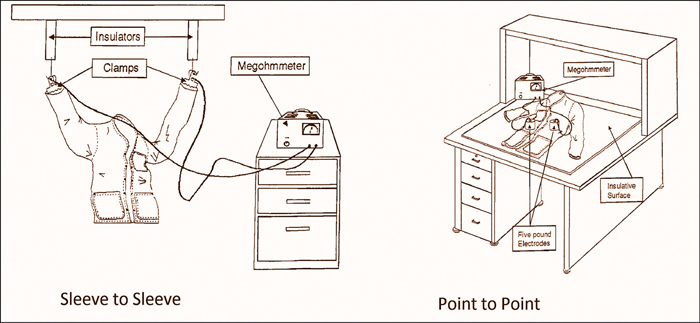
Workstation surface. ESD mats should be used to cover the complete bench top. The mat needs to be grounded. The best practice is to use metal grounding hardware snaps and ground cords connecting the work-surface mat to the common-point ground.
ANSI/ESD S4.1 standard provides test methods for evaluating and selecting work surface materials, testing of new work surface installations, and testing of previously installed work surfaces.
In the document, the guidelines for work surface are:
• Resistance-to-groundable point: 1×106 to 1×109 ohms
• Resistance from point to point: ≥1 mega-ohm
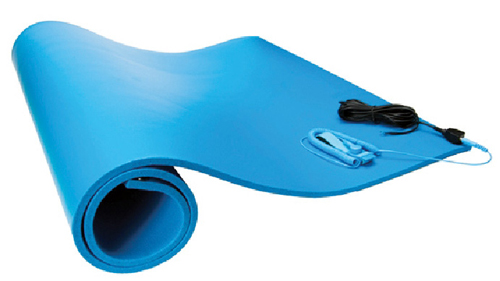
These guidelines represent a range of resistance that has generally been proven to provide protection in the manufacturing environment. If the mat’s resistance is too low, static transfers to the mat will be so fast that a spark is created. This spark is an electrostatic discharge that will damage electronic devices. If the mat’s resistance is too high, static transfers so slowly that items placed on the mat will not lose their charge. When the item is removed from the mat, it will still have a static charge and will be capable of discharging to other items.
A mat’s performance is based on the material used to make it. Performance includes electrical values, tolerance to heat, chemicals and mechanical abrasion.
Vinyl and rubber are widely used in making the mats. Vinyl is used in most cases. Rubber is used when the required resistance to heat and chemicals is high.
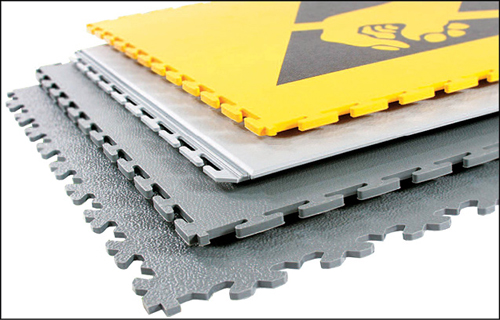
Flooring. First, decide the type of flooring you will use: conductive (electrical resistance to ground range: 2.5×104 to 1.0×106) or dissipative (electrical resistance to ground range: 1.0×106 to 1.0×109). Dissipative floors cost the least, but if the floor is used as a primary ground for people and carts, a conductive floor should be chosen.
ANSI/ESD S20.20 requires the system resistance of a person through the floor and to ground of less than 3.5×107 ohms (35 mega-ohms) when floor is used as the primary ground. S20.20 allows static dissipative floors as long as the resistance to ground from anywhere on the floor is less than 1×109 ohms and personnel do not generate greater than 100 volts using the ANSI/ESD S97.2 test method.
There are various options available (mats, tiles, etc). Make sure that the one you choose complies with the standards mentioned above.
3. ESD protective tools and workstation. When working with sensitive electronic components, you should consider buying anti-static or ESD-safe equipment for your workstation.
The materials mentioned below are optional but can be used for better electrostatic-protected area:
A bench-top ioniser can be used to neutralise electrostatic charges at the workstation. This is the only ESD control method available to neutralise electrostatic charges on essential insulators or isolated conductors that may be at the workstation.
The required limit according to ANSI/ESD S20.20 is less than ±50V offset (balance). In addition to that, the discharge time to reduce +1000 volts to +100 volts and to reduce -1000 volts to -100 volts should be measured. The faster the static elimination time, the better. Do look for one that strictly complies with ANSI/ESD S20.20.
5. Proper packaging. Place sensitive items in an appropriate protective packaging when transporting or moving to storage. The cost of static-protective packaging is insignificant compared to the losses incurred without them.
One of the most common static-preventing elements is a bag. Static-protective bags are an integral part of a static control programme. Selecting an appropriate bag can help reduce static damage and save money on costly repairs and rework.