Some latest DC-DC converters are introduced here, along with the basic and new features, so that designers can select the best devices for their applications.
DC-DC converters are important parts of modern automobiles and industrial applications. This is because direct current (DC) power supplies are used in almost all the electrical devices in automobiles and other industrial applications.
A DC-to-DC converter is basically a DC electric power converter required in some devices because the standard DC sources (mostly batteries like 1.5V, 6V, 12V) available are either too high or too low in voltage to drive a particular circuit or gadget. Therefore some form of power conversion, either step-up or step-down, is required from a standard DC source.
For example, most mobile devices have 3.7V batteries. To charge them from a 12V car battery would require a DC-DC converter circuit because 12V is too high to charge a 3.7V battery. Again, most of the embedded system circuits in automobiles and industrial applications require either 3.3V or 5V DC sources, so you need power converters to drive them from a 12V battery. DC-DC converters are also used in many consumer electronics and domestic electrical systems.
Power levels of DC-DC converters vary from very low (in small batteries) to very high (for high-voltage power transmission). Most of these converters are available as integrated circuits (ICs) and do not need many external components. These are available as complete hybrid circuit modules or as plug-in modules ready to use in an electronic assembly. Most power converter ICs include an integrated power MOSFET and are classified as regulators because they regulate the output voltage.
This article covers different types of DC-DC converters newly released/announced by different manufacturers for automotive and industrial applications. To better understand the features of these converters, let us first have a look at some major types of DC-DC converters available in the market.
Types of DC-DC converters
The major DC-DC converter types are linear, switched mode, non-isolated, and isolated.
Linear. It uses resistive voltage drop to create and regulate a given output voltage. A linear converter can generate a voltage that is lower than the input voltage.
Switched mode
It converts DC voltage level by storing the input energy temporarily and then releasing that energy to the output at a different voltage. Energy storage can be done in either a magnetic field component like an inductor or a transformer, or in an electric field component such as a capacitor. Transformer-based converters provide isolation between the input and the output.
Non-isolated
This converter is used when change in the voltage is small. It does not give protection from high electrical voltages and noise. The converters in this group include step-down (buck), step-up (boost), and buck-boost converters.
Isolated
It has a separation between input and output terminals. It has high isolation voltage properties and can block noise and interference. It also has cleaner DC output. This group includes flyback converter and forward converter.
Common parameters/specifications
It is important that a DC-DC converter operates within the range of required DC parameters for a particular application. After understanding the different parameters of the converters, system designers can choose proper DC-DC converters for their applications. The most basic DC parameters are the input voltage range, the output voltage range, and the maximum required output current.
DC input is an important parameter in DC-DC converters. Input voltages include 12V, 24V, 48V, 110V, 280V, and 360V. DC output is another important parameter to consider in DC-DC converters. Common output voltages are 3.3V, 5V, 12V, 15V, 24V, and 48V.
Other parameters include output power, line regulation, load regulation, minimum load, operating temperature, PCB footprint area, and topology. The most common DC-DC converter topologies are buck, boost, and buck-boost (flyback). Common features for DC-DC converters include constant current, over-voltage protection, over-current protection, and short-circuit protection.
Constant current provides constant output current, irrespective of the changes in load impedance. Over-voltage protection limits or shuts down the voltage output when over-voltage condition occurs. Over-current protection limits or shuts down the current output when over-current condition occurs. Short-circuit protection protects the converter in the event of a short circuit at load end.
Some new features in DC-DC converters
There are many new features being added in some latest DC-DC converters. Apart from the wide range of input and output voltages, new features may include noise optimisation, higher efficiency, digital interface, power management, multi-channel input and output, remote control, ensuring compliance and compatibility, safety standards, among others. Table 1 lists different DC-DC converters released/announced recently by some manufacturers.
Noise becomes an important parameter to consider for better performance and accuracy in DC-DC converters. Optimising a DC-DC converter for noise and electromagnetic interference (EMI) would enhance the performance of the power supplies in automotive and industrial applications. Electromagnetic compatibility (EMC) standards ensure proper operation of the equipment and control of EMI, so that unwanted effects are prevented.
For example, Flex’s BMR683 DC-DC converter has EMC specification according to EN55022/EN55032, CISPR 22/CISPR 32, and FCC part 15J regulations. Flex’s PUB-2M series has conducted EMI tests according to EN55032, CISPR 32, and FCC Part 15J. Traco Power’s TMR 4 series has EMC specifications as per EN55032, and FCC Part 15, both Class A and B.
Digital interface is becoming more popular in modern converters. Traditional way of controlling DC-DC converters using analogue techniques was simple to implement. However, over the past several years, with innovation in electronic devices—such as high speed, low power consumption, better efficiency, and inexpensive semiconductors—digital control is found much more advantageous over analogue techniques. DC-DC converters with digital interfaces are digitally controlled power sources that provide accurate and adjustable levels of voltage, current, and power. Digital control may include a processor, voltage/current programming circuits, software, current shunt, and voltage/current read-back circuits.
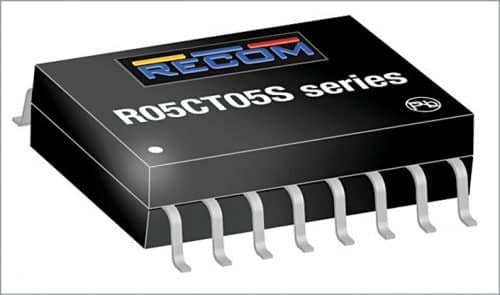
For example, Flex’s BMR683 DC-DC converter has a PMBus digital interface that enables the user to configure many aspects of the device operation through software control. It can be used with any standard two-wire I2C or SMBus host device. Rohm’s BD71850MWV DC-DC converter has digital I2C interface with clock frequency up to 1MHz. Diode’s AP61100Q converter has programmable operation mode through digital input that turns the converter on or off.
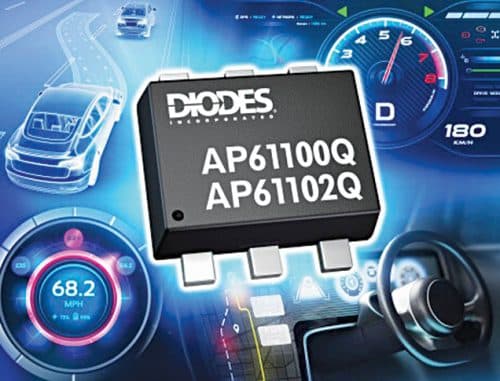
Power management feature is included in some newer DC-DC converters. For example, Flex’s BMR683 DC-DC converter has power management feature that can be configured using its digital interface. Its software suite can be used to configure and monitor this product via the PMBus interface. It incorporates a wide range of configurable power management features that are simple to implement with a minimum of external components. Rohm’s BD71850MWV DC-DC converter is a programmable power management device for powering single-core, dual-core, and quad-core SoCs such as NXP-i.MX 8M Nano.
Efficiency is an important design parameter of DC-DC converters. Along with innovation and introduction of CMOS devices, digital control can improve the efficiency of a previously analogue design. With careful design, modern switching regulators/converters can achieve 90 percent efficiency and even more. For example, BMR683 can have high efficiency, typically 95.5 percent at full load. BD71850MWV has its efficiency target between 83 percent and 95 per cent. Murata’s UWE-Q12 series DC-DC converters have efficiency up to 92 per cent.
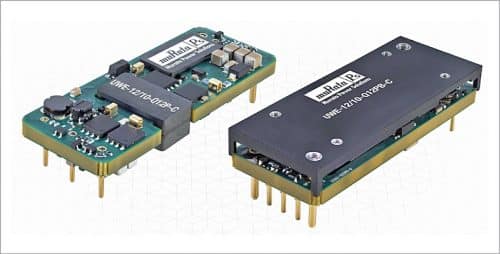
Multi-input multi-output (MIMO) feature in newer DC-DC converters allows users to integrate multiple input sources and multiple output loads simultaneously. That is, this type of converter allows input sources to be added or removed seamlessly without cross-regulation problem. It is easy to achieve high extension capability for arbitrary inputs and outputs. For example, BD71850MWV integrates six buck regulators and six low-dropout (LDO) regulators to provide all the power rails required by the SoC and the commonly used peripherals.
The soft-start function in DC-DC converter is used to prevent large inrush current and output voltage overshoot. The function could be with an internally fixed soft-start time, or externally adjustable soft-start time, setting pin and externally adjustable oscillator duty cycle. Soft-start function is included in many DC-DC converters including BMR683, BD9P1X5EFV-C, BD9P2x5EFV-C, BD71850MWV, UWE-Q12 series, and AP61100Q.
Some DC-DC converters are integrated with remote control function, offering a convenient way to control your application. The control could be through a wire or wireless using infrared (IR) or some other wireless technology. For example, UWE-Q12 series has a remote sense circuit through which the product can be controlled using IR technology. TMR 4 series converter has dedicated pin for remote control function.
Ensuring safety is paramount to product users and industry. Adequate safety measures include fail-safe design against physical injury, damage to property, failure, or malfunction of a product. There are many industry safety standards that require restriction of hazardous substances or RoHs compliance, such as IEC/EN/UL safety requirements, Automotive Electronics Council (AEC) quality standards, etc. For example, BMR683, PUB-2M series, UWE-Q12 series, 0RQB-50Y05x and TMR 4 series meet safety requirements according to IEC/EN/UL62368-1, while BD9P1X5EFV-C, BD9P2x5EFV-C, and AP61100Q are AEC-Q100 qualified.