The idea of 3D printing technology was first introduced back in 1984. Though 3D printing is now utilised in a variety of applications, this concept is relatively new for the Indian industry.
In the field of electronics
Karan Chaphekar of KCbots says, “3D printing has yet to percolate everyday life, but at present, the main application is in rapid prototyping by an engineering and design team (at a start-up, SME, etc) or by hobbyists who want to make unique things.”
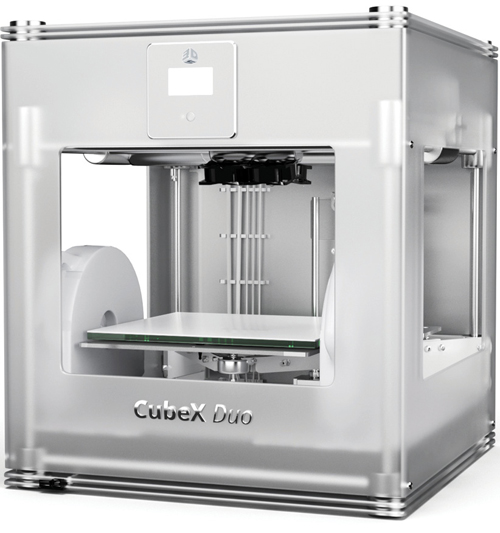
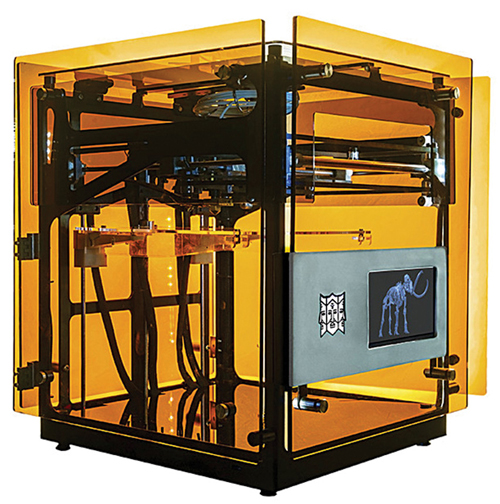
A basic 3D printer can be of great advantage for electronic product designers or innovators. According to Paul Anand of Biotz, “The most important part lies in mechanics designs of any electronic gadget they design. In this era, user-centric design is becoming the key differentiator for product optimisation.” A 3D printer lets the user create rapid prototypes of different designs, which can be sent for user feedback and optimisation. It reduces the size of product considerably and saves time and effort.
Attributes to consider
Print speed. The speed of a printer can be defined as the time taken to print a specific distance in the Z-axis. It is usually represented in millimetres per hour or inches per hour. With larger print speed, we get the model printed faster. However, print speed may depend on some other factors such as complexity of the model to be printed or type of printing material used. Print speed determines how fine and dense your structure will be printed. The speed generally has an inverse relationship with print complexity and quality. The faster the print, the lower the quality. The greater the complexity the lesser the print speed. It is important to select a model that offers a trade-off between speed and quality of print.
Complexity. Complexity of design that can be printed is determined by three factors: slicer software support, support structure generation and print speed. Some applications require composite design features, such as multiple layers and complex curves. So it is necessary to first define the demands of your specific application.
Print platform. The size of the print platform determines the maximum dimensions that can be printed using a particular printer. It is usually measured in inches or centimetres in XYZ dimensions. For electronics designer, 203×203×203mm would be a good start. Print platforms of 229×229×229mm or more are used in industries. If the printing job can be split into smaller parts and combined later, you can go for smaller build area. Larger print area avoids the need for this scaling and slicing of the print.
Resolution. Resolution can be of two types:
Vertical Z resolution/layer height/layer thickness is usually defined by the thickness of each layer the printer can create in one pass. The smaller the layer thickness, the higher the resolution. Small resolution gives smoother and more realistic print outputs, but this also increases the time to produce the final product as the number of layers increase.
On the other hand, larger resolutions provide models with lesser finish in lesser time. Models that let the user choose layer thickness are also available. 0.2mm and 0.3mm are the commonly available resolutions.
Horizontal resolution/XY resolution/feature resolution is the minimum displacement that can be made by a print head in the XY plane. It is measured in micrometres (µm) or dots per inch (dpi). Smaller feature resolution corresponds to finer features in the print.
High resolution or reduced error is particularly important if the casting is printed in parts and assembled separately. Low dimensional accuracy models may lead to misfit of parts whilst they are combined to create the final model.
Printing methods. There are several methods of 3D printing. These can be categorised into six core processes:
Photocuring.
Uses: Concept models, patterns and prototypes
For example: Stereolithography (SLA/SL), digital light processing (DLP), multi-jet modelling (MJM) and polyjet technology
Sintering.
Uses: Functional prototypes, low-volume production of complex components and investment casting
For example: Selective laser sintering (SLS) and direct metal laser sintering (DMLS)
Melting.
Uses: Functional prototypes, low-volume production of complex components and tooling components
Electron beam melting (EBM) and direct metal printing (DMP)
Lamination.
Uses: Wood-like models and concept models
For example: Laminated object manufacturing (LOM)
Extrusion.
Uses: Functional and durable models, production parts and manufacturing tools
For example: Fused deposition modelling (FDM)/fused filament fabrication (FFF), plastic jet printing (PJP) and thermoplastic extrusion
Jetting.
Uses: Large objects, fast and cheap models and smooth models with lots of fine details
For example: Powder bed and inkjet head/3D printing (3dp), MJM, smooth curvature printing (SCP) and DMP
The key advantage of FDM is reusability. Since raw thermoplastic materials are used here, this technology is less susceptible to dimensional changes, unlike other technologies. This technology offers easy material changeover. FDM has fair levels of accuracy which fulfils the needs of a basic perspective making it the most popular in low-end, economical devices. But this method mostly lacks the resolution and finish of a professional-grade output.