If you are a low-volume electronics manufacturer or a hobbyist stepping up from hand assembly, you might be overlooking how efficient you can get in production by continuing to do hand assembly. A lot of people doing just through-hole soldering might be nervous about surface mount. They might also be tweezing their way through work, which is not the most efficient way to do things. There are many things that you can do to get more efficient.
There are different flavours of benchtop or desktop printed circuit board (PCB) assembly solutions available. “Desktop SMT equipment should be compact, yet flexible enough to cover a wide spectrum of today’s manufacturing needs and in the future, too. These should also be easy to use and economical,” says Kumud Tyagi, vice president, Bergen Associates Pvt Ltd.
Pick-and-place
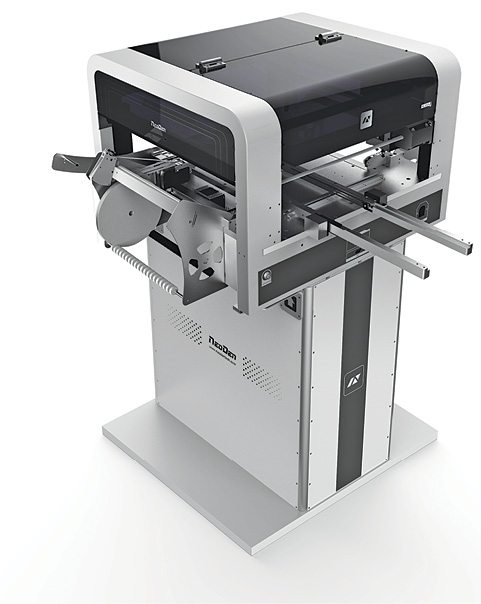
Are you ready to look at pick-and-place (PNP) machines? The most important point to keep in mind is that the least expensive machines will almost always be the most difficult to use. There is a new family of PNP machines coming out of China. A number of different products are being launched by companies who are just copying each other to come out with these machines. They lack important features and also suffer from support and service issues.
Let us take a look at some of the things that you need to consider while shopping for a PNP machine.
Select the right feeders. The components now come on paper or plastic tape. So if you are assembling manually, you would just need to hold on to the tape somehow. In PNP, you might get machines where there is no facility to advance the tape and so you will have to be careful so as not to spill the components all over the workbench. It will be a pain to sort out the small components, especially if these are polarised. The last thing you want is to rework the whole thing. Low-end machines, typically, do not have auto advance, and this means that you would have to babysit the machine while it does its job.
Machine vision. The least expensive PNPs do not have machine vision. Machine vision is a camera and software combo that works to ensure that the part is on the nozzle and aligned correctly before it puts down the component. There are some new machines from China that can be sourced from AliExpress, which do this, or you can work with a local distributor to get one.
We recommend that you go for it if you can afford it. So, what does it do?
1. Verifies that the part is picked up and is on the nozzle. It is easy for the machine to not pick up the part and keep going without picking up a part.
2. Aligns the board. When you start a job and put the board in the machine vision, it will look for marks on the board called fiducial markers. This becomes even more important as the parts become smaller.
3. Helps align the pickup points and identify where the feeders are. Even if you have the mechanical position of the parts correct, you could be off by a millimetre. The problem occurs when the part is just half a millimetre.
Neoden-4 has an intelligent vision system that allows edge detection of every component. It will analyse, add correction, co-ordinate and place accurately using micron high-resolution cameras for analysis and calculation.
Speed of placement per minute. This is important as it decides the productivity that you could get out of your machine. Usually, low-end machines are not going to do more than 10 or 20 pieces per minute. This should not be a problem unless you have a lot of placements to do. For systems with machine vision, switching it off should give you significant increase in the speed of placement since it now does not have to verify the placement of every component.
Other features that can be considered include the smallest size of the part that can be picked. Currently, one of the smallest is 0402 imperial, which translates to 1mm×0.5mm.
Also important is the number of heads that the machine has. Venu Narayan Vaishnav, owner, Chipmax Group, says, “NeoDen-4 can achieve accuracy with 0201 chips and it is a quad-head machine that can carry four component pick-up nozzles at a time.”
Another good example is VisionBot PNP. An interesting machine made by a maker for other makers, it is a comparatively inexpensive tool for PCB assembly that works with gerber and csv files. You can go for 24 to 96 feeders depending on the model, and it is being launched via Kickstarter.
Another interesting one is the PNP machine by ProtoVoltaics, which can speed up the system by using compute unified device architecture (CUDA) accelerated computer vision from an NVIDIA graphics card to speed up the processing of video tasks like rotational vision correction.
The PCBGRIP electronics assembly system being offered is not a complete PNP machine, but holds PCBs, components, stencils and other items so that you can improve the quality and speed of your soldering.
Of stencils and printers
The paste you use along with a stencil is like toothpaste, but it is grey and has to be kept refrigerated in order to last at least six months. If it dries even after being kept in the fridge, you can add alcohol and rejuvenate it. You do not need a lot of it, though. To apply the paste, you need to have a stencil, a piece of material with holes.
Vaishnav adds, “Solder paste comes in different compositions, leaded and without lead to comply with the restriction of hazardous substances (ROHS) directive. There are a few good Chinese brands that are there in the market.”
How do you build stencils? You can laser-cut these stencils pretty easily. Materials can be high-durability or high-temperature plastic. You can also use vellum, which is a translucent paper that you can get at a stationary store. It can be used for about 50 boards and can be easily laser-cut.
How do you select a laser cutter? Laser cutters have a limitation of the smallest hole these can cut. So this may restrict you from using the latest lead-less parts that have a pin pitch of 0.5mm or 0.4mm. If you need to cut a hole of 0.25mm×0.25mm the typical desktop cutters face the limit of their capability here. For steel stencils you need to use ultraviolet lasers that are very expensive. You only find these at big contract manufacturers or you can get a custom stencil by sending your gerber to China from where you will get a steel stencil for about US$ 80. Only do this for super-fine pitch parts with, say, 0.5mm pin pitch.
You may also want to go for steel if you want to do volume as vellum will not stand up to high volumes. You can get a steel stencil framed with an aluminium frame that is designed for mounting into the stencil printer.
You might be able to order a stencil at US$ 80 in China, but to get that to India you will end up paying another US$ 200. Venu suggests you try the many local companies in India that make quality stencils.
When you are dealing with 0.25mm pitch holes, getting the stencil aligned to the board can be tricky business. Stencil printers can be used here. While manual ones are not really useful, automatic ones are very expensive.
Reflow ovens
Reflows are generally categorised in two ways.
Batch reflow. This happens in batches of PCBs.
Continuous reflow. With the help of a conveyor, it moves through the oven, all controlled by PID/PLC control with multi-zones of temperature for better reflow soldering. There are a few Chinese vendors that have very good desktop models of this type.
There are a number of reflow ovens in the market from reputed Chinese suppliers. There are some small reflow ovens that can handle up to 10mm2 and larger ones that can go up to 330mm by 220mm, which is almost as big as an A4-size paper, and that is a good size to work with for office production.
When it comes to reflow ovens, get the biggest one that you can afford. When you get bigger ones, you require good ventilation as these generate fumes and smell.
In the case of smaller desktop ones, you do not need to worry about fumes and smell under normal conditions. But if you are using these throughout the day, then you do need to worry about the fumes.
You are either done or you need to rework
No matter how good a machine is, you always have to inspect what the machine did for you and how the reflow went. Coggeshall says, “The biggest challenge that I have is the paste application and whether the paste is getting on in a uniform manner, or whether you have solder bridges due to too much or too little paste.”
Other cases are where there are big inductors, which could take a long time to heat up due to their thermal mass and the profile of the board. This could cause you to not get complete reflow. So when the boards come out, you need to check these out in a rework station.
Nitish Gupta, business development, Advance Tech Services, says, “Defective surface-mount components can be repaired by using soldering iron or by using a non-contact rework system. In most cases, a rework system is the better choice because SMD work with a soldering iron requires considerable skill and is not always feasible. Temperature accuracy is of utmost concern. RX-802 has a patent six-seconds heat recovery used with a reflow bit for SMT soldering that delivers better and efficient working without shorting and bridging.”
Coggeshall gets a piece of equipment called 898 rework station for about US$ 88 through AliExpress. It is called so because the first Chinese company used that name and now eventually there are a dozen companies using the same name. Coincidentally, the ovens are the same, too. These all look the same on AliExpress or Alibaba. The 898 is a combination of hot air and soldering iron—the hot air is truly indispensible for surface mount rework. There is a set of skills you need to hone if you have to reflow, and you have to use a solder wick to remove solder.
Hot air will usually help you take care of most reflow unless you have something exotic or very small. An exotic component is a lead-less component like the one on Arduino Leonardo quad-flat no-leads where the central processing unit is a small black rectangle. If you have one in hand, look carefully at the perimeter and you will see small dots. That part is impossible to work on without hot air.
There is one more piece of equipment that is basically a bed that heats up—Aoyues66, a toaster oven that sits on your desk and costs approximately US$ 200. When you place your board on the bed, it will heat up the whole board from the bottom. It also has a little arm over the board and a hot-air gun that blows hot air down on the board. These are the last resort if you have rework to do like when you have a ball grid array with pins on the bottom; this may be the only way to get to that part of the board. For light emitting diode arrays that are closely placed, this is the only way to get densely packed parts of the same.
The author is senior editor at EFY. He is B.Tech from University of Calicut, and is currently pursuing MBA from Christ University, Bengaluru. This article was written with major inputs from Bob Coggeshall, who runs Small Batch Assembly, a small, maker-centric business from NoVa Labs in Reston, Virginia, USA