As tech firms keep reducing product development cycles to stay competitive, simulation before going for a prototype is important to save time and improve product reliability – which ultimately results in cost savings. This article looks at the latest in simulation
Dilin Anand
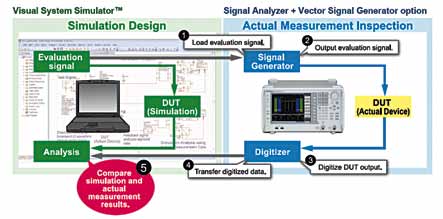
Today, apart from designing innovative and reliable systems, engineers also have to ensure that they do so within a tight budget and a short time-frame. In this cutthroat competition, the primary driver to a successful product is the speed of getting the product to market before competitors. Simulation tools give engineers a very valuable aid—the ability to quickly select the most promising designs before committing to a prototype.
Testing while designing
While it is possible to come up with prototypes and do real-world tests on them, the cost implications are going to be sky-high. Simulation tools give you the ability to simulate your product on the computer and see how it would behave in a real-life situation by allowing you to model different physical characteristics and coupling them simultaneously.
An important factor that has been stressed so many times is to increase the test coverage so that it does not get limited just to test during production but also extends to the design phase.
According to a study conducted by researchers at NASA Johnson Space Center, findinga product defect during production is 21 to 78 times more expensive than during design. Increasing the test coverage during design can bring about a dramatic reduction in the relative cost to repair defects.
Addressing development cycle and cost issues
Traditionally, the product development process in any industry has a cycle of design, detailed design, prototype development, prototype testing and design rectification. This cycle goes on until the desired functionality and performance are achieved.
[stextbox id=”info”]
Being able to reuse simulation models for implementing algorithms by employing automatic code generation technologies enables design teams to leverage the effort invested in creating simulation models, reduces the overall product development time, and saves expensive and lengthy design iterations by mitigating coding and interpretation errors”
— Prashant Rao, technical manager, application engineering & training, MathWorks India
[/stextbox]
“This whole development cycle is very time-consuming and costly, as multiple iterations of physical prototypes are required to arrive at a refine prototype. If you take the case of a pump, our tool helps in simulating the various phenomena that happen inside the pump, such as the centrifugal force, the pressure produced, the flowof the fluidcreated by the pump, the heating up of the motor when in use and the electromagnetic phenomena based on which the motor performs. The combination of electromagnetism, rotation, vibration, thermal variances and other related phenomena can be simulated and this will help you to estimate what the best design should be,” explains Gautam Dutta, country manager, ANSYS.
With the demand for shorter product release cycles, while keeping costs as low as possible, development teams are challenged to bridge the gap between system designers who develop new algorithms and engineers who implement algorithms in software or hardware.
“Embedded software implementations are written in ‘C’ language and executed on digital signal processors or microcontrollers. Hardware implementations are written in hardware description languages (HDLs) such as VHDL or Verilog and programmed onto FPGA or realised on ASICs. Being able to reuse simulation models for implementing algorithms in ‘C’ or HDL languages by employing automatic code generation technologies like Embedded Coder and HDL Coder enables design teams to leverage the effort invested in creating simulation models, reduces the overall product development time, and saves expensive and lengthy design iterations by mitigating coding and interpretation errors,” explains Prashant Rao, technical manager, application engineering & training, MathWorks India.
There are two big advantages to doing a simulation before actually building the design and testing it.
“The biggest of these advantages is money. Designing, building, testing, redesigning, rebuilding and retesting for anything can be an expensive project in itself. Simulations take the building/rebuilding phase out of the loop by using the model already created in the design phase. Most of the time simulation testing is cheaper and faster than performing multiple tests of the design each time,” explains T. Anand, managing director, Knewron.
“The second biggest advantage is the level of detail that you can get from simulation. Simulation can give you results that may not be experimentally measurable with our current level of technology or available instruments in hand. Additionally, you can set the simulation to run for as many time steps as you desire and at any level of detail. The only restrictions are your imagination, programming skills, etc.”