Saber simulation tool for automotive system design is a platform for modelling and simulating physical systems, enabling full-system virtual prototyping for applications in analogue/power electronics, electric power generation/conversion/distribution and mechatronics
Ashwin Gopinath
Decades of industry use and innovation have earned Saber a reputation as one of the most reliable solutions for design validation and optimisation in various domains like automotive, aerospace, industrial power and energy systems. Here we discuss the applications and solutions that Saber brings to design engineers’ tables in automotive domain.
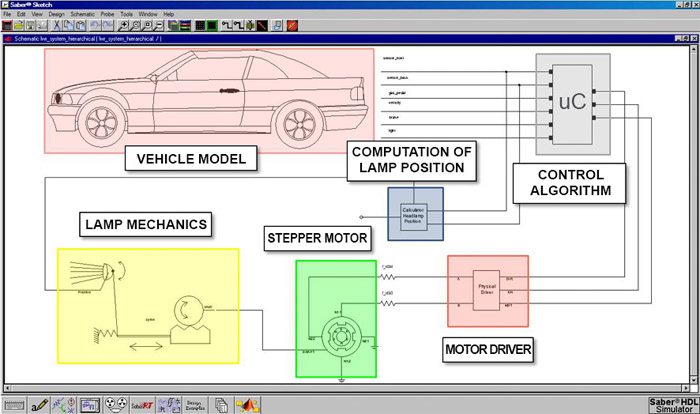
Simulation in automative sector
The economics of automotive industry are becoming more challenging for car makers. Increased pressures for productivity and quality, and proliferation of complex electrical systems are just some of the issues that the industry needs to address. Quality is a significant challenge for automotive industry. The root causes of quality issues are often the designs that do not account for sources of variation, including component tolerance, environmental conditions, component ageing and so on. Statistical analysis using actual parts is economically prohibitive due to the size of systems involved. Compounding the quality challenge is the proliferation of electrical subsystems.
The electrification of vehicles has made them so complex that traditional design approaches don’t achieve performance and design goals. This trend is driving an increase in projects requiring simulation and analysis. On top of these challenges, automotive industry has had to deal with economic pressure in recent years. Reductions in engineering budgets have led to an increase in workload that has to be managed by the same (or sometimes reduced) levels of staffing. Competition from global players has intensified, putting more pressure on development time scales as manufacturers strive to bring their products to market faster.
Robust design methodology
Successful automotive design requires a systematic method to meet rapidly changing and increasingly aggressive performance goals—not to mention compressed schedules. Saber is used to design and verify the interaction of multiple technologies, viz, electrical, mechanical, hydraulic, magnetic and software among numerous others. Designers create virtual prototypes of the system, including the wire harness, to reduce the number of design iterations and hardware prototypes. Far more tests and design variations are possible in this environment than the regular hardware prototyping.
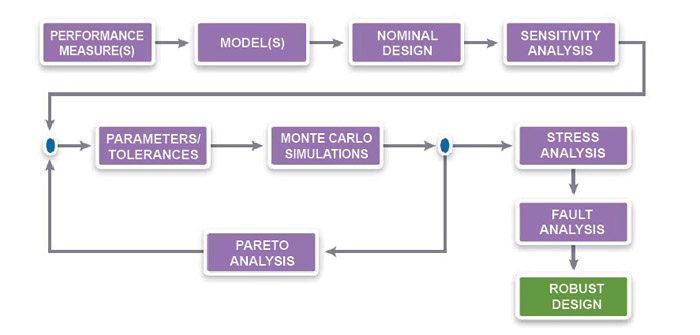
Through a robust design methodology, system performance is immunised against variance in parameters. These methods have proven to reduce design cycle time and maximise performance and reliability. All systems are subject to sources of variation including component tolerances, environmental stresses and ageing. Automotive system engineers want to reduce the effects of variability on system performance by designing systems that are less sensitive to these sources of variation. Saber helps engineers to apply robust design methods, such as Taguchi and Design For Six Sigma (DFSS), and optimise their mechatronic systems for quality and cost.
Saber links to transistor-level CAD (TCAD) tools from Synopsys enable engineering teams to achieve faster product design for power electronics systems. By abstracting the device-level physics to physical systems, designers can work with accurate, compact models of power components. These abstracted models also support behavioural circuit simulation that can be hundreds of thousands of times faster than device-level mixed-mode simulation.
Vehicle power network. As electronic content in vehicles increases, the challenges in meeting this rising energy demand on the power network also rise. Designers must create efficient power generation and distribution systems that perform reliably.
As mentioned before, design teams use robust design methodologies to manage complex energy generation and distribution problems, including an alternator charging system or taking into account system and environmental variations that affect performance. Saber’s comprehensive simulation, modelling resources and analysis capabilities enable design teams to meet the challenges of powernet design.
Advantages for design engineers in vehicle power network. Saber allows design engineers to accurately size system components so as to match the energy generation with corresponding consumption. It eliminates untoward surprises in power network loading and distribution through early detection and verification. “Saber also allows early testing of the complete system with hardware/software co-simulation.” It saves time and eliminates errors with industry-proven power model libraries apart from enabling design portability using industry-standard VHDL-AMS and MAST languages. The Saber platform maximises reliability with advanced sensitivity, statistical performance and fault analyses while increasing analysis throughput with distributed simulations across multiple CPUs.
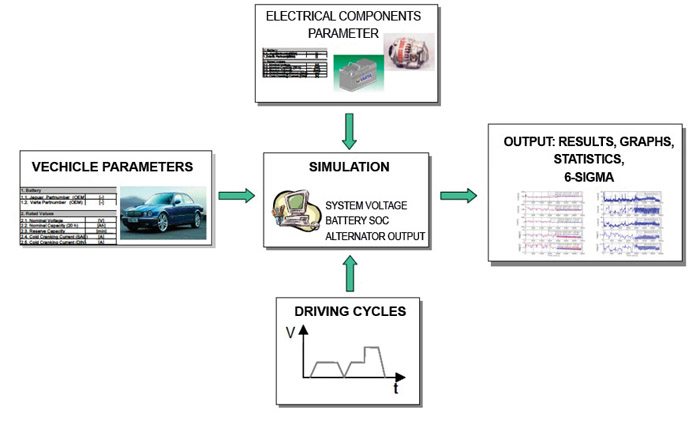
In-vehicle networks (IVNs). Advances in automotive design have been propelled by a dramatic increase in electronics content. Today, a whopping one million lines of code go into a car’s electronics. Numerous electronic systems are required to communicate with each other over a complex network of different communication protocols, such as CAN, LIN and FlexRay. These complexities add significant challenges to physical network layer verification for seamless communication.
With a traditional approach to prototyping, it is nearly impossible to build enough prototypes to adequately test the most important and critical variations of a network design. This is where virtual prototyping comes as the solution for verifying data-network reliability. Saber provides a comprehensive simulation and analysis capability—something which is extremely necessary to apply robust design methodologies to in-vehicle networks and ensure reliability.