RF and microwave tests. The primary requirement for radio frequency and microwave test, apart from accuracy and precision, is wide-band coverage. T&M manufacturers offer highly flexible software along with modular RF hardware to support a wide range of RF test applications that include signal intelligence, record and playback, software-defined radio, multiple-input multiple-output and beam-forming.
Test equipment use some of the latest and high-performance technologies like field-programmable gate arrays for signals intelligence applications. For communications and R&D-grade accuracy, RF equipment are available that provide multichannel synchronisation for up to 4×4 MIMO configurations and a wide range of communication IPs for software-defined radio applications.
High-performance signal analysers provide frequency coverage up to 26.5 GHz and ensure present and future flexibility through optional measurement capabilities. Hardware expandability is another key feature of such equipment. High-speed digitiser modules provide measurement fidelity for high-frequency signals. These also feature large-scale circuit integration, high-speed GS/s sampling rates, wide bandwidth and large acquisition memories.
Surveillance tests. “The growth in types of long-range and short-range wireless technologies poses an escalating challenge for intelligence and homeland security agencies. Whether the mission is to intercept and collect, detect and eradicate, monitor and track, or trend and analyse, there needs to be a thorough familiarity and synergy between the testing systems,” says Awasthi.
“When it comes to security networks, T&M equipment should ensure the transmission quality, for the system to run error-free. These should also check that the network elements are correctly synchronised,” highlights Naresh.
Today’s test systems feature an increased probability of early detection, assessment and response. Military robots and underwater and aerial vehicles can be designed using graphical software environment and embedded hardware platform.
Modularity for flexibility
Advancement in technology has increased device complexity and therefore the complexity of testing and measurement. Modular instruments bring flexibility and scalability to address the complex testing needs.
“Modular instrumentation is a key requirement for most testing environments and the demands placed on aerospace test are no different. Most applications, whether electronic or mechanical, require a mix of different signal types and inputs/outputs. The most effective way to address this is a modular approach. For example, when LXI is utilised as the instrumentation backplane, a tremendous level of flexibility is available to select the right device for the task at hand. This approach limits risks and ensures the best instrumentation solution for the application,” explains Semancik.
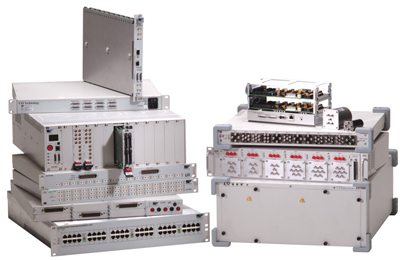
Rajeev Krishnan, strategic sales manager, National Instruments, cites, “The combination of a modular form factor, a high-speed bus and integrated timing features makes PXI ideal for creating modular, software-based systems. With the advent of PXI Express, the PXI platform can provide data streaming up to 1 GB/s. High-speed data streaming represents a revolutionary increase in the functionality of instruments. Furthermore, they can better integrate their tests with real-world signals, acquiring them and then playing back in a controlled environment.”
[stextbox id=”info” caption=”Standards set for aerospace & defence”]
Use of aerospace and defence related T&M equipment is generally governed by the needs of reliability and mission-worthiness. Most of the standards that govern usage of T&M equipment in aerospace and defence are built around ruggedness and reliability of these equipment in extreme war and space conditions. “Aerospace and defence customers look for MIL- or space-qualified equipment,” informs Awasthi. They also have stringent requirements of EMI/EMC compliance.
Most users require equipment that meet certain levels of well-defined safety and performance criteria. Semancik shares, “Instrumentation safety is covered under IEC 61010-1 and electromagnetic radiation is covered under IEC 61326, CISPR 11 and certain FCC sections.”
Sabapathi shares, “Federal aviation authorities decide the avionics instrument standards. Aeronautical Radio, Incorporated (ARINC) standards are for system interfaces in the aviation industry. International Civil Aviation Organization (ICAO) standards decide the operating standards and required parameters to be maintained.”
[/stextbox]
Modular instruments are integrated in a system with timing and synchronisation capabilities through shared clocks and triggers. Some of the synchronisations are better than multiple channels on the same instruments, as in the case of baseband, IF and RF instruments, highest synchronisation accuracy is less than 100 ps. All the modules of the integrated system are connected through a bus, such as GPIB, PXI, VXI or most recently LXI, to the shared processor to perform a task.
The cost of high-accuracy and high-resolution systems is normally high, which is why they are required to last longer. “The aerospace and defence industry uses modules for specific functions. Integrated modular instrumentation provides highly accurate measurements, saves a lot of space and opens a wide range of test and measurement equipment,” says Sabapathi. This makes integrated modular instrumentation suitable for ATEs today and tomorrow.