Oscilloscopes for complex signal analysis. Conventionally, RF equipment are meant to perform analysis in frequency domain. But there has always been a need to capture and analyse signals at these high frequencies in time domain as well. Introduction of 33GHz millimetre-wave oscilloscopes has enabled RF engineers to capture and analyse these signals in time domain. Along with a versatile analysis tool like VSA, these oscilloscopes make the most convenient tools for complex signal analysis.
Advanced vector network analysers (VNAs). As the demand for faster data transfer rates and wider channel capacities continues to rise, precision RF components are essential to provide high-quality signals required from base-band to RF. For their exceptional accuracy and flexibility, VNAs have become an indispensable tool on the design bench as well as in validation test systems on the production line.
Samant underlines the importance of using VNAs: “The unique hardware architecture of VNA allows to precisely characterise the DUT. VNA allows to understand the electrical contribution of each component, whether in the form of an impedance mismatch or non-linear behaviour. This facilitates design of wireless devices that keep pace with today’s demanding standards.”
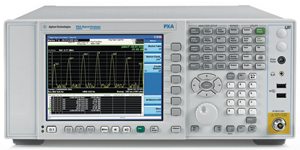
Introduction of 67GHz single-box VNA with inbuilt second source, pulse generators, pulse modulators, combiner and switch has allowed RF designers to test their radar and satellite components, and also extract non-linear models and X-parameters of their devices and circuits right up to 67 GHz.
“Along with millimetre-wave test heads, it provides the most sophisticated single-sweep, single-connection, multiple-measurement platform up to 110 GHz and in bands up to 2.0 terahertz,” informs Vishal.
Equipment for hardware-in-loop testing. Hardware-in-loop testing of RF sub-systems like telemetry links, radars and software-defined radio systems requires real-time processing of high-bandwidth RF data. One of the major challenges so far had been the backplane throughput, which did not allow streaming of RF data from input/output (I/O) modules to processors at a fast enough rate.
“With PXIe platform, T&M systems have evolved to meet these requirements of in-line signal processing on the acquired data. For example, PXIe backplane offers peer-to-peer streaming capabilities through which high-frequency and high-bandwidth data can be routed to FPGA processors at extremely fast rates, where it can be processed and measured in real-time,” says Tarun.
Test equipment that ensure shorter design cycle. The most critical test challenges before RF design engineers are reducing the design cycle and coming up with an accurate design. Further, RF design engineers want a single and more robust test platform to test multiple parameters of their device with a single connection.
“New equipment like non-linear vector network analysers (NVNAs) and the latest VNAs provide such capabilities where the non-linear behaviour of a device could be modelled more accurately and incorporated in the design to bring down its design cycle drastically. The latest-generation VNA—similar to Agilent’s PNA-X, provides a platform to perform complete characterisation of an active device based on single-connection multiple measurements,” says Vishal.
Equipment for multiple-channel signal analysis. New modular equipment can perform signal analysis for up to six channels.
“T&M industry has experienced the need for multiple-channel RF testing, especially for software-defined radios (SDRs) and wireless standards with MIMO. This has given rise to a new trend of modular test equipment in the RF domain,” says Vishal.
Equipment for custom measurements. As the devices become more complex, there is a need for custom measurements and therefore more flexibility in the instruments to program these custom measurements.
Samanta explains, “In most traditional instruments, measurements are defined by the vendors. Engineers want the flexibility of acquiring raw data and making custom measurements on it. In addition, they like to use an instrument that can be used by their verification and validation engineers as well.”
“The modular software-defined architecture of PXI test equipment makes it a compelling alternative to traditional instrumentation for testing emerging standards and devices with increased complexity,” he adds.
Traditional instruments typically have a fixed software architecture with most of the functionality defined inside the box along with their own mechanical enclosure, processor, power supply and display. On the other hand, software-defined instruments share the processor, chassis, power supply, and display across all instruments in a single PXI chassis. The test software resides on the host PC, allowing user-defined measurements and analysis in real time—a test setup optimised for high-throughput parallel testing.
Equipment to enable quick prototyping. Another challenge faced by the design engineers at various stages of design is the need for quick prototyping. Tarun explains, “It is not always possible to have ‘golden’ boards or sub-systems that can be used to validate a newly developed sub-system. Thus arises the need for a platform which enables users to prototype the various sub-systems and test the development done by the user quickly.”