Ever wondered how your mobile vibrates? Let us see. There is a small motor in your phone, which is responsible for shaking it every time you receive a notification. I observed this phenomenon in a Motorola phone by removing the back cover and calling that number. Interestingly, there is a half-cut cylinder (cut along its axis) attached to the motor’s axle that rotates very fast to generate the vibration.
Motion is the main motive behind using motors. In embedded systems an area that has seen extensive use of motors is robots. If you go through the schematics of a humanoid robot, you will probably forget the motor count by the time you are through with the review. Every joint is essentially a motor, with some having more than one.
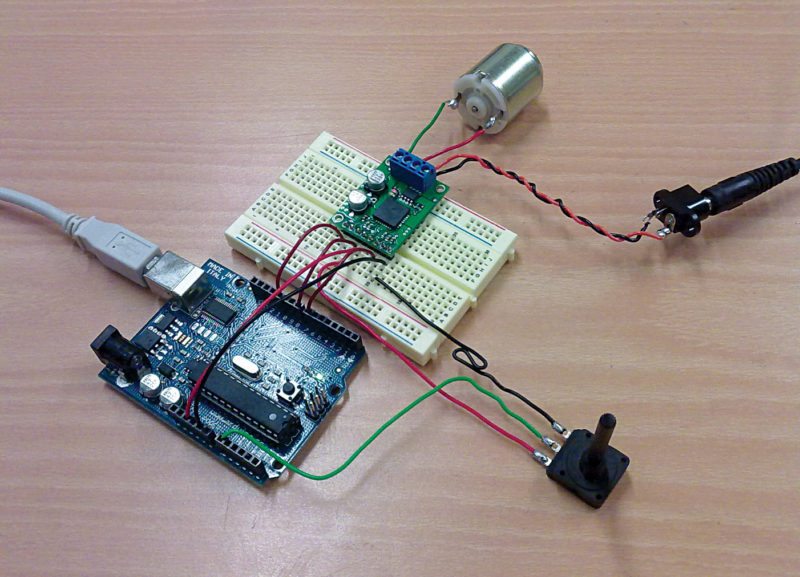
Types and advances
Let us take the example of the humanoid robot. We would require a multitude of motors for different use cases. For instance, a type of motor would be used for lifting heavy parts of a machine, whereas another for controlled motions of its individual parts. These would then, in turn, require similarly different drivers for their application.
A trend that is catching up in system design using motors is employment of direct current (DC) motors. “Ranging from automotives and fans to wearables, we are seeing an increase of brushless DC (BLDC) motors,” says Hrishikesh Kamat, chief executive officer, Shalaka Technologies.
With their increased employment in embedded system designs, the size of motors has become smaller than ever through continuous iterations and technology advances. Motors and their drivers are moving towards smaller, smarter, safer and faster solutions. “Drivers are coming inbuilt with Hall sensor inputs and back electromagnetic force sensing capability,” says T. Anand, managing director, Knewron Technologies. He adds, “This allows designers to reduce part counts and, thus, BOM costs.”
Drivers can also be integrated with radio frequency chipsets for remote control in home automation and industrial applications, enabling remote diagnostics of motor drives as well.
Sensor-less control
Kamat says, “Implementation of sensor-less control of BLDC motors is seen in many of the recent applications. Elimination of rotor positioning sensors like Hall sensors not only reduces cost but also increases reliability.” Sensor-less drive is based on detection of back electromagnetic force induced by the movement of a permanent magnet rotor in front of stator winding.
InstaSPIN is another technology that monitors the motor’s flux to determine when to commutate the motor.
To implement features like sensor-less control, automatic and integrated-state machine logic to control the motor, “it requires highly smart algorithms to control the system,” says Anatya Vallabh, technical sales engineer, Texas Instruments (India) Pvt Ltd. He adds, “These should follow the theoretical mechanism to spin the motor.” Besides, it should take care of practical faults that might rise during operation.
Vallabh explains, “For example, the motivation behind sensor-less control is applicability with end usage.” Naveen Bevara, analogue applications engineer, Texas Instruments (India) Pvt Ltd, adds, “Motors typically include what is called a position sensor, which can identify the position of the rotor (moving part of a motor). Identifying rotor position is essential for control of the motor at various speeds and under changing loads.”
Reliability in speed control
One of the innovative uses of motors in applications today (such as air-conditioners, refrigerator compressors, washing machines and cooling fans) is to drive and control a motor at variable speeds and even turn it off at times to improve product efficiency. The motor must be able to then re-start quickly and reliably 100 per cent of the time. This has allowed manufacturers to improve reliability of their products, improve efficiency by using variable-speed motor technology and eliminate costly position sensors from their systems.
Automatic tuning
Running the driver in stepper motor application requires tuning. If manual tuning is used, it is very difficult to find the accurate point to set while tuning. Auto-tuning is an intelligent system, which seeks optimum parameters of the motor. Auto-tuning suppresses oscillations, making frictional compensation. It does not require any input from you. The motor will perform a sequence of movements in order to determine the type of load that is controlled and the type of coupling. This tuning covers most applications with good performance.
STSPIN motor drivers from STMicroelectronics can be used in a wide range of applications including robotic positioning systems, printer motors, camera autofocus mechanisms, toothbrush motors or syringe pumps other than the intended purpose of portable and wearable design. Sized at 3mm×3mm, these are being dubbed as the smallest in size.
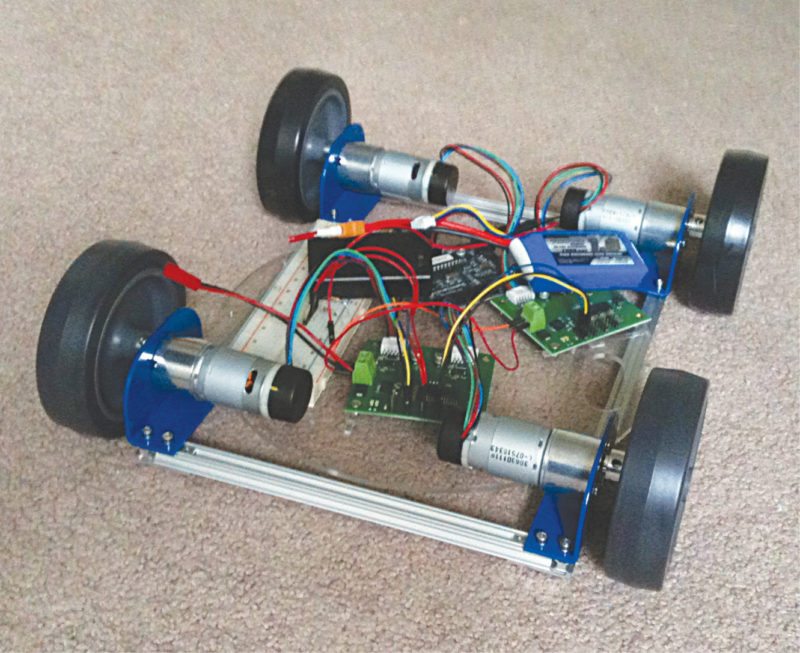
Power applications
Improved power efficiency is always the guiding factor for technology trends. Bevara explains, “When it comes to power applications, higher power efficiency is always the guiding factor for new technology.” Power of electric motors can range anywhere from milli-watts to mega-watts. “Intelligent performance and improved efficiency of both motor and driver circuitry are the areas of design focus,” he adds.
When it comes to electronics driving the motor, innovation in the fields of topology, power devices and integration are defining the roadmap. Anand adds, “One of the critical elements for these systems is power sources with the capability to deliver higher current in peaks.”
Integrated solutions
Solutions that consume lower power (around/less than 50W) are now available with integrated power devices and state machine to control. For example, DRV10983, a three-phase sensor-less motor controller with integrated power MOSFETs, can provide continuous drive current up to 2A.
With integrated-state machine, driver and power MOSFETs, it uses a proprietary sensor-less control scheme to provide continuous sinusoidal drive, which reduces pure-tone acoustics that typically occur as a result of commutation. Interface to the device is designed to be simple and flexible. EEPROM is integrated in DRV10983 as memory for the motor parameter and operation settings.
DRV10970 is an integrated three-phase BLDC motor driver for home appliances, cooling fans and other general-purpose motor-control applications. Embedded intelligence, small form factor and simple pin-out structure help with design complexity, board space and system cost. Integrated protections can keep a watchful eye on system robustness and reliability.
TC78S122FNG is a low-power-consuming module with up to four channels for motor with DC brush. Application areas include surveillance cameras, banking terminals, video slot machines and home appliances like refrigerators and air-conditioners. Currently available in DIP package, Toshiba also plans to bring out a quad-flat package very soon.
Features to look forward to
Kilby Labs engineers have developed and patented a sensor-less control algorithm that turns power electronics into smart gate drivers and eliminates the need for a position sensor. The end result is a more reliable motor system that will start a motor every time under full-load conditions. The system also continues to drive and control the motor as load and speed performance change, as required by the application.
Kamat says, “We now have a very wide variety to select from.” As we move ahead, improving efficiency will always be the focus. Anand adds, “Minimising power losses is a key objective of designs.” Gallium-nitride, silicon-carbide and other such newer semiconductor materials might enable in reaching higher efficiencies.
Total harmonic distortion is another concern in motor-driving applications. Currently-used passive filtering mitigates this to some effect, but since it is bulky, it can introduce load based resonance. Combining active and passive methods (hybrid) or pure active methods could, however, be feasible solutions to increase system performance. These technologies are being researched at some research and development centres.
Saurabh Durgapal is working as technology journalist at EFY