This article aims to make design challenges for LED streetlights easier with the help of an example.
In many consumer lighting applications, the cost of existing technology—especially light bulbs or fluorescent lamps—is so low that many of the benefits of LED lighting cannot offset the increase in start-up costs. Street lighting differs significantly because the long life and high degree of control provided by semiconductor lighting is associated with the end user—the government—who evaluates the cost of ownership along with the initial cost.
This is where high-quality LEDs paired with good thermal management and robust drive electronics have real value. This article proposes an electric drive solution that balances higher initial costs with long life—at least as long as of the LEDs’ themselves.
DC bus voltages
A hundred or more one-watt LEDs are often enough to produce thousands of lumens needed for a streetlamp. One way to power 100 LEDs would be to string them in one series. This ensures the same current through each LED and, since the light output is proportional to the current, it is the best way to guarantee the same light output from each device.
The problem is that a DC voltage can easily be 400V. Such a voltage can be lethal and also requires large and expensive components.
The second way to arrange 100 LEDs would be to use more parallel strings with lower DC voltage. Known and cost-effective topologies, such as a reverse converter, produce good AC-DC stages (often called offline converters) because they can combine a step-down function with galvanic isolation and power factor correction (PFC).
DC bus voltages of 60V or less are common due to the 48V used in telecommunication applications and due to safety regulations, such as the IEC definition of safe low voltage. Because it is not as low as the logic voltage of digital circuits, and yet is not as high as the rectified offline voltage, the 48V distribution voltage is often called the medium DC bus voltage.
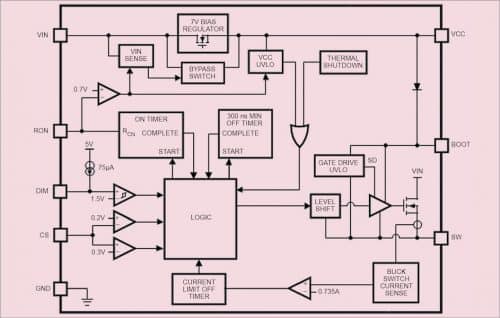
Circuit topologies
The DC-DC converter is a natural choice for the last stage in the LED power supply. The LED requires direct current, so the output is also direct current.
The concept of an intermediate DC bus allows the designer to use cost-effective, non-isolated DC-DC converters, as the previous stage takes care of repair, PFC, and isolation.
There are three main types of non-isolated converters:
- Buck
- Boost
- Buck-Boost
Of these topologies, the buck controller is by far the most suitable for LED control for several reasons.
First, the buck inductor is at the output, which means that the LED current and the inductor current have the same average value. Further, the output current is always explicitly controlled thanks to the inductor.
Second, voltage reduction is the most efficient form of power conversion, making the buck the most efficient of all switching converters.
Third, the buck is most economical among switching converters because the heaviest currents are at the output and the low voltage is at the input.
It places the lowest voltage and current on power MOSFETs and diodes, which form power switches in switching converters. This means a wide selection of power switches, passive components, and control integrated circuits—all of which represent the most economical solution.
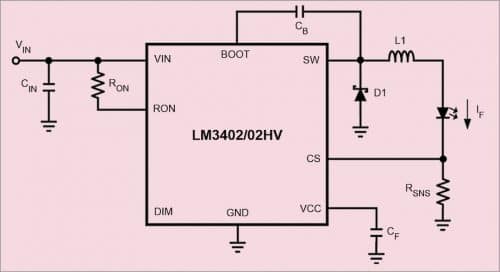
LED layout and IC driver selection
For this design example, 100 LEDs will be used, each scattering one watt. A 48V intermediate DC bus is a good choice, as standard AC-DC power supplies with a wide selection of output power are available.
From 48V ±5% it is possible to use the buck LED driver to supply ten LEDs in series. Ten such controllers produce a robust light bulb that can be designed to operate using all 100 LEDs without a dangerous voltage.
Optoconductor manufacturers combine their white LEDs for luminous flux, correlated colour temperature (CCT), and forward voltage. Binning for temperature and colour flux is important to maintain consistent colour and light output, but the more quality LEDs are combined, the higher the cost.
If LEDs with different sockets are used, the designs of the LED bulbs must be adapted to a wide range of forward voltages. Therefore each LED driver will be a 350mA current source that is designed to operate from a 45V to 51V input in the output voltage range of 30V to 40V, reflecting the potential VF changes of each LED from 3.0V to 4.0V.
The LM3402HV is an example of a buck controller with an internal power N-mosfet.
Design challenges with buck regulators
When using a cell controller to power an LED, the main design challenge occurs when the input voltage is at a minimum and the output voltage is at a maximum.
Many switching regulators cannot turn on the internal N-MOSFET indefinitely. During each switching period, the controller must be turned off for a minimum shutdown time of 300ns to restore the bootstrap capacitor, which is part of the circuit that drives the internal power FET.
Because the minimum switch-off time is fixed, the maximum duty cycle that can be achieved decreases with increasing switching frequency. This is because those 300ns consume more and more of the switching cycle.
Typical switching frequencies range from 50kHz to 1MHz, and 500kHz is often a good balance between the physical size of power components such as an inductor, which is smaller when the switching frequency is higher, and energy efficiency, which is higher when the switching frequency is lower.
In this case, 500kHz is not possible, so 370kHz is used. This ensures that the LED driver has the smallest possible components and, at the same time, can properly control all ten LEDs during the worst input and output voltage conditions.
Jawaaz Ahmad, from Srinagar, is a Design Fellow at Design Innovation Centre in Islamic University of Science and Technology, J&K. He did B.Tech in Electronics and Communication from the same University, and M. Tech in VLSI Design and Embedded Systems from Visvesvaraya Technological University