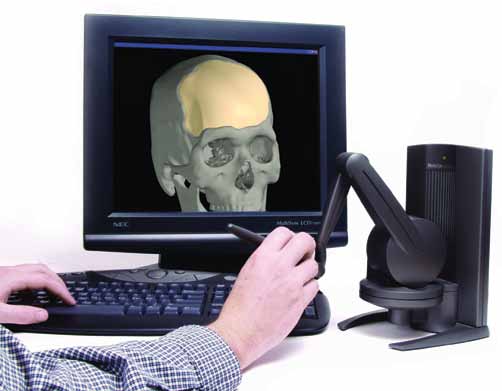
Fundamentally, haptics is any form of non-verbal communication involving touch. Shaking hands when you greet someone is a haptic custom originated from western countries. What we are going to discuss here is the technological aspect of using haptics. When you receive a call on your mobile phone while it is in silent mode, and feel that gentle buzzing in your pocket, that is haptic technology at work.
How does it work?
Haptic technology utilises haptic perception, which is the ability to recognise objects by touch. While tra-ditionally the object that was referred to was a physical object, modern-day implementations include the ability to recognise virtual objects such as those that exist in a world connected by the Internet of Things.
Haptics uses tactile feedback, executed by applying force or motion on the body of a person, in the form of vibrations or other similarly identifable effects. The human somatosensory system is an impressively complex sensory system which comprises sensors that allow our body to feel touch, temperature, pain and movement. These sensors detect the force applied by the actuators in a haptics system and allow the user to have an additional level of interaction with the device that he is working with.
Overall, it could be said that haptics allows a person to feel input from the device, other than the conventional methods of either seeing or hearing it. Thus, it adds further depth to the level of interaction between humans and machines.
Why integrate haptics in your project?
Haptic technology works by using different kinds of actuators to create vibrations and movements that are perceived as tactile feedback by the user. These haptic effects are enabled by the actuators that apply force on the skin so that the user can feel the force. A variety of actuators are available these days for use by a designer.
“Many technology companies such as Immersion, Texas Instruments (TI), Senseg and AAC Technologies have come up with a set of development tools to work with haptics—to design, develop and test haptics-based applications. As the technology is in a fairly nascent stage, not many players have resources available for learning in the field,”explains Anand Tamboli, managing director, Knewron.
Eccentric rotating mass motors
The most commonly used (and the least expensive) form of actuators use electromagnetic technologies to form eccentric rotating mass (ERM) motors, which are off-centre weighted motors that apply very strong force. While the force that we can leverage from this device is impressive, you will not be able to use it for applying subtler effects. This actuator would be suitable when the device only needs to alert a user urgently when a certain event occurs. ERM motor also suffers from lower response times as it takes a little extra time for the vibration to begin or end.
Linear resonant actuators
The latest smartphones use linear resonant actuators (LRAs) that are capable of providing a more precise and softer vibration that does not feel jarring in your pants. In an LRA, you will finda magnet attached to a spring which is surrounded by a coil. As the magnet is controlled, it oscillates linearly until the frequency reaches the resonant frequency of that component. Frequencies on either side of the resonant frequencies can also be used at the loss of performance. On the brighter side, the LRA is more power-efficientthan the ERM motor. However, it also has a weakness—linear vibrators are much larger than rotational vibrators.
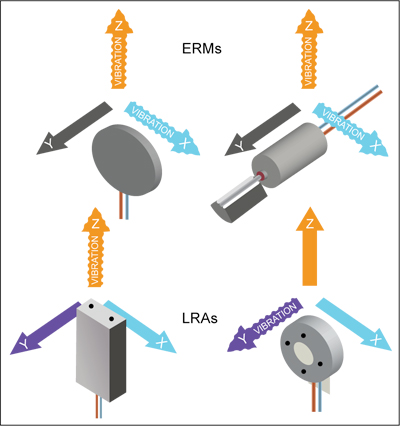
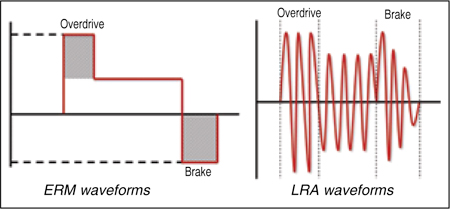
Piezoelectric actuators
Piezoelectric actuators, or piezos as they are lovingly called, are yet another technology that allows very power-efficien vibrations. Most of you must be familiar with the piezoelectric buzzer used in electronics projects. Well, this is almost the same thing. While piezoelectric actuators allow a far wider range of frequencies to be put on the device, these also require a far higher voltage than an ERM or LRA.
The DRV8662 is a single-chip piezo haptic driver from TI that solves the high voltage requirements of piezos by including an integrated on-chip boost converter which can boost up to 105 V.
[stextbox id=”info” caption=”Components of haptic devices”]PicoVibe 304-002. A small eccentric rotating mass motor from Precision Microdrives based on neodymium (an exotic metal) magnets for improved performance. Its size is mere 4 mm.
Fairchild Semiconductor’s FAH4830. A haptic driver that supports both ERM motors and LRA and features very low wake-up time of 30 μs.
Texas Instruments’ DRV8601. A haptic driver that supports both ERM motors and LRA. It is a low-power-consumption model that consumes just 10 nA of shutdown current.
Texas Instruments’ DRV8662. A haptic driver that supports piezo actuators and has an integrated voltage boost converter to account for the high voltages required of piezoelectric actuators.
PrecisionVibe C10-100. An LRA-based actuator with 1.4G amplitude. It is based on a brushless design that gives it an enhanced working life due to the reduction of mechanical components compared to the ERM-based motors.[/stextbox]