While going through electronics product reviews, you might have come across phrases like, “The phone heats up on intensive gaming” or “The device feels warm after constant use.” According to Ramanan, vice president – engineering, defence solutions, Mistral Solutions, “Due to this inefficiency of electronic devices, a vast portion of electrical energy is converted to heat, calling for a heat sink and other solutions being put in place.”
Electronic devices exhibit high heat dissipation levels over a very small surface area. The heat thus dissipated by electronic devices in a product, if not managed or removed, may lead to the malfunction of the device, deteriorate the product performance, and may also be hazardous to the environment and users of such products. It is therefore essential to implement efficient thermal management techniques at the product level. Thermal management designs for the envelope the product has to function within can be arrived at by carrying simulations and analysis which yields the exact information of the thermal behavior of devices and the product as a whole. The findings from such analysis is applied to arrive at the appropriate and optimal design of the product.
Thermal solutions come in handy while thinking of a way to solve this problem. Heat dissipation needs of today’s components are more challenging than ever. System airflow and its impact on heat sink design is a very important factor in applications generating sufficient heat. “Telecom, automobiles and lighting are some applications that require major use of thermal solutions,” says Dr Misra, director – research and development, Henkel Adhesive Technologies.
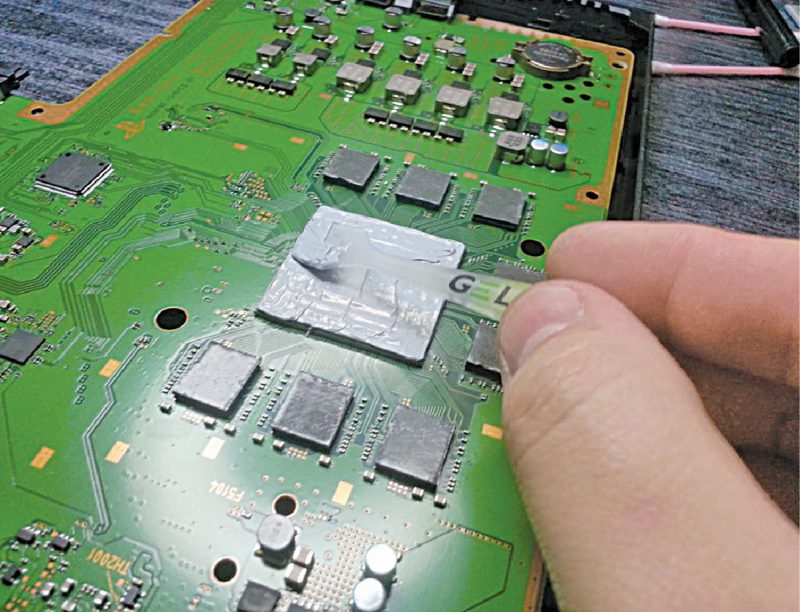
Consider an efficient heat sink
Ongoing increase in power usage among devices such as processors and insulated-gate bipolar transistors results in higher capacity cooling requirements to remove excess heat. To cool hotter components, you may use large fans, heat sink and increase surface area. Using higher-performance interface material between the case and the heat sink also improves cooling performance
Heat transfer occurs when two surfaces have different temperatures, thus causing heat energy to transfer from the hotter surface to the colder one. Some tips from industry experts in the box titled ‘Application tips for heat sink design,’ should be helpful in designing one.
The latest in heat removal
“A clear understanding of the amount of heat generated and the rate of generation are essential to arrive at the size and design of the heat sink,” says Ramanan. “The choice of thermally conductive pads as a shunt between heat sink and the devices is also determined by these two factors,” he adds. On a more general note, radial and grid patterns (pin fin) are being used by designers today for better heat dissipation. Radial fins provide ease in design, while grid patterns allow for a much higher surface area to aid heat loss.
As for the material, aluminium alloys have been the material of choice for the past decade for efficient cooling. Aluminium also remains popular for its conductivity, light weight and low cost, relative to other metals such as copper. To create more complex designs, manufacturers have also employed high-quality alloys like forged aluminium.
Ceramics, thermally-conductive plastics and graphite are also being experimented with. Inorganic ceramics, non-metallic and non-corrosive materials are already being used in LEDs. Heat conduction and electric insulation make these ideal for heat sink applications.
Thermally-conductive plastics, or thermoplastics that are loaded with a conductive material, such as aluminium nitride are naturally non-corrosive, making these ideal for outdoor applications. Thermoplastics are also 20 to 30 per cent less expensive than aluminium as these are simpler to make.
Italian luminaire manufacturer, Reggiani Lighting, combines copper and extruded aluminium to reap the best of both metals in LEDs. These materials are undergoing a lot of experiments. Made from graphite, hitherm is a lightweight flexible material. Carbon being an excellent conductor of heat, it enables this material to be a very good heat sink. However, price point of these solutions is relatively high.
Liquid cooling solutions
There might come a time while designing a system when a simple fan or heat sink is not enough. Ramanan explains, “If the quantum and rate of heat dissipation is very high, we may need to opt for methods which would involve liquids as the medium for the transfer of heat.” This calls for solutions that can manage a higher rate of heat transfer.
One solution is to allow a coolant to flow in between the plates of the heat sink. This coolant would absorb heat from the heat sink and allow for a more maintained environment of operation. A common coolant in such a solution is distilled water mixed with ethylene glycol. “Proportion of these two could be determined by the temperature envelope under which the product would have to function,” explains Ramanan.
Interface materials are too often forgotten
Thermal interface materials applied between the conductive layer and the heat sink to facilitate heat transfer are too often forgotten. For efficient transfer of heat from the circuit to the sink, a proper interface becomes necessary. “The heat sink in most cases will be rigid, hence reducing the contact area, resulting in a lower level of heat transfer,” says Padmanabha Shakthivelu, general manager, Electrolube India. As a result, thermal interfaces become integral to a system.
Depending on the material, this layer can cause significant difference in the effectiveness of the heat sink. Thermal solutions are also available in the form of adhesives, greases, gels, pads or solder alloys. Dr Misra says, “Low hardness and high conductivity are the necessary requirements for interface materials.”
Some solutions are solid
Flexible solid interface materials consisting of silicon in ceramic are in high demand. However, a lot of forums raise the question of local vendors preferring one over the other, depending on the area of usage. Thermal pads and thermal compounds are used to fill air gaps caused by imperfectly flat or smooth surfaces, which should be in thermal contact. Thermal pads are solid, rubber-like materials, often based on silicone compounds or paraffin wax. These are relatively firm at room temperature, but become soft and are well able to fill gaps at higher temperatures.
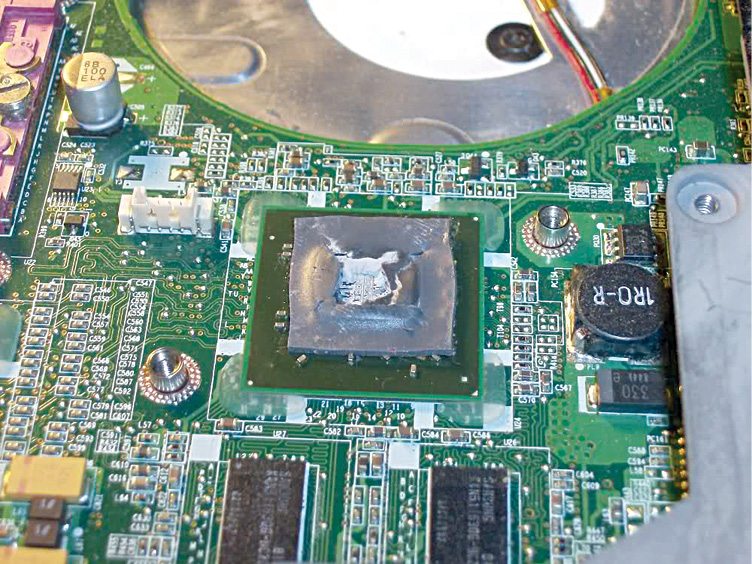
Average usage lifetime for a solution usually goes from one to three years. However, with thermal pastes, this can be more towards the lower end of the spectrum, due to their tendency to dry out. There is always a risk of thermal grease dispersing over time, leaving no interface material between the heat source and the sink.
Others are liquid
The liquid approach offers infinite thickness variations with little to no stress to sensitive components during assembly. Gap-filler 3500LV from Henkel is a two-part, high thermal conductivity, liquid gap-filling material. Made of polymer and thermally-conductive elements, it offers mechanical property benefits of a silicone material with low outgassing.
ER2224 epoxy resin from Electrolube caters to a wide range of automotive applications. These generally require high thermal conductivity and good thermal cycling performance.
Shakthivelu explains the design of grease solutions for heat management. “We have a range of grease, for example, one-watt, three-watt or five-watt grease”. These are designed for perfect balance between spread and conductivity. He adds, “We have small metal conductors inside the paste, which transfer the heat. Sizes of these conductors change with the amount and rate of transfer of heat.”
Where does this trend take devices
The role of thermal compound is simple—to fill the tiny gaps between the cooler and the integrated heat spreader, and to promote thermal conductivity. Some reports suggest that, introducing active cooling systems reduces the size of heat sinks by 90 per cent. Now, if you could design a system with a smaller size, that would be a dream for designers.
Manufacturers are sceptical, however, about the reliability of fans and the noise these could create. Misra says, “Heat absorbers is an area that shows promise.” Introduction of new materials and form factors has been a very welcome change in designing heat dissipation solutions. These improvements should lead to things that have never before been possible.
Saurabh Durgapal is working as technology journalist at EFY