[stextbox id=”info”]“System-on-module is an extension of the concept of system-on-chip which lies between a full-up computer and a microcontroller in nature” ——Texas Instruments[/stextbox]
[stextbox id=”info”]“We wanted to assist product designers in developing products with reduced time, effort and cost, to foster innovation. This was our aim when we conceptualised the SoM based on TI’s DaVinci DM816x and DM814x video processors,” says Dhaval Parikh, hardware division head at eInfochips.[/stextbox]
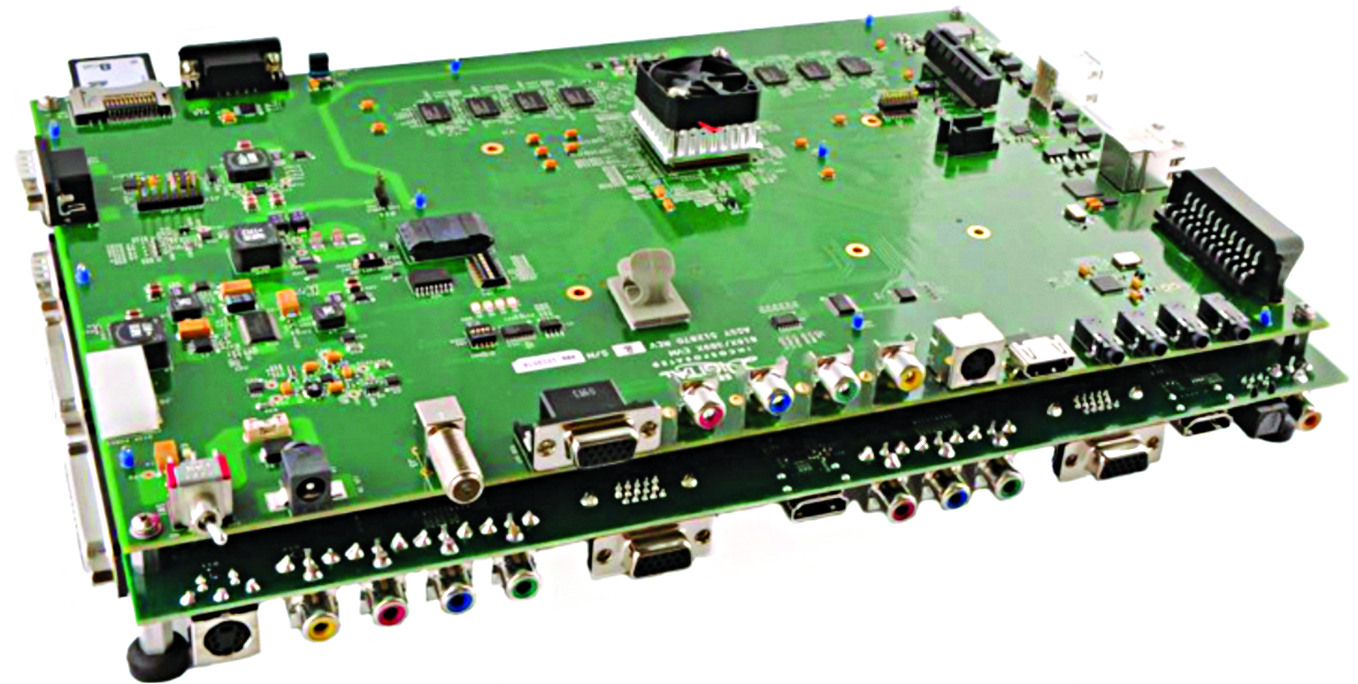
But what exactly is an SoM? A system-on-module (SoM), also known as computer-on-module (CoM), is a complete embedded computer system built on a single circuit board. It includes the microprocessor, input/output (I/O) peripherals, memory, power management system and other components on the same chip.
How is a SoM different from a SoC?
SoM is the combination of a system-on-chip (SoC) with memory (DDR2, DDR3 or Flash), power management and other components embedded into one module. Moreover, SoMs do not need processor ‘wake up’ as in SoCs. ‘Wake up’ is the process of getting a shut-down or sleeping CPU back to work and fully operational.
Since the SoM usually lacks standard connectors for I/O peripherals on the board, it is mounted on a carrier board or baseboard. The baseboard has standard peripheral connectors for Ethernet, USB, etc. The wiring of these connectors from the baseboard to the SoM is done via buses. By separating the design of the SoM and baseboard, modular design concepts can be implemented in the system.
In contrast, SoCs are typically I/O-specific devices. So SoCs from even the same manufacturer may not be interchangeable.
Why modular?
Debugging complicated silicon hardware and related hardware for a special application usually requires a high design overhead. By using a module-based approach, it is much easier to upgrade a CPU component. You need to change only the module to be upgraded, leaving the baseboard essentially intact. This reduces the overhead incurred during development and allows designers to spend more time on applications that are key to product success. This leads to reduced business risk and a lower design overhead. Also, one has multiple CPU choices with a modular approach. The best part is hardware and software can be developed in parallel as developers can use off-the-shelf hardware with the same processor core as their product.
Another important point is that the modular approach reduces the risk of having an end-of-life product due to memory, chipset or CPU going kaput. With the capability to swap in another CPU SoM board, the system can be kept running with minimal changes to the baseboard. This also allows the user to enjoy scalability with multiple-speed cores for similar products, which, in turn, allows high-volume pricing to bring down the cost. A lot of applications in the embedded space are shipped in relatively low volumes, which work very well with the concept of a plug-in CoM.
Lower time to market
The SoM approach allows the fastest time to market. Utilising off-the-shelf standard components like a baseboard and SoM, designers are able to start developing applications even before the custom baseboard is complete. As mentioned earlier, this allows software development and hardware development to proceed simultaneously, greatly reducing the time to get the product to the market.
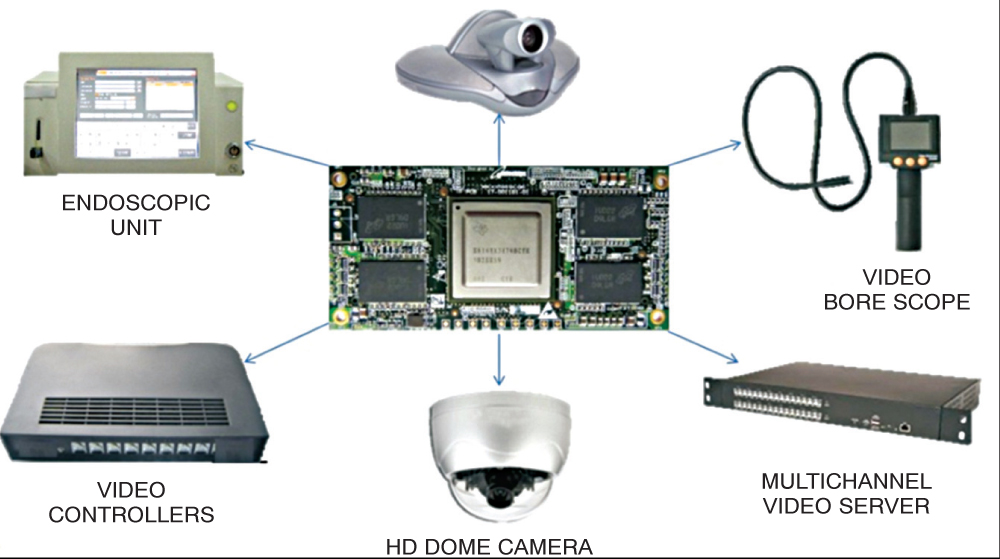
Working with an SoM
An SoM designer needs to be an expert in different aspects of product design in order to conceptualise and evaluate ideas, and make them tangible through products. For designing and supporting a high-quality SoM, he needs to have:
- Deep knowledge of SoC, memory, power management, etc.
- Knowledge of software infrastructure and firmware
- Understanding of system design to define correct SoM and connectivity, for development of different products.
Fitting a processor, memory, flash and interfaces within a small space as in a typical chip, requires careful layout with respect to environmental conditions such as temperature. Simulations are followed by extensive validation testing to ensure that the SoM solution, including a heat-sink, meets its specifications. In addition, rigorous testing is done to ensure that the clock, power, reset and memory signals have sufficient margin to guarantee consistent operation over the lifetime of the product.
As SoM-based designs are similar to microcontroller-based board designs, it will be easier for microcontroller-based systems to transit to SoMs.
What next?
The semiconductor industry is witnessing blazingly fast changes. Different companies use different strategies to improve their portfolio.
“Current SoM-based design requires the use of connectors. To reduce BOM cost, we are working on connector-less SoMs that can be directly soldered onto customer boards. This will make SoMs usable for very high-volume applications too. We are also working on bringing in high-performance microprocessor based SoMs to India. One example is OMAP4460/70, which is a dual-core Cortex A9 based processor,” says Jithu Niruthambath, joint director at Calixto Systems.