It is absolutely necessary to ensure that the leads of components are free from grease, oxidation and other contamination. The oxide layer repels molten solder. It is very difficult to solder old components or tracks on the PCB because of the layer of oxidation that builds up on the surface of the component leads. Even surfaces that look clean may have a thin, invisible film of oxide on them. So for appropriate solder bonding, surfaces must be cleaned using flux.
It is important that the surfaces to be soldered together are brought to the same temperature. When both are heated at a high temperature, solder flows evenly to make a good mechanical and electrical joint.
The parts to be joined should be heated with a soldering bit for the right time length. Excessive heating may damage the components or the printed circuit track. The heating period depends on the size of the joint and the temperature of the soldering bit. Semiconductor components such as diodes, transistors and ICs are sensitive to heat and should not be overheated.
Soldering: the process
When the soldering iron bit is adequately hot, apply a little solder on the flattened tip and wipe it off with a piece of damp cloth or sponge. The solder will form a thin layer on the bit. This process is known as ‘tinning’ the bit.
Heat up the joint with the bit and continue heating while applying solder. The molten solder flows quickly from the bit onto both parts to be joined. It is important to use the right amount of solder. Remove the iron and allow the joint to cool. During the cooling period, if the joint is disturbed, it may become dry and create serious problems in the working of the circuit. Sometimes it becomes very difficult to trace out this defect.
Post-solder flux cleaning
After the soldering process is complete, remove the residual flux from the PCB. Clean it by dissolving it in a solvent and wiping the area dry with a tissue paper. The complete assembly should be totally free from flux and residual cleaning agents. The cleaning method and solvent solution used should not have any adverse effect on the components and the connections.
Wetting action
While soldering, if molten solder comes into contact with a copper surface, the solder dissolves and penetrates the copper surface. Solder and copper form a new alloy. This solvent action is called ‘wetting’ and forms an inter-metallic bond between the two parts.
Wetting can occur only if the surface of copper is free of contamination and oxide film, and the solder and the work surface have reached the proper temperature.
Resoldering and desoldering
Resoldering. It is very difficult to correct poorly made joints. So make good joints in the first place. Try to prevent re-soldering of joints as much as possible. A dry or disturbed solder joint usually requires reheating and re-flow of solder by applying a suitable quantity of flux.
Desoldering. Desoldering is required when components in the circuit need to be removed or replaced. To remove a damaged or defective component, either a desoldering pump or a desolder braid can be used.
Using a desoldering pump. The desoldering pump consists of a spring-loaded plunger. During the desoldering operation, the plunger is released at the push of a button and the molten solder then drawn up into the pump. Sometimes, it may take more than one attempt to clean the soldered point. You may add more solder to the joint and then desolder the whole quantity with the pump. Ensure that the components and PCBs are not damaged by overheating.
Using a desoldering braid or wick. The desoldering braid or solder wick is especially effective for desoldering a difficult joint. It is a simple and excellent alternative to a desoldering pump.
The desoldering braid, made from fine copper, draws molten solder up into the braid. To desolder using it, place a short length of the wick on the point to be desoldered. Place the hot bit of the soldering iron over the wick and press. The bit subsequently melts the solder and the molten lead is drawn up into the braid. Take extreme care to ensure no damage happens to the printed circuit track when the braid is pulled off the solder point.
Wave soldering
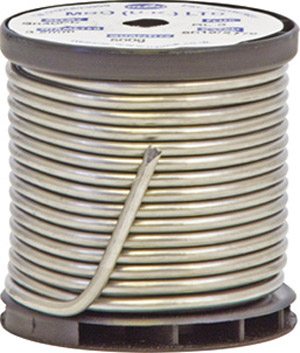
The wave soldering technique is used in the mass production of electronic circuits. It is an automated technique in which a large number of solder joints are made simultaneously. It reduces cost and increases the speed and reliability of production.
Wave soldering has three main requirements: solder, flux for wetting the soldering surface, and heat to activate the flux and melt the solder.