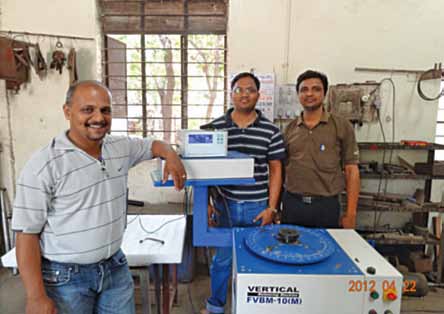
AUGUST 2012: “Keep the wheel round for smoother operations and lower vibrations” was probably the first rule of wheel making, and rightly so.
Excessive vibration in rotating machinery can cause unacceptable levels of noise and also substantially reduce the life of shaft bearings. Hence the idea is to remove all causes of vibration to run the unit vibration-free. Unfortunately, in practice, this cannot be fully achieved and, in spite of the best designs, some inherent cause of vibration, or unbalance, will persist.
The smart thing to do is to reduce this unbalance to such a level that it will not adversely affect the bearing life while reducing noise to an acceptable level.
The first step is to identify where the unbalances are and in what capacity. This is where a solution by Narayan Apte and Nikhil Mane comes in. Apte, a lecturer in electrical engineering at the Walchand College of Engineering, Sangli, and Mane, a lecturer in electronics engineering at KIT’s College of Engineering, Kolhapur, have come up with a device aptly named ‘digital electronic indicator for dynamic balancing of machines.’(I personally would have gone with ‘DEI’.)
Mass unbalance
There are two centre lines of a rotating body: Physical centre line and rotating centre line. The mass of the rotating body is distributed around physical centre line. If the mass distribution is even, both centre lines are coincident. But if the mass distribution is uneven, both centre lines are non co-incident. This gives rise to vibration in the shaft and subsequent problems arising out of the vibrations. Each rotating body needs to be checked for mass unbalance and should be corrected by removing or adding mass as required.
Conventional detection approach
The existing electronic hardware used for detecting mass unbalance is based on analogue circuitry. The indicator is based on an 8-bit microprocessor. Because of the analogue electronics involved, such devices have the drawbacks of difficult calibration, sensitivity to ambient parameter changes, large size, longer lead time (one to two weeks required for assembly and testing of one card) and higher cost.
The new approach
Apte and Mane developed a digital system based on the latest 32-bit processor from Texas Instruments (TI). The system is said to accurately detect the mass and angle of unbalance.
Apte explains the advantage of digital technology over analogue: “The existing electronic hardware was a combination of analogue and digital circuitry and hence it was quite bulky. Our system occupies negligible space and consumes much lesser power than the existing system. We are very confident that this device will have a lifespan of at least ten years.”
The custom-developed digital electronic hardware is built around TI’s 32-bit Piccolo series floating-point real-time processor, TMS320F28069, which is clocked at 80 MHz. The device consumes 5W power and uses state-of-the-art digital signal processing to extract mass unbalance and its angle. The operator then uses the information to adjust the parameters of the rotating object and reduce the vibrations.
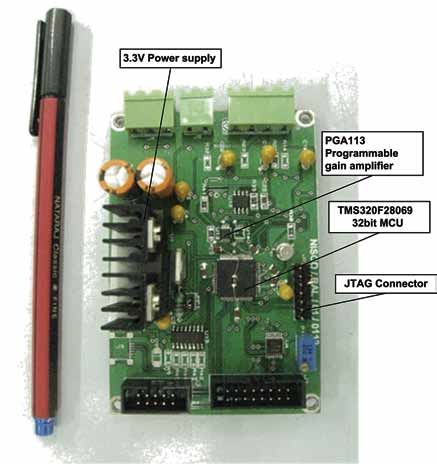
The unbalance in the rotating body is sensed by a piezo-sensor. The output of the piezo-sensor is amplified by using PGA113, a programmable gain amplifier, and then digitised using on-chip 12-bit analogue-to-digital converter. An inductive proximity sensor is used to sense speed and to generate reference signal. By extracting the fundamental component of the vibration signal, the amount and angle of the vibration are found out.
As the system relies purely on digital signal processing, the accuracy and precision, repeatability are greatly enhanced. The resulting circuit is very compact and much more efficient. To reduce the cost, the developers reduced the number of components and selected a fixed-point processor.
Hurdles aplenty
“Whenever you start something very new, you will face challenges. I mean, in many ways, that was one sign that we were heading in the right direction,” says Mane.
He explains: “The output of the piezo-sensor is highly noise-contaminated and it is very difficult to extract the unbalance signal. This problem aggravates in low-rpm machines—300-400 rpm machines of 1-3 tonne capacity. We worked on the design for a year and after a lot of debugging and tweaking, we managed to get the design right. Thankfully, all the pieces locked into action and have worked seamlessly.” The new indicator has undergone successful field trials for all machine capacities ranging from 5 kg to 3 tonnes and compliance for ISO1940.
Future plans
“The product is in the finished state and applicable for both vertical and horizontal type dynmaic balancing machines. Our immediate plan is to patent this design. We are working on adding user-interface facilities like TFT display and USB interface before it is launched nation-wide. It will be available as a sub-assembly of balancing machines manufactured by Balancing Instruments and Equipments Miraj Pvt Ltd, Miraj, India,” informs Mane.
The author is a tech correspondent at EFY Bengaluru