Radar absorbing materials are a special kind of polymer that convert radar energy into some other form of energy, such as heat, thus improving the stealth of a military aircraft. But there is a vast variety of such materials, each having its own characteristics and thus application.
The development of radar systems before and during World War II led to research on the interaction between electromagnetic radiation at radar frequencies and various materials. One aspect of this research is finding ways to reduce the returned signal. This was done not only to reduce interference between the radar signal and surrounding buildings (for example, radar masts and support structures that could reduce the designed performance of the radar itself), but also to help reduce hostile radar detection by properly designed anechoic systems and materials.
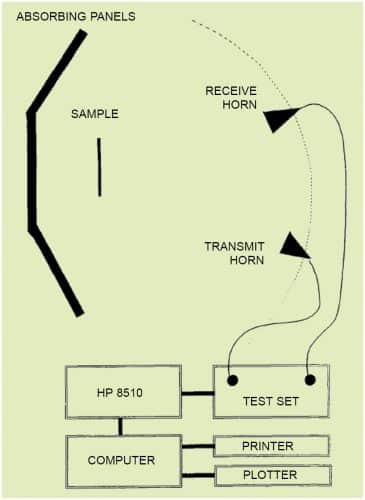
The Germans developed coatings for their underwater periscopes, snorkels, and command towers that achieved a nearly 26db decrease in reflection in the 112 to 195cm wavelength band. However, a number of physical deficiencies, primarily the coating’s lack of survivability in harsh environments, prevented the large-scale deployment of this material.
Since World War II, there has been an increasing interest in radar absorbing materials (RAM), culminating in ‘stealth’ US projects for the advanced technology bomber and advanced technology fighter and the deployment of RAM on warships. These developments have been based on a synergistic approach, obtaining the reduction of the radar cross-section through several complementary methods. The basic methods used are radar absorbing structures, transparent radar structures, geometric shape modification and the use of radar absorbing materials as surface coatings. The application of these technologies to all types of defence material is of utmost importance.
The increasing use of radars in war surveillance and weapon locating, in addition to the normal or traditional function of aerial target detection, means that improved radar cloaking and counter-surveillance techniques must be developed and deployed for all types of equipment. For existing material, applying radar cross-sectional reduction techniques could involve radical structural modification and, in some cases, may not be justifiable in terms of performance or cost. However, the selective use of thin radar absorbent coatings that apply to existing material would bring real benefits in terms of performance and cost-effectiveness under the right circumstances.
Radar is the most common method for detecting and tracking aircraft. Although radar is a necessary tool for air traffic management, the problem is in offensive military operations, which require the aircraft to attack its target unnoticed and escape. Radar involves the transmission of electromagnetic waves into the atmosphere; they then bounce off the aircraft onto the receiving antenna.
Conventional airplanes, such as airliners, are easily detected by radar due to their cylindrical shape in conjunction with engine knocks and the tailplane. The metals used in aircraft are also strong reflectors of electromagnetic waves and can be easily detected by radar. Compounds are also detected by radar, although usually not as easily as metals.
Radar absorbent material (RAM) is a specialised class of polymer based material applied to the surface of covert military aircraft, such as the F-22 Raptor and F-35 Lightning II, to reduce radar signature and thus complicate radar detection. These materials are also used in covert versions of unmanned tactical air systems such as the Boeing X-45. RAM is applied to the entire outer surface or (more often) to regions of high radar reflection, such as the edges of the surface.
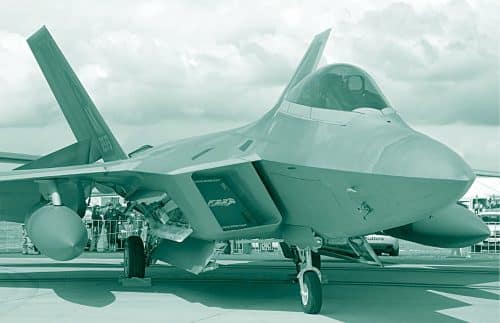
RAM works on the principle that the aircraft absorbs energy from electromagnetic waves to minimise the intensity of the reflected signal. RAMs are used in combination with other stealth technologies, such as flat design and hidden engines, to make it difficult to detect military aircraft. It is possible to reduce the cross-section of a jet fighter’s radar to the size of a medium-sized bird through ideal design and the application of stealth technologies. The information on the composition of the RAMs is kept secret by the military. Most RAMs consist of ferromagnetic particles embedded in a polymer matrix with a high dielectric constant.
One of the more common RAMs is called iron ball paint, which contains small metal coated spheres suspended in an epoxy based paint. The spheres are coated with ferrite or carbonyl iron. When electromagnetic radiation enters the iron ball paint, it is absorbed by the ferrite or carbonyl iron molecules, causing them to oscillate. Molecular oscillations then decay with the release of heat, which is an effective mechanism for damping electromagnetic waves. A small amount of heat generated by the oscillation is transferred to the aircraft structure where it is dissipated.
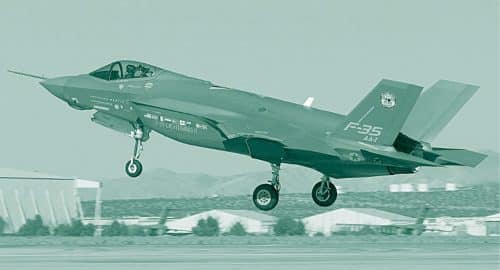
The second type of RAM consists of a neoprene foil containing ferrite particles or carbon black. This material, which was used in early versions of the F-117A Nighthawk, works on the same principle as iron ball paint by converting radar waves into heat. The USAF has introduced radar absorbent paints made of ferrofluidic and non-magnetic materials in some of its stealth aircraft. Ferrofluids are colloidal mixtures composed of ferromagnetic particles of nanometric size (less than 10nm) suspended in a carrier medium.
Ferrofluids are superparamagnetic, which means that they are strongly polarised by electromagnetic radiation. When the fluid is subjected to an electromagnetic field strong enough, polarisation causes ripples to form on the surface. The electromagnetic energy used to form these ripples weakens or removes the energy of the reflected radar signal. RAM cannot absorb radar at all frequencies. The composition and morphology of the material is carefully adapted to absorb radar waves in a specific frequency band.
There are three main classes of polymers: thermosets, thermoplastics, and elastomers. The most widely used polymers in aircraft are thermosetting such as epoxy resins and bismaleimides, which are used as a matrix phase in fibre composites and as structural adhesives. The aerospace applications for thermoplastics and elastomers are much smaller.
The properties of polymers that make them useful aerospace materials are their low weight, excellent corrosion resistance, and good ductility. Some polymers are also transparent for use in window applications. However, polymers have low stiffness, strength, fatigue life, and creep resistance, and therefore should not be used alone in structural applications.
Polymers are produced by polymerisation reactions called addition or condensation reactions, which link monomer units in macromolecules in the form of long chains. The chemical and physical structure of the molecular chains has a great influence on the mechanical properties.
Thermosets have higher stiffness, strength, and creep resistance compared to thermoplastics because the molecular chains are interconnected by cross-links. These cross-links resist chain slippage under tension and therefore increase mechanical properties.
Epoxy resin is the most widely used polymer for the aerospace industry and finds applications in carbon fibre composites and as a structural adhesive. Epoxy resin has good stiffness, strength, and environmental durability and can be cured at moderate temperatures (below 180°C) with little shrinkage.
Other thermosets used in composite materials include bismaleimide and polyimide, which are suitable for high temperature applications. Phenolic resin has excellent resistance to flammability and is used in car interior composite and moulded parts.
Thermoplastics have high toughness, ductility, and impact resistance, but high processing cost and low creep resistance limit their use in the aerospace industry. Thermoplastics such as PEEK are used as a matrix phase in fibre composites that require impact resistance.
Polycarbonate is used for aircraft windows due to its high transparency, scratch resistance, and impact resistance.
Elastomers lack the stiffness and strength necessary for aerospace applications, although their high elasticity makes them useful as a sealing material. Elastomers have high elasticity due to their coiled molecular structure that responds under load, similar to a spring.
The adhesives used to bond aircraft components and sandwich composites are often thermosetting, such as epoxy resin. Adhesives should have low shrinkage during cure to avoid residual tensile stress build-up at the joint. Proper surface preparation is essential to ensure a long-lasting, high-strength bond with a polymer adhesive.
The mechanical properties of polymers are inferior to those of aerospace structural metals and their use is restricted to relatively low temperature applications. Polymers transform from a hard, glassy state to a soft, rubbery state during heating, and the maximum working temperature is defined by the thermal deflection temperature or the glass transition temperature.
Polymers often contain additives for special functions such as colour, toughness, or fire. Radar absorbent materials are a special kind of polymer that converts radar (electromagnetic) energy into some other form of energy (such as heat) and thus improves the stealth of military aircraft. RAM should be used with other stealth technologies, such as aircraft shape design adaptations, to minimise radar cross-section.
Jawaaz Ahmad from Srinagar is a Design Fellow at Design Innovation Centre, Islamic University of Science and Technology, Awantipora, J&K