With the introduction of personal computers (PC) in 1980s, industrial automation was revolutionised. Industrial Automation is the use of automated control devices such as Programmable logic Controller (PLC), Computer Numerical Control (CNC), Remote Terminal Unit (RTU) etc to control industrial processes and machinery in place of labour intervention and dangerous assembly operations with automated ones.
There are various process variables such as temperature, flow, pressure, distance and liquid levels that can be sensed simultaneously, processed and controlled by complex microprocessor systems or personal computer (PC) based data processing controllers. They are designed in such a way that they can withstand temperature, pressure and other extreme environmental conditions yet be accurate, efficient, giving timely response and economical.
Functional Elements of Industrial Automation
An Industrial Automation system consists of various elements in synchronisation with each other performing functions like sensing, controlling, supervision and monitoring of industrial processes. The following figure shows various levels of functional elements of industrial automation system.
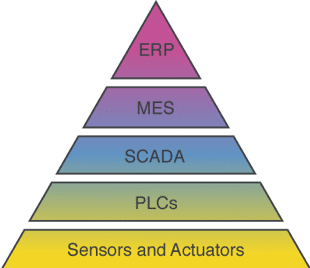
Functionally, an industrial automation system consists of Field level (Sensors & Actuators), Control level, Supervisory, production control level (SCADA) and Information & enterprise level (MES & ERP)
Field level
At the lowest level we find sensors and actuators which are installed at the field. Sensors are used to collect physical process signals and measurements such as flow, pressure, temperature etc. and convert them into electrical or pneumatic form. For example, LDR, thermocouple, strainguage etc. The signals from these sensors are used for processing, analysing and decision making to produce the control output. Control Systems like Programmable Logic controllers(PLCs), RTUs etc are connected to these sensors to produce the required output by processing the signals in accordance with the program and set values. Then the controllers produce the computed output and are applied as electrical or pneumatic signal inputs to the actuating elements. Actuators convert the electrical or pneumatic signals into the physical process variables such as controlling valves, relays, pneumatic actuators, DC motors etc.
Control Level
This level consists of control elements, microprocessor based electronic controllers or simply industrial computers that accept the signals from various sensors as well as command signals from human operators. These controllers can be analog or digital systems depending on the structure of control nature. Signals from sensors are processed by controller producing the control output to various actuating devices depending on the control structure. Out of available modern control devices, PLCs are most widely used robust controllers in industrial automation system which can deliver automatic control functions based on input from sensors.
A programmable logic controller (PLC) is a special form of microprocessor-based controller that uses programmable memory to store instructions and to implement functions such as logical, sequencing, timing, counting and arithmetic to control machine and processes. PLCs have rugged CPU, digital I/O, analog I/O and communication modules such that they can operate at industry environment conditions to control the various process parameters using the program written in accordance with the industrial process. They are programmed using application software on personal computers. The software allows users to create, edit, document, store and troubleshoot programs. The most commonly used programming language for PLC is ladder programming, which is easier for any operator to understand, operate, write and debug.
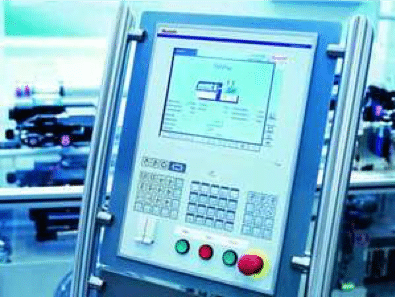
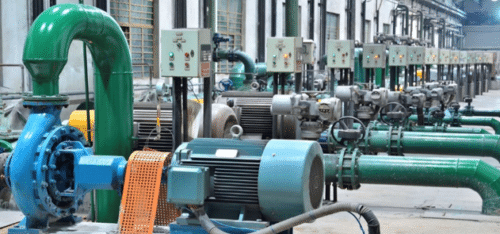
Programmer writes, debugs and installs the program into PLC. Then PLC performs a repetitive cycle of operations called program scan. Wherein it scans the input devices and updates a memory table indicating their status. Next, the PLC executes its ladder program and updates a memory table which indicates whether output devices should be on or off. Depending on this output table, PLC changes the condition of the output devices.
Examples of PLCs are Allen Bradley PLC 5, Allen Bradley SLC500, SIMATIC PLC from Siemens, Omron Plc, ABB plc etc.
PLCs come with advantages like flexibility, easy implementation of changes and correcting errors, enormous quantities of contacts, low cost, pilot running, visual observation, easy programming method, reliability and maintainability and documentation. Only disadvantage in using PLC is that it makes use of fixed programs for applications and in some cases fail safe operations can be possible only through wired control.
Supervisory control and production control level
Next level of control is supervisory control, which controls the smaller subsystems. It consists mainly of process computers and Human Machine Interfaces(HMIs). These personal computers perform elevated level control operations like set point computations, performance monitoring, diagnostics, start-up, shut down and other emergency operations. Most of the system contains Distribution Control System (DCS) or Supervisory Control and Data Acquisition (SCADA) and Human Machine Interface (HMI) in this level.The SCADA concept was developed as a universal means of remote access to a variety of local control modules, which could be from different manufacturers allowing access through standard automation protocols. They can control large scale processes that can include multiple sites and work over large distances as well as small distance.
A SCADA system mainly consists of a plant computer, supervisory computer, multiple remote terminal units(RTUs)/Programmable logic controllers(PLCs) and communication infrastructure
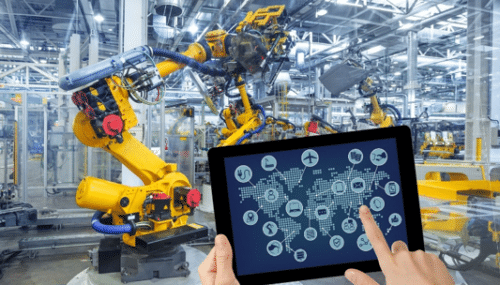
- Plant Computer: It is a PC or mainframe computer with necessary software responsible for communicating with the field equipment like RTUS, PLCs etc. The SCADA system presents the information to the operator in the form of a mimic through HMIs. i.e. the operator can see a representation of the plant being controlled. For example, consider a pump connected to a pipe. The operator can observe pump is running and how much fluid is pumped through the pipe. He can turn off the pump when required.
- Supervisory computers: It refers to the computer and software responsible for communicating with the field connection controllers- PLCs, RTUs and HMI software. These computers gather data on the process and sends control commands to the field connected devices. In smaller SCADA systems, the supervisory computer is a single PC with HMI. Whereas larger SCADA systems has several HMIs hosted on client computers, with multiple servers for data acquisition, distributed software applications and disaster recovery sites.
- Multiple Remote Terminal Units(RTUs) or Programmable Logic Controllers(PLCs): Actual control is automatically performed by RTUs and PLCs. They are directly connected to the physical equipment and reads status data from a switch or valve: reads measurements such as pressure, flow, voltage or current. Depending on the program, they process the signal and sends proper signals to control equipment such as closing a switch, motor speed control etc.
- Communication Infrastructure: – SCADA systems use combinations of radio and direct serial or modem connections to meet communication requirements. At large sites, Ethernet and IP over SONET is used. This connects supervisory computer system to the RTUs and PLCs and may use industry standard or manufacturer proprietary protocols. They operate automatically on the near real time control of the process. But process continues even during communication network failure. Hence some critical systems will have dual redundant data highways.
Effective SCADA system can result in significant savings of time and money. Modern SCADA systems allow real-time data from the plant floor to be accessed from anywhere in the world. This allows governments, businesses and individuals to make data driven decisions about how to improve their processes. Control can be centralised by using single system over multiple sites and large distances called Panorama SCADA system. It can monitor and control multiple systems and process simultaneously. These applications range from 50 variables to 1,600,000 I/O operations. One of the suppliers for such system is Electro in partnership with Codra. Without SCADA software, it would be extremely difficult if not impossible to gather sufficient data for consistently well-informed decisions.
Human Machine Interfaces (HMIs) or Man Machine Interfaces (MMIs) is a software application that present information to an operator or user about the state of a process and to accept and implement the operators control instructions. HMIs help in integrating humans into complex technological systems.
A good HMI can provide realistic and natural interactions with external devices. They help in error reduction, increased system and user efficiency, improved reliability and maintainability, increased productivity, increased user acceptance, comfort, less training, less stress etc.
Information and Enterprise level
This is the top level of industrial automation which is more sophisticated. It uses artificial intelligence to manage whole automation system. This level mainly takes care of commercial activities like production planning, customers and market analysis, orders and sales etc. It is less concerned with technical aspects.
Industrial communication networks transfer the information from one level to the other, providing continuous flow of information. It may vary at various levels. For example, RS485, CAN, Device Net etc.
Thus, if we draw a graph to represent these level, we get a pyramid. The top level consists of enterprise level and bottom consists of sensors and actuators. At bottom level, we get detailed information about the process and as we go up information becomes more aggregated or complex.
Automation using SCADA systems can be found in most of the systems. It can be found in modern industries like: Â Energy, Food & beverages, Manufacturing, Oil & gas, Power, Recycling, transportation, Water & waste water etc. Also, in day to-day life applications like local supermarket, tracking energy use at home, lift control in a multi-storey building etc.
Thus, there is no doubt that SCADA, HMI & PLCs are playing vital role in today’s industrial automation.
Plc. Servo motor . Automation project
Hi Arun, Kindly elaborate on your query.
Our company supplies second hand elctronics. Such as ocb, plc, ac drives, navigation system, marines automation. Sir, tell us whatever you want, we will try as much as we can.