In an official document sent out by Ministry of Power on December 14, 2018, the government of India has outlined several key facts, figures and a plan to support the expansion of EVs in the country.
Electric vehicles, also called EVs, use one or more electric or traction motors for propulsion. These may be powered through a collector system using electricity from off-vehicle sources, or may be self-contained with a battery, solar panels or an electric generator to convert fuel into electricity. EVs include, but are not limited to, road and rail vehicles, surface and underwater vessels, electric aircraft and electric spacecraft.
EVs first came into existence in the mid-19th century, when electricity was among the preferred methods for motor vehicle propulsion, providing a level of comfort and ease of operation that could not be achieved by petrol cars of the time. Limitations of heavy weight, short trip range, long charging time and poor durability of batteries compared to later internal combustion engine vehicles led to a worldwide decline in their use; although, EVs have continued to be used in the form of electric trains and other niche uses.
At the beginning of the 21st century, interest in electric and other alternative fuel vehicles increased due to growing concerns over the problems associated with hydrocarbon-fueled vehicles, including damage to environment caused by their emissions, sustainability of the current hydrocarbon-based transportation infrastructure as well as improvements in EV technology.
Some advantages of EVs are:
- Most electric motors can travel 150km to 180km before these need to be charged.
- No tail pipe exhaust means no greenhouse gases such as carbon-dioxide, NOx pollution and PM10.
- No oil consumption means less reliance on fossil fuel.
- Cars can be recharged whenever convenient to user.
- More cost-effective than regular cars because of long-lasting battery use.
- Cheaper to maintain because of fewer moving parts.
- Creates less noise pollution because of a silent engine.
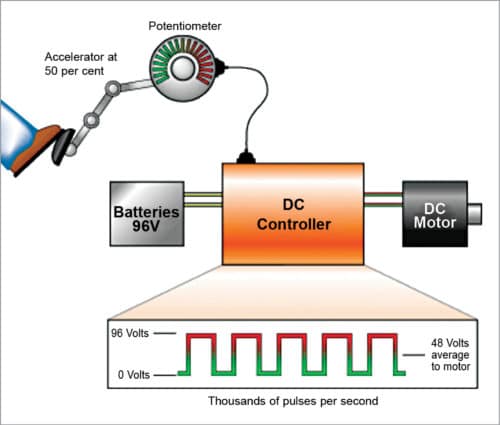
Working of an EV
The three main components of an EV are: electric motor, controller and battery. The electric motor needs no oil, no tune-ups and, since there are no tailpipe emissions, it does not necessitate any smog checks.
When you switch on the vehicle, current is passed from the battery. The controller takes power from the battery and delivers it to the motor. Before passing the current to the motor, the controller converts 300V DC into a maximum of 240V AC, 2-phase power, which is suitable for the motor.
The accelerator pedal hooks to a pair of potentiometers (variable resistors). These potentiometers provide the signal that tells the controller how much power it is supposed to deliver.
When you push on the accelerator pedal, a cable from the pedal connects to these two potentiometers. There are two potentiometers for safety. The controller reads both potentiometers and makes sure that their signals are equal. If not, then it does not operate. This arrangement guards against a situation where a potentiometer fails in the full-on position.
The controller can deliver zero power (when the car is stopped), full power (when the driver floors the accelerator pedal) or any power level in between. The electric motor then converts electrical energy into mechanical energy, which moves the vehicle forward.
Other components of an EV are electric engine, regenerative braking and drive system.
Battery. The battery is the key component of an EV because of the following:
- Range of the vehicle depends almost entirely on HV battery.
- It is the heaviest electrical component.
- It is also the most expensive electrical component.
A battery electric vehicle (BEV) uses a battery that can be charged using ordinary grid electricity at a specialised power station. Besides conventional lithium-ion battery technologies, there are lead-acid, nickel-metal-hydride (NiMH) and zebra.
Lithium-ion
Today’s EVs mostly use lithium-ion batteries—the same technology that can be found in a laptop or e-book reader. These batteries are now considered to be the standard for modern BEVs. There are many types of lithium-ion batteries and each has different characteristics. But vehicle manufactures are focused on variants that have excellent longevity.
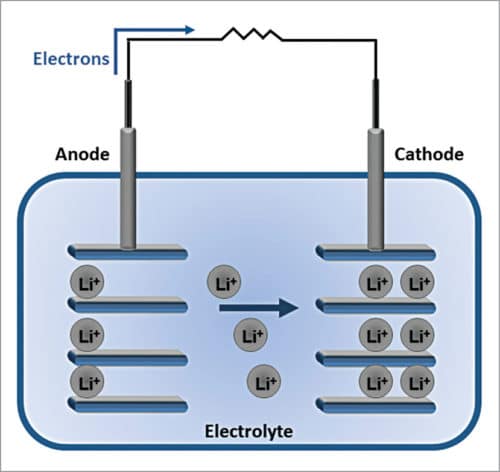
Compared to other mature battery technologies, lithium-ion offers many benefits. For example, it has excellent specific energy (140Wh/kg) and energy density, making it ideal for BEVs. It is also excellent in retaining energy with a self-discharge rate (five per cent per month), which is an order of magnitude lower than NiMH.
However, lithium-ion batteries also have some drawbacks. Six significant problems with current lead-acid battery technology are:
- These are heavy; a typical lead-acid battery pack weighs 463.6kg (1000 pounds) or more.
- These are bulky; the car used as an example here has 50 lead-acid batteries, each measuring roughly 15.24×20.32×15.24cm (6x8x6-inch).
- These have a limited capacity; a typical lead-acid battery pack might hold 12 to 15 kilowatt-hours of electricity, giving the car a range of only 80.5km (50 miles) or so.
- These are slow to charge; typical recharge times for a lead-acid pack range between four to ten hours for full charge, depending on battery technology and charger.
- These have a short life—three to four years, perhaps 200 full charge/discharge cycles.
- These are expensive—perhaps US$ 2000 for a typical battery pack.
When you place the battery in a device, positively-charged lithium-ions are attracted to and move towards the cathode. Once it is bombarded with these ions, the cathode becomes more positively-charged than the anode, and this attracts negatively-charged electrons.
As electrons start moving towards the cathode, these are forced to go through the device and use the energy of the electrons flowing towards the cathode to generate power. You can think of this kind of like a water wheel, except instead of water flowing, electrons are flowing.
Lithium-ion batteries are great because these are rechargeable. When the battery is connected to a charger, lithium ions move in the opposite direction as before. As these move from the cathode to the anode, the battery is restored for another use.
Lead-acid and NiMH batteries
Both lead-acid and NiMH batteries are mature battery technologies. These were originally used in early EVs such as General Motor’s EV1.
However, these are now considered to be obsolete with regards to their use as the main source of energy storage in BEVs. Lead-acid batteries have been used in conventional petroleum-driven vehicles and are relatively inexpensive. However, these have a poor specific energy of 34Wh/kg.
NiMH batteries are considered to be superior as these can have up to double the specific energy—68Wh/kg—compared to lead-acid batteries. This allows EVs that utilise NiMH batteries to be significantly lighter, leading to reduced energy cost for propelling the BEVs.
NiMH batteries also have greater energy density compared to lead-acid batteries, which allows the battery system to be contained within a smaller space.
NiMH batteries do have some drawbacks such as lower charging efficiencies than other batteries. There is also an issue with self-discharge (up to 12.5 per cent per day under normal room temperature conditions) that is exacerbated when the batteries are in a high temperature environment. This makes NiMH batteries less ideal for hotter environments.
Zebra
The sodium or zebra battery uses a molten chloroaluminate-sodium (NaAlCl4) as the electrolyte. This chemistry is also occasionally referred to as hot salt. A relatively mature technology, the zebra battery has an energy density of 120Wh/kg and reasonable series resistance.
Since the batteries must be heated for use, cold weather does not strongly affect their operation, except increasing heating costs. Zebra batteries have been used in several EVs. These can last for a few thousand charge cycles and are non-toxic.
Downsides to the zebra battery include poor power density (<300W/kg) and the requirement of having to heat the electrolyte to about 270°C (520°F), which wastes some energy and presents difficulties in long-term storage of charge.
Flow batteries
A flow battery, or redox flow battery (after reduction-oxidation), is a type of electrochemical cell where chemical energy is provided by two chemical components dissolved in liquids contained within the system and separated by a membrane. Because of chemical energy, ions (charged atoms or molecules) are generated and flow through the membrane. These produce an electric charge while both liquids circulate in their own respective space.
A flow battery may be used like a fuel cell (where spent fuel is extracted and new fuel is added to the system) or like a rechargeable battery (where an electric power source drives regeneration of fuel). While it has technical advantages over conventional rechargeable ones, such as potentially separable liquid tanks and near unlimited longevity, currents are comparatively less powerful and require more sophisticated electronics. Energy capacity is a function of the electrolyte volume (amount of liquid electrolyte), and power is a function of the surface area of electrodes.
Flow batteries are unique and the most practical for renewable energy to road transport due to the following reasons:
- Rapid and safe charging by electrolyte exchange
- Wheel-to-wheel efficiency four times better than hydrogen as fuel
- Operating costs equal to conventional diesel-fuelled vehicles
- Totally recycled fuel
- Zero emission at point of use
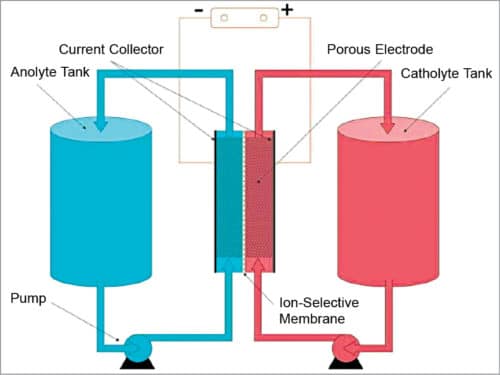
Motor controller
Control of an EV is not a simple task in that its operation is essentially time-variant (for example, operation parameters of an EV and road conditions are always varying). Therefore the controller should be designed to make the system robust and adaptive, improving the system on both dynamic- and steady-state performances.
Currently, the major limiting factor for the widespread use of EVs is the short running distance per battery charge. Hence, besides controlling the performance of the vehicles (that is, smooth driving for comfortable riding), significant efforts must be made for the energy management of batteries. However, from the viewpoint of electric and control engineering, EVs are advantageous over traditional vehicles with an internal combustion engine. Basic performance requirements of the EVs’ motor drive system are high performance, low loss, high power density, low speed, high torque, a wide range of variable speed, strong overload capacity and good reliability.
Presently, brushed DC motor, brushless DC motor, AC induction motor, permanent magnet synchronous motor (PMSM) and switched reluctance motor (SRM) are the main types of motors used for EV driving. Selection of the motor for a specific EV is dependent on such factors as intention of the EV, ease of control and so on.
To control an EV, the objective is to control the torque of the driving machine. The throttle position and the brake are inputs to the control system, which is required to be fast-responsive and low-ripple. An EV requires that the driving electric machine has a wide range of speed regulation. To guarantee speed-up time, the electric machine must have large torque output under low speed and high overload capability. And to operate at high speed, the driving motor should have certain power output at high-speed operation.
Electric engine
The electric engine propels the electric car. An engine uses either AC or DC current. An AC engine, commonly used in electric cars, is lighter and less expensive than an engine that uses DC current. AC engines have fewer moving parts and are, hence, prone to fewer mechanical problems.
Regenerative braking
In a battery-powered EV, regenerative braking (also called regen) is the conversion of the vehicle’s kinetic energy into chemical energy stored in the battery, where it can be used later to drive the vehicle. It is braking because it also serves to slow the vehicle. It is regenerative because energy is recaptured in the battery where it can be used again.
When we apply force to the brake pedal, the car slows down and the motor works in reverse direction. When running in invalidate direction, the motor acts as the generator and, thus, charges the battery. Using regenerative braking in an EV reduces cost of fuel, increasing fuel financial system and lowering emission. The regenerative braking system provides braking force while speed of the vehicle is low and, hence, the traffic stop-and-go. Thus, deceleration required is less in an EV.
Drive system
The drive system transfers mechanical energy to the traction wheels in generating motion. It makes the transmission system unnecessary in an electrical vehicle.
Charging station
EVs are available in a variety of models with different ranges and capabilities. To recharge, these are plugged into a source of electric power through electric vehicle supply equipment (EVSE). EV charging stations—also called electric recharging points, charging points, charge points and EVSE—are an element in an infrastructure that supplies electric energy for the recharging of EVs, such as plug-in EVs. These stations are also needed when travelling, and many support faster charging at higher voltages and currents than are available from residential EVSE.
Types of charging
The various types of charging are described below.
Level 1 charging
Level 1 charging uses the same 120V current found in standard household outlets in the USA and can be performed using the power cord and equipment that most EVs come with. Low installation cost is its advantages, while slow charging (typically 4.8 to 8.04 kms, or 3 to 5 miles, of range per hour) is the disadvantage.
Level 2 charging
Level 2 charging uses 240V power to enable faster regeneration of an EV’s battery system. This type of charging requires installation of an EVSE unit and electrical wiring capable of handling higher voltage power. It has a faster charge time (16.09 to 32.2 kms, or 10 to 20 miles, of range per hour). It is more energy-efficient than level 1 charging, but is a little more expensive.
DC fast charging (480V)
DC fast charging provides compatible vehicles with an 80 per cent charge in 20 to 30 minutes by converting high-voltage AC power to DC power for direct storage in EV batteries. Automakers currently have three specifications for DC fast charging plugs, CHAdeMO (or CHArge de Move), SAE Combined Charging System (CCS) and Tesla Supercharger standards.
Nissan and Mitsubishi vehicles use CHAdeMO, while many current and upcoming vehicles from American and European manufacturers have SAE CCS ports. Tesla’s Supercharger equipment is only compatible with Tesla Model S or later vehicles, although the company is developing an adaptor that will allow Tesla owners to use CHAdeMO equipment.
Charge time has reduced drastically—it is nearly as fast as refuelling a petrol vehicle. It is significantly more expensive than level 1 or 2 equipment, and high-voltage 3-phase power connections to utilities further increase installation costs. Also, it has potential issues with cold weather operation.
EV charging in India
The Indian government has finally announced a policy for the rollout of EV charging infrastructure. In an official document that was sent out by Ministry of Power on December 14, 2018, the government has outlined several key facts, figures and a plan to support the expansion of EVs in the country. Push for electric mobility charging stations will first be rolled out in cities with a population of greater than four million residents, that is Mumbai, New Delhi, Bengaluru, Hyderabad, Ahmedabad, Chennai, Kolkata, Surat and Pune.
The government has also announced that in the cities mentioned above, there will be at least one EV charging station in a grid of 3km. On the highway, there will be an electric car station every 25km. The government has also recognised key corridors that will have electric charging stations for both small private vehicles and large commercial vehicles.
The most important announcement in the circular is that the setting up of these charging stations will be a de-licensed activity and, thus, rollout is expected to be quite rapid. Charging stations will also be free to obtain electricity from any power company through the open access system.
While there are no restrictions on private charging stations being set up in a house/apartment complex/office block, public charging stations have to meet minimum requirements. Every charging station will have to have a minimum of three fast chargers, one CCS-style plug, one CHAdeMO (equivalent to move using charge) and one type-2 AC fast charger. While the first two plugs will have to give a minimum output of 50kW and 200V to 1000V, the type-2 plug will have to be a minimum of 22kW and 380V to 480V.
In addition, charging stations will also compulsorily have two slow/moderate charge points, one with Bharat DC-001 connection with 15kW and 72V to 22V, and the other, Bharat AC-001 with 10kW and 230V.
To propel the growth of EVs in India, the government recently slashed the applicable rate of Goods and Services Tax (GST) on lithium-ion batteries. Many states have also geared up for the uptake of EVs as a means of mainstream mobility.
Mahima Vithal is an electrical engineer from Mumbai University
I don’t know whether you see this comment or not
Well the information was just amazing. The way it has explained. Thanks for it
One suggestion that. lots of electric vehicle conversation kit are available in market
So get us the DIY of electric vehicle