Driverless cars are aimed at reducing the number of accidents, cutting down emission and easing congestion. This article details some factors that must be considered while designing autonomous vehicles.
Autonomous vehicles combine sensors and software to control, navigate and drive vehicles, including cars, trucks, bikes and drones. These may or may not need driver assistance depending on their design or development. Fully-autonomous vehicles do not require human drivers for safe operation. Some may not even have a steering wheel, for example, Google’s Waymo car.
On the other hand, a partially-autonomous vehicle can take full control of the vehicle but may require a human driver to intervene if the system encounters uncertainty, like Tesla. Such vehicles are designed with varying amounts of self-automation, with brake and lane assistance to highly-independent, self-driving prototypes.
Driverless cars are aimed at reducing the number of accidents, emission and congestion. This is achievable because autonomous cars are better at following traffic rules than humans. There are things required to know for a smooth drive, including location of car or objects around the car, fastest and safe route to destination, and capability to control the driving system. It is also important to know when and how to perform required actions.
Components required for autonomous car design
Autonomous cars being tested today make use of a combination of laser illuminating detection and ranging (lidar), radio detection and ranging (radar), sound navigation and ranging (sonar), cameras, GPS and inertial measurement units (IMUs) along with 3D road maps. These sensors and systems work together, and data is analysed in real time to manipulate the steering, acceleration and braking.
Radar sensors help monitor the position of nearby vehicles. Ultrasonic sensors assist vehicles while parking. Use of both types of sensors has resulted in lidar technology. Lidar sensors help detect the edges of roads and identify lane markings by bouncing pulses of light off the car’s surroundings. These also alert cars to nearby objects, including other cars, pedestrians, bicyclists and other obstacles.
Lidar technology is also used to build a 3D map to enable the car to see its surroundings and spot potential hazards by determining the size and distance of all things around it. It is great at capturing information in various types of ambient light—whether night or day, sunny or cloudy.
Lidar and cameras, together with radar and GPS antennae, work to make the car perceive its surroundings and allow it to determine its position. Cameras detect traffic lights, read road signs and road markings, and keep track of other vehicles, while also looking out for pedestrians, bicyclists, cars and other obstacles. These may, however, face difficulty in shadows or poor lighting conditions. A combination of ultrasonic, radar, cameras, GPS antennae and lidar sensors digitally map out the road ahead of an autonomous car and help it see where it is going.
While Google continues to rely on lidar, Tesla strongly believes that camera vision will ultimately prove superior. Ziv Aviram, chief executive officer, Mobileye, agrees, “Camera vision is simply more sophisticated than lidar, and offers much higher resolution data.”
Satyarth Praveen, research engineer, Hi-Tech Robotic Systemz, adds, “It depends on the use case. Lidar has a resolution factor as well. Since it makes measurement based on reflected light, lidar makes the device scene-dependent as well. Meanwhile, cameras are more dependent on the software being used to understand the captured scene. Since lidar is immune to atmospheric variations, missed detection is less of an issue with it. So just the selection of a device cannot guide towards what works better; there are a lot of other things that go along with it.”
Path planning technology
Hard-coded rules, obstacle avoidance algorithms, predictive modelling and smart object discrimination between different vehicles on the road help the software follow traffic rules and navigate through obstacles. To stay on the road, avoid collisions and obey traffic laws, autonomous cars rely on path planning approaches including predictive control and behaviour-based models. Algorithms process the information gathered by the autonomous car technology to enable the cars to react accordingly to variables such as traffic, road construction, detours and varying weather conditions.
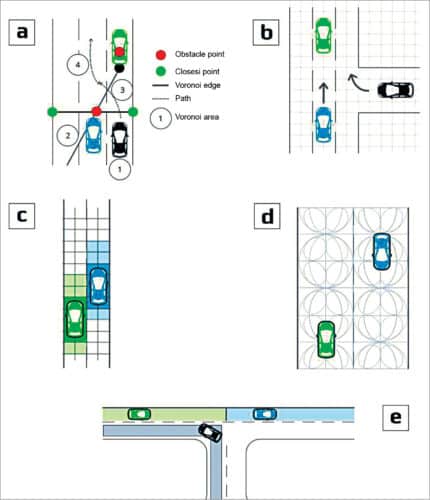
Some algorithms used for finding corridors and spaces are:
- Voronoi diagram algorithm, which generates paths that maximise the distance between a vehicle and surrounding obstacles
- Occupancy grid algorithm, which calculates risk and feasibility based on the presence of obstacles, and lane and road boundaries
- Driving corridors algorithm, which recreates continuous collision-free spaces, bounded by lanes and other obstacles between which the vehicle is expected to drive; uses data from digital maps built by simultaneous location and mapping models
Denver’s (in Colorado, USA) Regional Transportation District has launched the first on-road deployment of an autonomous vehicle (shuttle). Although, it will not have a driver, an ambassador will always be present on the shuttle to ensure safety of the passengers and operations. Data collected will be used to improve future deployments and bring autonomous services into wider usage.
Design considerations for lidar
There are thermal challenges involved in designing lidar systems. The distance a lidar sensor can measure is affected by its operating temperature. For lidar systems that incorporate custom systems-on-chip (SoCs) ICs, operating temperature of internal components and external surfaces are influenced by their internal heat generation.
Surrounding temperature and air flow, and cooling mechanisms are the key parameters to design lidar systems. Lidar systems that are mounted on vehicle roofs or other areas are directly exposed to the Sun. Hence, considerations for heating by solar radiation must be included.
To ensure that designs meet safety requirements, thermal simulation and analysis is done, which helps detect thermal issues before and in parallel with electrical and mechanical designing. This results in shortened overall design process and more robust product design.
Thermal analysis done early in the design process helps select designs that will work better among all other designs. With the development of electrical and mechanical designs, thermal aspects can also be refined, clearly indicating which designs should be prototyped and tested.
Good thermal management of PCBs and critical ICs on the board ensures reliability and good performance. Internal lidar components generate heat, which is convected, conducted and radiated to enclosure internal surfaces. Heat-transfer effectiveness for critical IC components can be improved by adding new conduction paths or through increasing heat transfer surface area. Using a heatsink on the device can lower component temperature.
A direct conduction path to the outer enclosure is recommended when a significant reduction in temperature is needed. Adding thermal conduction in solids such as aluminium is much more efficient than convection and conduction through air. Temperature reduction is influenced by IC heat dissipation and thermal resistance between the ICs and enclosure.
Digital design to speed up development
Thermal design optimisation for a lidar system analyses a wide range of vehicle integration and use case scenarios. Solar radiation can heat up vehicle-mounted lidar when a vehicle is being driven on a hot, sunny day. These simulation-driven analyses, from early prototyping stages, empower designers to account for various performance and life-limiting factors in their design and conduct optimisation analysis.
Testing autonomous vehicle functionality in extremely hot and cold weather conditions is a critical part of vehicle verification and validation. To rely on the virtual design framework, accuracy of simulations is important for design engineers to make design decisions.
Electronic cooling simulation can be calibrated with non-destructive thermal characterisation to ensure accuracy. Thermal simulation can be extremely useful to ensure reliability of lidar and other sensors, and autonomous functionality-enabling electronics for both sensor companies and vehicle manufacturers.
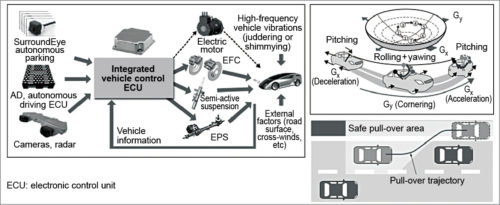
Integrated vehicle control structure
Lassaad Ben Cheikh, product marketing manager – automotive division, Infineon, says, “To meet safety and reliability requirements for autonomous vehicles, electronic systems must transition from fail-safe/fail-silent to fail-operating modes. To ensure robustness, availability and functional safety of critical systems, an effective strategy requires a two-channel architecture for electronic control units handling safety-critical functions.” Safe automation levels in passenger vehicles defined by Society of Automotive Engineers (SAE) are shown in Fig. 3.
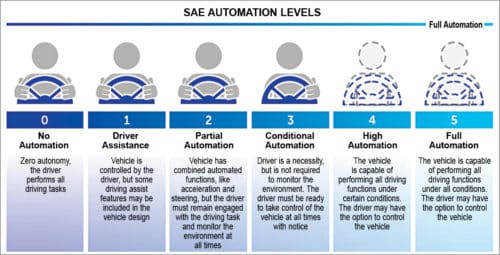
Due to integration of different components and automated features, it is important to ensure their interoperability within the vehicle. An autonomous car relies on devices and components that exchange, share and interpret data. Interoperability ensures that these devices and components can form an integrated ecosystem within the vehicle, seamlessly communicating with one another for a safe ride.
Interoperability of components ensures these will work together in a secure manner, without sacrificing performance. To check for issues as well as how other devices or components in a system impact each other, testers can place products in a simulated environment. Software testing is also an effective way to check interoperability as it uses manual and simulated test processes to verify that the product meets all functional, performance, security and quality requirements.
There are several ways manufacturers can mitigate cybersecurity risk in connected devices. These are:
- Use of certified products that are correctly configured
- Certification of information security management systems
- Threat risk assessments vulnerability assessments and penetration testing
A reliable, high-performance electric power steering is made possible by aligned solutions featuring sensors and low-loss MOSFETs. It enables advanced driver assistance systems such as side-wind compensation, lane assist/keeping and parking assistance systems. It improves fuel efficiency, car handling, overall driving experience and comfort. It can be adapted via software to suit diverse car models as well as dedicated driving modes.
Praveen adds, “Sensors must be carefully selected, as the wrong choice can make the problem a lot worse. Processing power used to comprehend and react based on the data collected from sensors must be powerful enough to give control signals in real time. Any delay in reaction to the scene can prove fatal. Software and logic used to get sensor data and control the vehicle must be efficient. Communication is an important factor as any loss of communication between any pair of devices can lead to critical failure.”
To sum up
Research and development is going on all across the world to produce safe and reliable autonomous vehicles. These vehicles depend on a number of external factors such as roads, traffic and weather of the location, among others. There is a need for data analysis and testing to have the most suitable and safe design. Sensors and systems should be designed such that these do not interfere with other integrated components in autonomous vehicles.