“If everything seems under control, you’re just not going fast enough” — Mario Andretti
For years, automakers have been continuously challenged with the need for more power. In the early days, cars were powered with a six-volt battery right up to the mid 1950s when automotive systems evolved to a 12V power source to meet the perpetual need for more power. Not only did automakers have to anticipate new power delivery demands for windows, steering and seats, but the need for more power was pivotal for the new high-compression engines.
In recent times, CO2 emission compliance standards have motivated OEMs to reconsider how to power the automobile again. While OEMs are introducing electrified vehicles to meet these standards, there has yet to emerge a harmonized approach for delivering electric power, not only to the motors but to all the subsystems in a vehicle.
This lack of clarity is compounded by the tremendous increase in power requirements. Automobiles with combustion engines typically operate with an electric power level between 600W to 3kW. New electrified EV, HEV, PHEV vehicles (xEV) require power levels of 3kW to over 60kW – more than 5 – 20 times the power.
That 5 – 20x increase puts tremendous strain on vehicles in terms of increased size, weight, and complexity of the power delivery network (PDN). These demands negatively impact energy efficiency, reliability and even comfort and safety as the added size and weight necessitate tradeoffs in vehicle features. There simply isn’t enough space to accommodate all the electrical requirements if car manufacturers proceed with traditional methods of power delivery. To meet this challenge they will need to find a solution that is not only lightweight and compact to mitigate the enormous increase in power, but is also flexible and can be reused across the fleet.
In addition to the major technical challenges, OEMs are also ratcheting up the pressure and making commitments to fully electrify their fleets over the next decade (Figure 1), even while the specifics of how to achieve the goal remains an open question. There is no clear path to standardizing electrification across the electric vehicle market. So while OEMs will likely all arrive at the same place, the PDNs they design will be different.
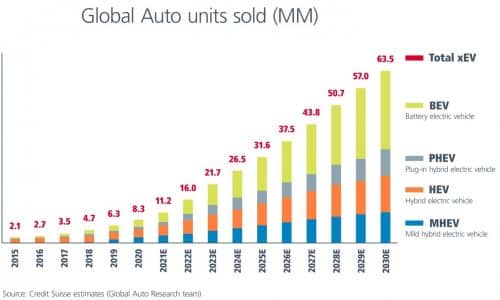
Fueling the electrification momentum
For many years, EV production volumes were less than 1% of the overall vehicle production output worldwide. According to the Credit Suisse Global Auto Research team, that will soar from 11% in 2020 to 62% in 2030, topping out at 63 million vehicles worldwide. Of those, nearly half, 29 million are expected to be fully electric.
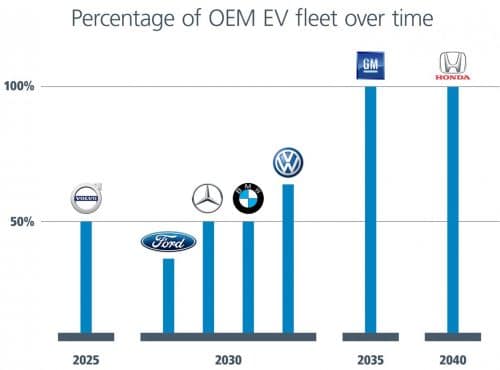
What is driving the explosive growth in electrified vehicles? While emissions compliance and government incentives started this ball rolling, it is consumer desire that is building the steep demand as OEMs are moving the electric vehicle from niche to mainstream. These OEMs are now making bold commitments. (Figure 2)
OEMs are now electrifying some of the most popular and beloved vehicles. GM Hummers, the new Ford Mach E (the electric Mustang) and now the flagship F150 Light-Duty Truck (Lightning) are being electrified. These models are drawing attention from the masses because of impressive performance enhancements and sleek designs.
These new vehicles, with improved fast-charging technology and lower maintenance and repair costs, are the catalysts driving consumer demand and increasing the adoption of electric vehicles. Consumers see value and momentum is therefore growing.
High-stakes, high-performance electrification challenge
The number of vehicle platforms, consumer options, varying powertrain architectures and choice of battery and charging configurations all add to the complexity power system designers have to address as they work to electrify automotive fleets.
To optimize vehicle electrification, OEMs need to enhance power levels, decrease power delivery network size and weight, and provide better thermal management and reusability. The traditional way of designing power systems must transition from complex customized discrete-based design to a smaller, more flexible, easier-to-use, higher-density modular solution.
Accelerating electrification
To achieve their aggressive electrification goals, OEMs will need to reconsider their approach to power delivery architectures. In addition to finding a highly efficient solution, to accelerate and optimize electrification three top requirements need to be addressed.
- Power density: Whether designing a fast sports car, a light-duty truck or a family car, OEMs need to pack as much power as possible into a constrained space. Vehicles need compact and efficient power solutions.
- Flexibility / Scalability: Fleets have many vehicles using the same platform, so easy power scaling is essential when modifying the power between sedans, minivans, SUVs, etc. that share the same platform.
- Reusability: To achieve full fleet electrification, OEMs need to be able to reuse power designs across different models to speed time-to-market.
Power Density
The size and weight of power electronics used in various xEV platforms have a direct bearing on vehicle performance, energy efficiency and battery range. OEMs are aggressively reducing the size and weight of their power electronics in an effort to go further and faster and R&D teams are incentivized to reduce vehicle weight.
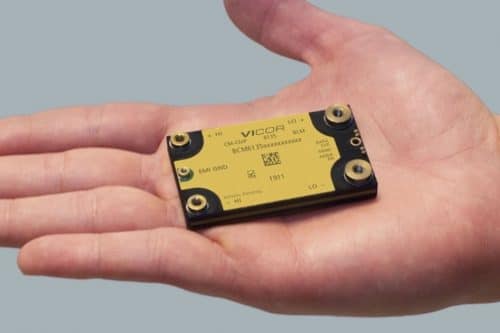
A small, 98% efficient bus converter module weighing only 68g from Vicor (BCM6135) can be bundled easily with EMI filtering, a reduced cooling structure and an enclosure to replace the 25kg 48V battery. This frees up considerable space and weight and can yield €125 – €250 in R&D weight reduction incentives. The high-density power module converts the main 400 – 800V battery to 48V in a small 61 x 35 x 7mm package capable of delivering over 2kW of power with a power density of >4.3kW/in.3 (Figure 3)
Flexibility/Scalability
OEM designers try to standardize the subsystems integrated within a vehicle as much as possible to save time, money and resources. However, each varies slightly with vehicle trim levels requiring multiple designs. Because of vehicle electrification advancements, power system design teams are challenged with changing power delivery requirements. The flexible and scalable modular power system design approach offered by Vicor allows designers to implement standardized solutions across a wide variety of powertrains such as SUV, minivan or light-duty trucks.
For example, a minivan’s power requirements may be 5kW, but powering a light-duty truck with lightbars, tow and plow packages and AC power stations may require 10kW. Using the same platform and a little extra space, engineers can quickly add or remove prequalified parts to the array to scale power up or down.
Modularity also offers additional levels of flexibility by enabling distributed power architectures from a 48V bus. Power modules can be placed in convenient locations for localized 48V/12V conversion – behind the glove compartment, near the trunk or by each wheel. Deploying a modular solution delivers not only design flexibility, but a better way to streamline power changes and the manufacturing process.
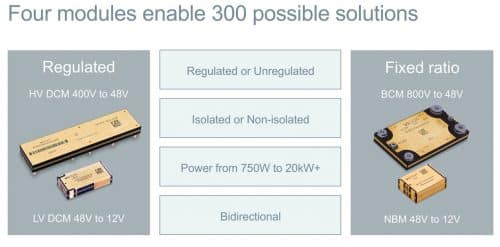
Re-Usability
One of the most common delays in vehicle development is the qualification and approval of electronic components used in the vehicle. Sometimes the process can take up to two to three years to qualify and PPAP a single component. R&D teams look for ways to reuse what they have to save development and qualification time, conserving valuable resources.
For example, a traditional PDN based on a discrete DC-DC converter design can consist of over 200 bulky components, whereas Vicor advanced technology provides a single high-density power module. The time savings for an engineering design team is significant when qualification is required for one module versus 200+ individual components for the same function.
Additionally, the Vicor modular approach allows engineers to achieve approximately 300 combinations of power delivery by using just three to four scalable building-block modules of various types. (Figure 4) This design approach amounts to hundreds of hours of time and resource savings, allowing OEMs get out in front in the electrification race.
The final lap
OEMs are facing daunting challenges not just to cross the electrification finish line, but also to finish with an xEV fleet that will deliver long-term results. Utilizing a modular power system design approach can provide a competitive advantage in this critical market-share race. Innovation is needed now in the form of new architectures and topologies that deliver the highest performance today and also can be re-used and reconfigured for the future.
Conventional power designs cannot meet this level of flexibility and ease-of-use. The best way for OEMs to meet their aggressive electrification goals is to adopt a modular approach that delivers the highest performance on a number of critical levels, and enables them to meet the most complex xEV power demands.
YS Jun is the Director of Automotive Business Development for Vicor APAC.
Vicor Corporation, the leader in high-performance power modules, solves the toughest power challenges for our customers, enabling them to innovate and maximize system performance. Our easy-to-deploy power modules provide the highest density and efficiency enabling advanced power delivery networks from the power source to the point-of-load. Headquartered in Andover, Massachusetts, Vicor serves customers worldwide with unequaled power conversion and power delivery technologies.