NGOs, investors, waste management practitioners and environmental conservation groups should recognise waste plastics as a resource for a clean renewable energy, and join hands with the plastic-to-fuel innovators to develop more pioneering technologies that produce ultra-clean emissions and replace fossil fuels.
“Nowadays people know the price of everything and the value of nothing.” —Oscarwilde
The archaeological timeline of human evolution shows how we have organised ourselves through the Stone Age, Bronze Age, Iron Age, and Polymer Age. These ages have proved that we can blend and amend natural resources and turn them into desirable materials. In this Polymer Age, we are showcasing that apart from blending and amending, we can manipulate the structure of chemicals and create artificial products. The versatility of plastics finds tremendous application in all household and consumer products, thus playing a major role in domestic and industrial areas.
The growth in use of plastics in products ends up with wastes that are non-biodegradable, thus becoming an environmental hazard. Plastics with polystyrene and polypropylene become a major problem because these cannot be recycled. Even when means to recycle them are found, their saleable value being very little, recyclers throw these plastics into landfills. As plastics never decompose, the landfills become a major environmental concern.
Plastic debris is also polluting the oceans and has become a major detrimental factor to vulnerable aquatic lives. Ellen MacArthur Foundation, in partnership with the World Economic Forum, has estimated that by 2050 oceans will have more plastics than fish. We, as global citizens, need not become extremists and call for an absolute close to plastic production, Let us understand that plastic is not the problem but its way of disposal is the main concern. Actually, we desperately need a paradigm shift in perceiving things. Let us be aware that plastics are a solid form of oil. So let us keep the plastics in the supply chain and work together to break the misperception of plastic wastes, which can be a valuable sustainable fuel.
Why is WTE unsuccessful in India?
Waste-to-energy (WTE) plants installed in the USA and European cities have now made them the most sustainable and eco-friendly cities. The solid wastes used in these plants are materials that cannot be recycled, but the plants recover the energy from these wastes either in the form of heat or electricity. When these cities have proved a proportional relationship between WTE plants and sustainability, unfortunately, in India, many WTE plants are being shut down due to environmental violations.
Some reasons behind this failure on our part are:
- Our WTE plants do not segregate the solid wastes, so wet wastes get mixed with dry wastes and reduce the calorific value of the wastes.
- The high organic content in the wastes is another factor that decreases their calorific value.
- Some wastes are highly inert, and the high moisture content in the wastes decreases the quality of it. Hence, incineration plants are unable to burn the wastes completely. In fact, most of the wastes are unfit for incineration.
- Unsegregated wastes require an excessive amount of fuel to burn. So, the cost of energy per unit from our WTE plants is high. Like the USA and European landfills, Indian landfills should learn to accept only non-recyclable and non-biodegradable wastes, and incineration should be done by grate combustion technology.
Successful Indian companies that turn end-of-life plastics to fuels
When WTE plants have shown their downsides, waste plastics have come as the light at the end of the tunnel, enabling us to move forward and transform end-of-life plastics to renewable fuels by adopting simple and cost-effective ways. The growing interest in creating something different from plastic wastes has led to many methods that turn plastics to fuel(s). Plastics are considered to be toxic, but by following proper waste management techniques, these can be vaporised rather than burnt and oxidised. A brief account of some companies that are successfully turning waste plastics to sustainable fuel(s) is given below.
Indian Institute of Petroleum (IIP), Dehradun, under the umbrella of Council of Scientific & Industrial Research (CSIR), has set up a plant that is the first by a government research institute in India. It converts waste plastics into useful hydrocarbons like petroleum or diesel using pyrolysis method. In this method, the segregated plastic wastes are not burnt but heated in the absence of air, so that the complex hydrocarbons are broken to small molecules. A right combination of catalysts is added to these small molecules, which are then converted to valuable hydrocarbons in vapour form. This vapour is then condensed to get the final products such as gasoline, diesel, or aromatics, in liquid form.
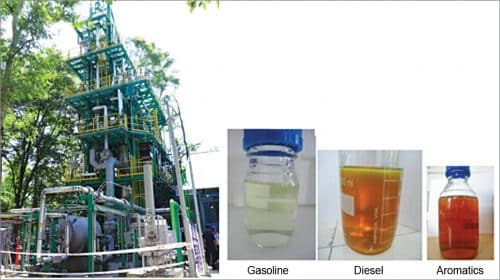
The IIP plant is capable of converting one tonne of plastic wastes to 850 litres of diesel, or 700 litres of petrol, or 500 litres of aromatic products. The obtained fuels are free from toxic substances and are thus completely environment friendly. The final IIP products are welcome by Indian Railways because these have zero sulphur and therefore meet the Euro-III standards. The aromatics are rich in BTX.
Agile Process Chemicals (APChemi) is a leading solution provider in following the technology of chemical recycling via pyrolysis. The company is one among the eleven winners of the Asia-Pacific End Plastic Waste Innovation Platform, which supports the innovations of the startups in ending waste plastics, conducted by Alliance to End Plastic Waste & Plug and Play.
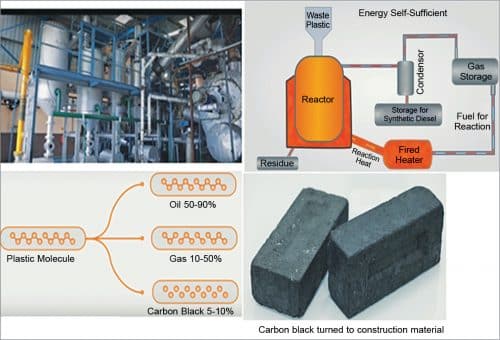
At APChemi, the plastics from the municipal solid wastes are thoroughly washed, dried, shredded and then fed into a gas-powered reactor where the plastic, which contains complex hydrocarbons, is broken down using heat to its molecular level. It yields oil and gas that are clean and efficient hydrocarbons, which serve as fuels and petrochemicals, thus reducing the dependence on crude oil and paving the way to an ecological circular economy.
The only waste product in the pyrolysis process is the carbon black. However, APChemi has successfully converted this pyrolysis waste to solid sustainable construction material. APChemi’s plant successfully converts 75,000kg of end-of-life plastics per day, and more than eighty percent of the polymer hydrocarbons become sustainable energy products. The output hydrocarbon oil is further fractionated into petrol, diesel, and jet fuel that can run petrol and diesel engines. This oil also finds many industrial applications such as the generation of steam, hot water, hot air, or for heating thermic fluid. The oil and the gas can be used in internal combustion engines to produce electricity.
Rudra Environmental Solutions has bagged the Dynamic Asia Global Award for its outstanding contribution to the recycling industry. Rudra uses the process called Thermo Catalytic Depolymerisation (TCD) in which shredded plastics are heated at 380°C to 430°C in absence of oxygen. A catalyst is used to crack the polymer chain, thus producing hydrocarbon vapours, which are condensed. The condensed vapours produce a fuel called polyfuel, and synthetic gases called syngas. The polyfuel undergoes filtration before collection, and the syngas is also cleaned before using in a reactor.
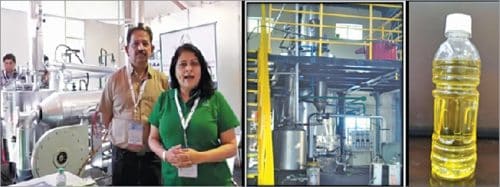
At Rudra, each tonne of plastics produces 600 to 650 litres of polyfuel, which is used in boilers, furnaces. etc. Efficiency of syngas, which is used for heating the reactor at Rudra, is 20% to 25%. In this process, no harmful gases or effluents are generated. The end product yields a residual char, which is a non-hazardous waste that can be used as a road filler along with bitumen.
The advantage of the method followed at Rudra is that plastic wastes need not be presorted, cleaned or dried before processing. This reduces the overall cost of operation, the process is eco-friendly, and the final output yield is not only energy-efficient but also has a negative carbon footprint.
PolyCycl Private Limited has won the Indian Innovation Initiative award from the Confederation of Indian Industry (CII) for making an impact towards sustainable circular economy by converting waste plastics to high-value petroleum fuels. PolyCycl has also been chosen as one among the eleven winners of the Asia-Pacific End Plastic Waste Innovation Platform, from Alliance to End Plastic Waste & Plug and Play, for innovative ideas from startups in efficiently making use of the plastic wastes.
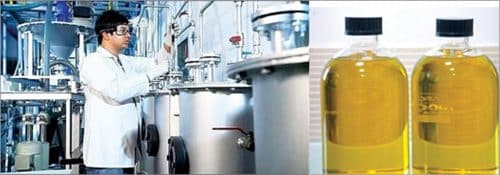
Amit Tandon, founder of PolyCycl, strongly believes that producing high-value fuel and adopting low-cost extraction technology are the two main factors to increase the plastic-to-fuel conversion. The plant at PolyCycl adopts Contiflo Cracker extraction technology that uses a patented continuous process to generate distillate fuels, which can be used in industrial boilers and furnaces. In the process of converting waste plastics to liquid fuels and gas, PolyCycl achieves an efficiency of 95%. For every tonne of waste plastics, PolyCycl plant produces 5.8 to 6.4 barrels of liquid fuels. In short, for every ton of plastic wastes the yield is 850 litres of lighter distillate fuels.
According to PolyCycl, extracting fuel from waste plastics using a batch-based approach is not only tedious but gives an output that is of low-value; whereas the fuels generated from PolyCycl’s process are lighter, less viscous and high in GCV (global value chain), thus making them highly effective and valuable. These fuels require no further distillation and are ready to be sold as a substitute for industrial diesel.
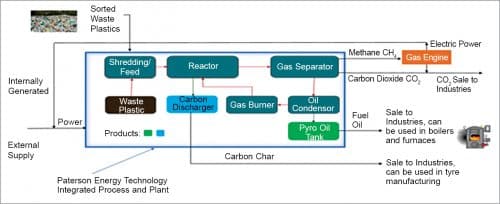
Paterson Energy provides a wholesome solution to plastic wastes through a sustainable and eco-friendly mechanism. Paterson uses continuous Thermo Chemical Depolymerisation (TCD) in its recycling plant to break the large plastic molecules, which yields a fuel named by them as ‘verte-x’ that is free from sulphur-like toxic elements. Verte in French means ‘green,’ and as the fuel finds many industrial applications, the company has added an ‘x’ to it.
Paterson produces 600 litres of verte-x from one tonne of plastic wastes. The carbon black residue is used as a replacement of coal. Verte-x can be used as a fuel in generators to produce electricity, in marine engines, in casting furnace, or any other plant that requires heat or electricity.
MK Aromatics, a manufacturer of various aromatic hydrocarbon solvents, also provides a technical solution to synthesise waste plastics or multi-layered plastics like sachets. The company uses a completely automated method where there is no need to segregate or wash or dry the plastics. The plant converts seven to ten tonnes of collected waste plastics per day.
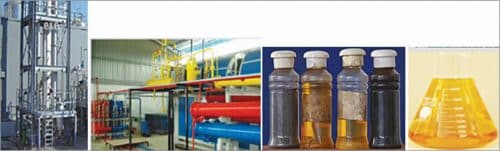
At MK Aromatics, the collected waste plastics are loaded on a conveyor belt that leads to a rotary drummer, where the dust and dirt get settled at the bottom and diverted to a compost pit. The dust-free plastics are collected, bailed and then fed into the loading press.
The hydraulic cylinder in the press pushes the plastic into the reactor, which operates between 350°C and 450°C, where the plastic is melted and vaporised. The resulting vapour from the reactor is then condensed to get crude oil, which can be further distilled to get various derivatives of hydrocarbons. The non-condensable gases like methane, butane and propane are recycled back to the reactor and used as fuel for the reactor.
This method is eco-friendly and energy-efficient as fuels are produced without any emissions and effluents. The fuels produced by MK Aromatics are used by well-known companies like Unilever and Britannia to energise their plants.
Conclusion
Companies mentioned above and some other companies, or individual innovators who are not mentioned, are creating a long-term promise by changing end-of-life plastics to valuable renewable fuels in a sustainable and environment-friendly way. The huge amount of money we have spent as half-measures on WTE plants is in a black hole now. The investments and the efforts made by these plastic wastes-to-energy companies will substantiate the principle ‘in for a penny in for a pound.’
Reliance Industries plans to become one of the world’s leading new energy companies by creating value from plastic wastes that yields a clean, affordable energy and makes carbon-dioxide a recyclable resource. State governments, NGOs, investors, waste management practitioners and environmental conservation groups should recognise waste plastics as a resource for a clean renewable energy, and join hands with the plastic-to-fuel innovators to develop more pioneering technologies that produce ultra-clean emissions and replace fossil fuels.
With the support of the government, we expect that the conversion of waste plastics to energy in all states of India will show a sharp rise in the following years and thus promote our country’s economy. By doing so, we are not only moving towards the circular economy but also bringing more benefits to the environment to create a win-win for all.
Dr Krishna Naga works as a Physics teacher. She has over twenty years of experience in this field. Her hobbies include reading and writing
I think it is true some progress is being made to achieve waste management. However, I think corporate lobbies in India derail plans to develop inclusive policies as they might ruin the spoils they accrue from current frameworks.
There is need for a systems change