Researchers at MIT have discovered an affordable and simple method to boost the strength of crucial materials used in diverse applications.
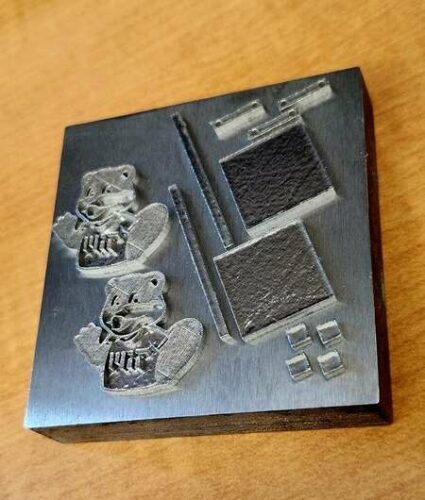
For aerospace and energy applications, materials need exceptional resilience to withstand extreme conditions like high temperatures and significant tensile stresses without failing.
Researchers at the Massachusetts Institute of Technology (MIT) have discovered a straightforward and cost-effective method to enhance the strength of a crucial material commonly employed in various applications today. The team thinks their approach, using 3D printing with ceramic nanowires, can enhance various materials.
Toward better performance
Using Inconel 718, a popular “superalloy,” the team combines it with ceramic nanowires, resulting in the nano-ceramic coating on the metal’s surface. The powder is used for laser powder bed fusion, a 3D printing method. Layers of powder are melted with a laser in a specific pattern, repeating with each new layer to create complex 3D parts. Parts made with the new powder have less porosity and cracks, resulting in stronger, stretchable, and radiation-resistant parts. The process is cost-effective, compatible with existing 3D printers, and improves performance. The process enhances thermal resistance, strength and eliminates flaws. The researchers believe this technique can benefit future 3D printing of metal alloys, including high-reflectivity copper and fracture suppression in superalloys.
A huge new space
According to the researchers, the rapid cooling rate of ultrathin 3D-printed metal alloy layers creates a significant opportunity for alloy design. This process surpasses the cooling rate of conventional melt-solidification methods used for bulk parts. Consequently, the traditional rules governing chemical composition in bulk casting do not hold for this type of 3D printing. This breakthrough allows for a broader range of compositional exploration, particularly concerning the base metal with added ceramics. The team believes that this advancement has the potential to open up vast new possibilities in alloy design. The researchers find the initial results exciting and plan further exploration of Inconel composites for resilient materials in extreme conditions.
The researchers highlight the immense potential of 3D printing for materials design, especially in the nuclear, aerospace, and energy sectors, with promising early results.
Reference : Emre Tekoğlu et al, Strengthening additively manufactured Inconel 718 through in-situ formation of nanocarbides and silicides, Additive Manufacturing (2023). DOI: 10.1016/j.addma.2023.103478