Discover how a collaborative effort is set to drastically reduce carbon emissions and transform pollution control in the chemical industry.
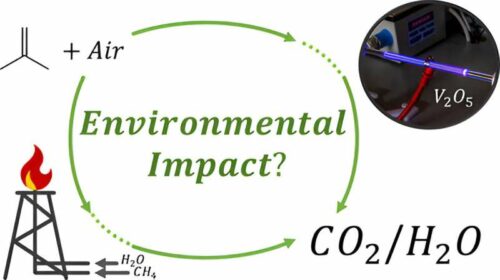
Scientists from the University of Nottingham’s School of Chemistry, industry partner Lubrizol, and the University of Warwick have unveiled a solution to tackle industrial pollution head-on. Their innovation—a nonthermal plasma electric flare stack—has the potential to drastically reduce carbon emissions compared to the conventional gas flares currently employed by oil refineries for pollution control. Gas flare stacks have long been the industry standard for managing the disposal of volatile by-products in oil recovery, casting their eerie glow above refineries and chemical plants. However, recent revelations suggest that these gas flares’ environmental and health impacts are more significant than previously believed.
Pollutants released during flaring, such as PM2.5, Ozone, NO2, and benzo(a)pyrene (BaP), have been linked to a range of health issues, including strokes, cancer, asthma, and heart disease, according to international experts, including the World Health Organization (WHO). The innovative electric flare stack developed by this collaborative effort promises to be a game-changer. By eliminating the need for the fuel source, gas isobutylene, the “electric flare stack” consumes a remarkable 6.6% less energy than its steam-aided methane flare counterpart, resulting in CO2 emissions reductions ranging from 2.0× to 11.4× lower. This technology not only offers a more environmentally friendly solution but also helps reduce the industry’s carbon footprint.
The overarching goal of this partnership is to develop cleaner and more sustainable chemical processing methods to support the government’s carbon-neutral targets. The team emphasises the significance of such collaborations in driving sustainability and innovation within the chemical industry. They see this groundbreaking solution as critical to improving the sector’s environmental performance and envisions further exploring the technology’s scalability in petrochemical flaring. They underscore its potential to help manufacturing plants meet their ecological responsibilities without relying on natural gas combustion, which could reduce scope one emissions. The collaboration reflects the industry’s determination to explore the broader applicability of nonthermal plasma technology for destroying volatile organic compounds (VOCs). In an era where sustainable solutions are paramount, the nonthermal plasma electric flare stack emerges as a beacon of hope, promising to reshape the landscape of pollution control and environmental stewardship in the chemical industry.