Researchers at Stanford University have achieved a milestone in replicating human skin healing with self-aligning sensors.
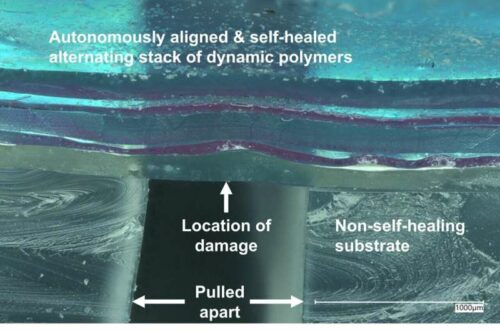
Human skin is incredible. It can detect temperature, pressure, and texture while exhibiting elasticity and resilience. Moreover, it serves as a protective shield, safeguarding the body against external dangers such as bacteria, viruses, toxins, and ultraviolet radiation. Engineers aspire to create synthetic skin for robots and prosthetics with similar qualities.
Researchers at Stanford University have achieved the initial showcasing of a self-aligning, multilayer thin film sensor, which marks a significant milestone in replicating the healing mechanism of human skin. Layering is crucial for emulating skin’s properties. When punctured or cut, each layer selectively heals, restoring overall function, similar to real skin. The team aims to develop multi-tiered synthetic skin, each layer as thin as a micron. Stacked layers, thinner than a sheet of paper, can sense pressure, temperature, and tension, with different materials engineered to detect thermal, mechanical, or electrical changes.
A novel approach
Global interest in multilayer synthetic skin persists. Their unique feature is the self-recognition and alignment of layers during healing, restoring functionality layer by layer. Other synthetic skins require manual realignment, risking compromised recovery. Materials hold the secret. Layers have chains with hydrogen bonds, like DNA, stretching without tearing. Rubber, latex, and synthetic polymers work. Design structures and choose combinations for each layer. The researchers used PPG (polypropylene glycol) and PDMS (polydimethylsiloxane, better known as silicone) , a rubber-like, biocompatible material. They mix with particles for electrical conductivity. The polymers and composites are immiscible but adhere through hydrogen bonding, creating a durable multilayer material. Both polymers soften and flow when warmed, solidifying as they cool. By heating the synthetic skin, researchers accelerated healing. Healing takes a week at room temperature, but at 70°C, self-alignment and healing occur in 24 hours.
A step further
The researchers added magnetic materials to their polymer layers. The synthetic skin can now self-assemble and heal. Magnetic field-guided navigation and induction heating enable shape-changing soft robots. The long-term vision is creating devices that autonomously recover from extreme damage. The researchers aim to minimize layer thickness and develop functional variation in layers. The current prototype detects pressure, but additional layers could sense temperature or strain. In the future, the team envisions robots self-assembling inside the body for non-invasive medical treatments. They also foresee self-healing electronic skins that provide robots with touch and form-fit capabilities.
Reference: Christopher B. Cooper et al, Autonomous alignment and healing in multilayer soft electronics using immiscible dynamic polymers, Science (2023). DOI: 10.1126/science.adh0619. www.science.org/doi/10.1126/science.adh0619