We often take electronics devices for granted. Be it while dropping your mobile phone from your bedside table, or a sudden jerk while driving your car or even while watching TV or playing a game. We are living in a digital world and we face several situations like the above in our daily life. No matter how many times we drop a remote on the ground, we still positively expect it to work. There is not even a single time we assume that there could have been an electronic failure. Unknowingly, electronics devices won our confidence to such an extent that we believe that everything is going to be alright and we can move on.
How are we able to do this?
Someone, somewhere is anticipating these situations of the phone hitting the floor, a device getting wet in rain, remotes, laptops and tablets falling down, cars hitting bumpy roads and so on. These are factors that are being considered while they are designing these devices.
However, we must remember that considering today’s rapid product development and time-to-market pressures, engineers find that there isn’t a lot of time to even perform reliability tests. And to top it all, there is a demand to do this in a lower cost. So we are asking for safety and reliability of quality products at low cost. So, how do engineers ensure that their products are dependable when reliability testing and possible redesigns are not only time-consuming but also expensive?
To account for these uncertainties, there are several factors that needs to be accounted for by increasing design margins. At the same time, in order to ensure safe operating conditions, the regulations are also getting more stringent day by day.
Engineers have to design and test these devices multiple times with multiple scenarios including dropping these devices from different heights and at different angles. The devices also need to be subjected to diverse environments with different temperatures and moisture and also to sudden shocks. They must also finally ensure that the electrical circuitry is working as intended, meeting regulations and reliability constraints and all this at much cheaper cost.
There is a lot of additional cost that is involved with all of the above and it is obvious that the prices will go up. So, is there any alternative to reduce the cost and still account for all of the above scenarios?
The simulation way
This is where simulation comes in. Engineers and designers across the globe are using virtual testing and simulations to account for all these uncertainties without physically testing the device there by reducing the overall design and production cost.
Without doubt, the key to reliable products is to employ design for reliability (DfR) methods. It is a process that warrants that a product, or system will perform a specified function, within a defined environment over an anticipated lifetime. DfR takes place at the design stage when engineers start assessing a concept’s feasibility. This is way before the construction of physical prototypes. It is often part of an overall design for excellence (DfX) strategy. In addition to the obvious mechanical considerations, DfR needs to consider Electrical/software reliability, Supplier and part selection, Design for manufacturing (DfM) and also the Physics of failure (PoF) analysis/modelling.
To ensure that product reliability meets customer expectations, engineers must establish the desired product lifetime and performance during the concept phase itself. This important step drives the thinking behind every decision throughout the product development process. Engineers also have to ensure that products meet the specification standards throughout the industry.
Design for manufacturing is the process of ensuring a product can be consistently manufactured by the designated supply chain with a minimum number of defects. DfM includes a variety of tools and processes.
We are not even bringing up the total time saved for the design here as that is a given.
As an engineer helping customers worldwide in creating virtual testing environments with comprehensive Ansys electronics simulation, I started realizing that simulation is getting placed in the front seat to test all possible scenarios in which failures occur using a computer, rather than creating prototypes and testing devices. Can you imagine the time, cost and effort that is saved due to this? We no longer need to create multiple prototypes for testing that could take months.
One strong reason behind this is being able to simulate electrical, thermal and mechanical behaviour of these devices not only in isolation but also considering the coupled effect. In the past, this was never easy and there was always a gap between what the real scenario is and what is being simulated. Another strong factor is the ability to simulate all in one environment. An electrical engineer or PCB designer can simulate the maximum voltage drop and the associated temperature rise couple with the reliability of the trace all in one environment (Ansys Electronics Desktop).
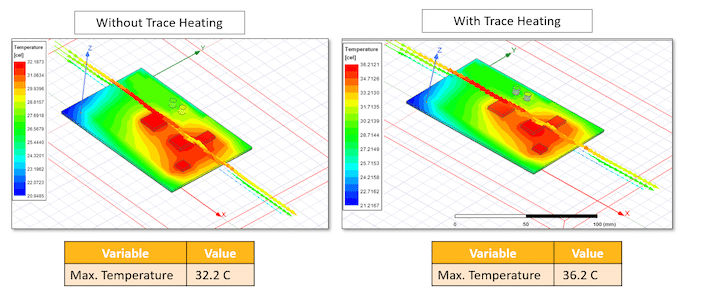
Ansys Electronics Desktop not only makes simulation easy, but also provides wizards for streamlining individual flows. This makes it easy for individual designers for setting up a thermal problem just by continuing with the electrical analysis in a few clicks. Of course, once the initial judgement is taken for the feasibility of the design, there are options to co-work with the thermal engineer in the same environment and test different what-if scenarios such as maximum current capacity of trace and trace reliability etc. To add to this what-if analysis, there are optimization modules such as Ansys Optislang that can help to optimize designs within given manufacturing constraints.
A single device failure can ruin your brand. Ansys comprehensive multiphysics models reliably predict how a design will behave. From concept design onwards, researchers can test a prototype in numerous situations. This means that experimenting early and often and failing takes place while changes are inexpensive to make, thanks to simulation.
Systematic testing includes reproducing the simulation for a large number of specific geometries and material properties.