Intelligent power management system and enhanced DC-DC converter powers the inverter-motor combination to achieve high-performance
When it comes to beating time with increased vehicle speed in a scenario such as race car driving, it becomes essential to use an electric motor that boosts the internal combustion engine (ICE) performance and enhances vehicle acceleration.
Accomplishing this is a new battery pack with associated electronics designed by Delta Motorsport.
The new 48V lithium-ion-based battery pack has an innovative intelligent power management and high-power-density DC-DC converter and regulation system. The battery pack powers the inverter-motor combination and also accepts regenerated power from it, while the high-power-density converter solution powers all the car’s electrical circuits and devices. The level of power density and power management achieved by this architecture allows the removal of the alternator system, which leads to improved weight, performance and reliability.
The battery pack includes a battery management system that controls all the cell voltages and ensures that the battery handles the maximum possible charge and discharge voltages at all times while communicating with the motor-inverter controller. It continuously calculates and updates the controller on how much current the battery can supply or accept, based on its state of charge (SoC). So, power demand must be reduced at a low SoC, while regeneration must be limited at a higher SoC.
The system also monitors the temperatures of all available cells in real-time and feeds the results into the available power calculations. Additionally, it can open contactors to isolate the battery pack safely if a problem arises.
Better Motor Power
The system achieves compact size, lightweight and high performance by utilising a modular power delivery network (PDN) that incorporates a 48VDC power source that is fed to four parallelly connected DC-DC converters, which together supply regulated 13.8V power at up to 92 amps (approximately 1.2 kilowatts of power). The load is shared by the four converters, although it can be fully supported by just three, i.e., N+1, or aviation-level redundancy.
The hybrid system’s 3-phase brushless motor connects to the battery through a bidirectional inverter that routes battery power to the motor and regenerated power from the motor back to the battery.
The motor drives the vehicle in pure-EV mode (motor only, no ICE) during its initial, speed-limited journey down the pit lane, then in mild-hybrid mode (together with the ICE) when the driver demands a performance boost during the race.
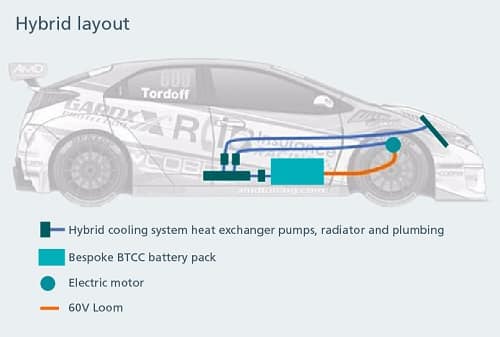
DC-DC Converter Power Modules
The battery management system supports data logging and diagnostics for logging the DC-DC converter’s performance. This is not only to check fault status but also to provide feedback on the exact amount of current being delivered on all vehicles.
The DC-DC converter power system uses four DCM3623 isolated, regulated DC-DC converter ChiP power modules by Vicor to deliver a regulated 13.8V output from the battery pack with current levels up to 92 amps. Due to their low profile and small footprint, they are mounted in direct thermal contact with the micro-bore cooling plates that extend between the battery cells.
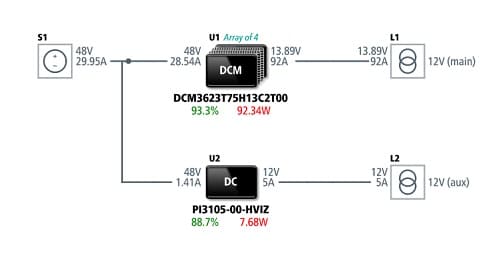
The DCM modules’ scalability and ease of paralleling enable the modular power architecture, that further allows customisation of the DC-DC PDN to a small footprint without sacrificing power.
Delta Motorsport also used a Vicor PI3105, a small 60W isolated converter for an uninterruptable power supply (UPS), which supplies power to the battery pack electronics in order to maintain the safety systems when isolated from the vehicle power supply. The UPS also allows the electronics to be powered independently of the vehicle, enabling remote connection for systems checks.
Forthcoming Plan
Future electric vehicles will inevitably need smaller, lighter and higher-efficiency power electronics to handle increasing performance demands. As manufacturers migrate to 48V batteries to handle this elevated power, the above modular approach can improve power delivery network efficiency, reducing power losses and weight with smaller, lighter cable and connectors.
It is expected that high-performance mild-hybrid vehicles based on the above technology will be featured in the British Touring Car Championship (BTCC) 2022 and thus add a new dimension to the championship.