A team of researchers from Rice University and Harvard University demonstrated that it is possible to fabricate programmable, nonelectronic circuits that could control the actions of soft robots using compressed air
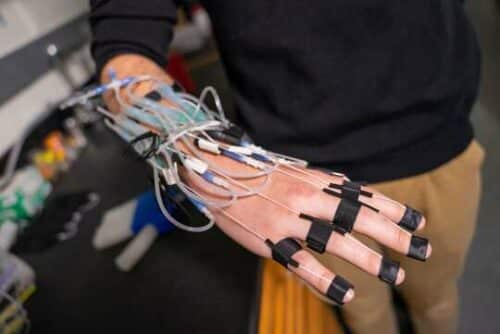
Presently, soft robots or wearables need to be programmed for every simple work to be carried out, hence, researchers are finding ways to design a cost-effective electronic control system to carry out those movements without the inclusion of electronic components. Therefore, Decker, a senior majoring in mechanical engineering, fabricated a soft robotic control system essentially from everyday materials like plastic drinking straws and rubber bands, the system’s air-driven logic gates could be configured to perform operations called Boolean functions.
“Part of the beauty of this system is that we’re able to reduce computation down to its base components,” said Rice undergraduate Colter Decker, lead author of the study in the Proceedings of the National Academy of Sciences. He said electronic control systems have been honed and refined for decades, and recreating computer circuitry “with analogs to pressure and flow rate instead of voltage and current” made it easier to incorporate pneumatic computation.
“The goal was never to entirely replace electronic computers,” Colter said. He said there are many cases where soft robots or wearables need only be programmed for a few simple movements, and it’s possible the technology demonstrated in the paper “would be much cheaper and safer for use and much more durable” than traditional electronic controls.
The team integrated two components into a single device, a piston-like actuator that translates air pressure into mechanical force and a valve that can be switched between two states—off and on. A bistable valve works similarly to a switch and uses air pressure as both input and output. A specific amount of air pressure is needed to flip the switch between off and on states. The valves are held closed by rubber bands, and they are programmed by adding or subtracting rubber bands, which changes the amount of pressure required for activation. During experiments, Decker showed the circuits could be used to control a soft, hand-shaped robot, a pneumatic cushion, and a shoebox-sized robot that could walk a preprogrammed number of steps, retrieve an object and return to its starting location.
“The biggest achievement in this work is the incorporation of both digital and analog control in the same system architecture,” said Preston, an assistant professor of mechanical engineering at Rice. Having both means the pneumatic control circuits can be programmed digitally, with the “ones and zeroes that you think of in a traditional computer. But we can also bring in analog capabilities, things that are continuous,” he said. “That allows us to simplify the overall system architecture and achieve new capabilities that weren’t accessible in prior work.”
Click for the Published Research Paper and Demo Video