Researchers have developed a new way to fabricate wearable electronic devices creating stretchable circuit pattern that can be worn directly.
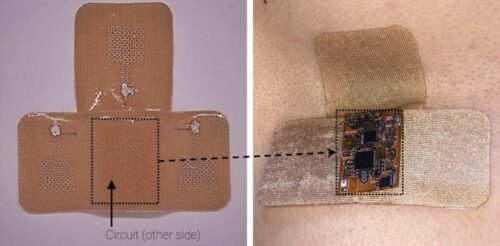
An electronic device may not look like much, but these small devices consist of thousands of transistors which are placed layer by layer in that tiny space measuring just within a few millimeters. When we take a look at the fabrication process we see how complex it actually is. Yet there is a window for development and maybe even complexity!
Researchers at the Washington State University have demonstrated that electrodes can be made using just screen printing, creating a stretchable, durable circuit pattern that can be transferred to fabric and worn directly on human skin. Such wearable electronics can be used for health monitoring in hospitals or at home.
They used a multi-step process to layer polymer and metal inks to create snake-like structures of the electrode. While the resulting thin pattern appears delicate, the electrodes are not fragile. The study showed they could be stretched by 30% and bend to 180 degrees.
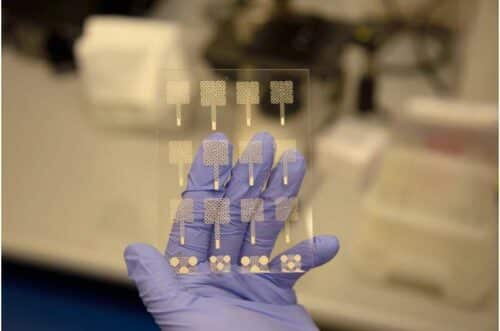
Multiple electrodes are printed onto a pre-treated glass slide, which allows them to be easily peeled off and transferred onto fabric or other material. Researchers then transferred them onto an adhesive fabric that was then worn directly on the skin by volunteers. The wireless electrodes accurately recorded heart and respiratory rates, sending the data to a mobile phone.
Researchers in their work focused on ECG measuring electrodes but the technology used to develop the technology, i.e. the screen-printing process can be used to create electrodes for a range of uses, including those that serve similar functions to smart watches or fitness trackers.
Reference : Sehyun Park et al, Fully Screen-Printed PI/PEG Blends Enabled Patternable Electrodes for Scalable Manufacturing of Skin-Conformal, Stretchable, Wearable Electronics, ACS Applied Materials & Interfaces (2023). DOI: 10.1021/acsami.2c17653